It exhibits good resistance to thermal cycling, making it ideally suited to applications found in engine compartments
Electrolube, the global manufacturer of electro-chemicals, has successfully developed a solution to protect the stator for a new generation of electric vehicles. The project brief required a high-performance resin material to electrically isolate the coil-ends of the stator with the ability to consistently withstand permanent contact with refrigerants. Electrolube conducted a series of resin tests with various test specimens performing under permanent contact with a mixture of different fluids, which included oil and cooling fluid, at temperatures up to +175°C for 168 hours.
In an electric vehicle, the stator is the static part of the engine whereby electrical energy is supplied via the car’s battery. When the electrical energy from the car battery is supplied to the motor, the coils create rotating, magnetic fields that pull the conducting rods on the outside of the rotor along behind it.
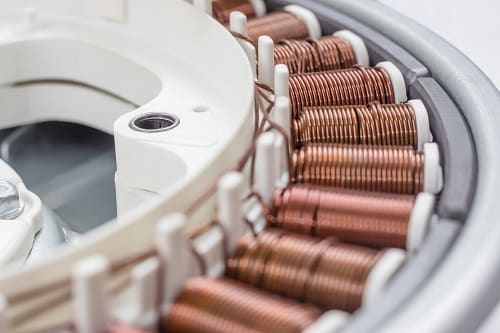
Effectively, the stator uses energy to create a magnetic field that then turns the rotor. In this particular application, Electrolube’s ER2223 resin was selected due to its excellent protection against different kinds of oil and cooling fluids widely used in today’s automotive sector. ER2223 is a highly chemical resistant epoxy potting compound that has been specifically formulated to meet the harsh operating conditions of under-hood applications in the automotive industry. It is chemically resistant to most fluids found in the engine compartment of vehicles or other mechanical applications, thereby offering superb protection to electronic components.
With an exceptionally wide operating temperature range of -40°C to +180°C, ER2223 also exhibits good resistance to thermal cycling, making it ideally suited to applications found in engine compartments. Its low viscosity allows for easy potting of the smallest or tightly packaged components and it provides excellent adhesion to a wide range of substrates. The ER2223 resin cures in an hour at 100°C, in 4 hours at 60°C and within 24 hours at room temperature.
Overall, the ER2223 black epoxy resin has proven to be a very successful solution to fully optimise the performance of the stator in next-generation electric vehicles. The increased sophistication of EV electronic systems often means they are more sensitive to contamination and adverse external environmental conditions. Moreover, as automotive electronic systems rely increasingly on their interconnection, failure in one assembly can compromise the operation of another. Unlike aerospace applications where two or three layers of redundancy may be built into these systems, automotive designs typically must work every time, throughout the life of the product.