Researchers in the fields of materials science and microelectronics are looking for sustainable ways to meet the world’s demand for computer power. This can be achieved by developing microelectronics that operate at much lower voltages and require less energy. Hence, thin-film alternatives to electronic components are much needed.
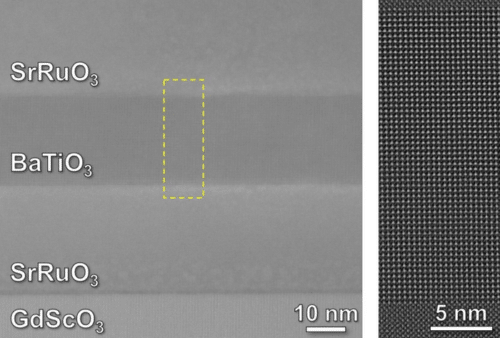
A group of researchers from Berkeley Lab and UC Berkeley have now discovered one energy-efficient method, which involves creating a thin-layer version of a well-known material with the precise qualities required for next-generation devices.
Barium titanate (BaTiO3), which was first discovered more than 80 years ago, is used in a variety of capacitors for electronic circuits, ultrasonic generators, transducers, and even sonar. The scientists found a means to make BaTiO3 films that are only 25 nanometers thick, or less than a thousandth of the breadth of a human hair. Their polarisation, or the orientation of charged atoms, shifts as swiftly and effectively as in the bulk form.
“We’ve known about BaTiO3 for the better part of a century and we’ve known how to make thin films of this material for over 40 years. But until now, nobody could make a film that could get close to the structure or performance that could be achieved in bulk,” said Lane Martin, a faculty scientist in the Materials Sciences Division (MSD) at Berkeley Lab and professor of materials science and engineering at UC Berkeley who led the work.
The researchers used a method known as pulsed-laser deposition to better understand what it takes to create the best, low-defect BaTiO3 thin films. BaTiO3 is a ceramic substance that transforms into a plasma when an intense ultraviolet laser beam is directed at it. The plasma then transmits atoms from the target onto a surface to create the film. “It’s a versatile tool where we can tweak a lot of knobs in the film’s growth and see which are most important for controlling the properties,” said Martin.
The researchers discovered a version that closely reproduced a very narrow slice of the bulk by slicing each deposited sample in half and analysing its structure atom by atom. Finally, Martin and his team produced small capacitors by sandwiching a film of BaTiO3 between two metal layers.