When we talk about power applications, higher power efficiency is always the guiding factor for new technology trends. The power of electric motors is in the range of milliWatts to Megawatts. Intelligent performance along with improved efficiency of both motor and drive circuitry are the main design goals. Â When it comes to the electronics driving the motor, innovation in the following the fields of topology, power devices and integration are defining the roadmap.
Latest features in motors
Innovation is the roadmap to success and hence calls for developments in the field of motors as well. Following are some of the new features seen in motors and drives.
Sensorless Control
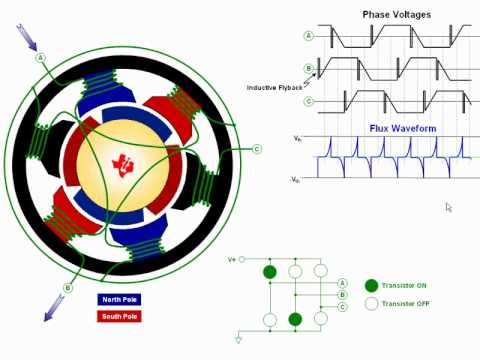
Implementation of Sensorless control of BLDC (Brushless DC) motors is seen in many of the recent applications. Elimination the rotor positioning sensors like hall sensors not only reduces the cost, but increases the reliability.
For example, the InstaSPIN-BLDC is a sensorless control technique that can get motors up and running in seconds with only a single tuning value. Unlike other sensorless BLDC control techniques based on back-EMF zero-cross timing, InstaSPIN-BLDC monitors the motor’s flux to determine when to commutate the motor.
Integrated Solution
Solutions which consume lower power (around and less than 50 watt) are now available with integrated power devices and state machine to control. For example, DRV10983 a three-phase sensorless motor controller with integrated power MOSFETs can provide continuous drive current up to 2 A.
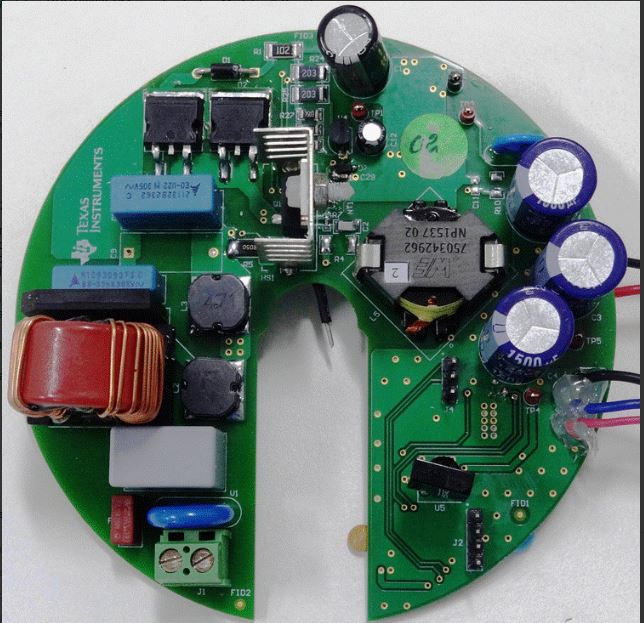
With integrated state machine, driver and power MOSFETs, it uses a proprietary sensorless control scheme to provide continuous sinusoidal drive, which reduces the pure tone acoustics that typically occur as a result of commutation. The interface to the device is designed to be simple and flexible. EEPROM is integrated in the DRV10983 as memory for the motor parameter and operation settings.
Automatic Tuning
Running the driver in stepper motor application requires tuning. If manual tuning is used, it is very difficult to find the accurate point to set while tuning. TI’s automatic stepper motor tuning feature known as AutoTune can adapt to changes in system inputs or motor characteristics without the user having to apply any type of parameter tuning.
Taking on the challenges
   These sensors are at times not as accurate as we would like, which can reduce performance and often the efficiency of the motor. Another problem with position sensors is their reliability as they regularly fail over time.  When they do, the motor is often dead under traditional control schemes that rely on this sensor. Hence newer features become a necessity.
Implementing sensorless control
To implement features like sensorless control, automatic and integrated state machine logic to control the motor, it requires highly smart algorithms to control the system. These should follow the theoretical mechanism to spin the motor. Besides it should take care of practical faults that might rise during operation.
For examples, motivation behind sensorless control is the applicability with the end usage. Motors typically include what is called a position sensor, which can identify the position of the rotor (the moving part of a motor). Identifying the rotor position is essential for control of the motor at various speeds and under changing loads.
Reliability in speed control
One of the innovative uses of motors in applications today (such as air conditioners, refrigerator compressors, washing machine and cooling fans) is to drive and control a motor at variable speeds and even turn the motor off at times to improve product efficiency. The motor must be able to then start back up quickly and reliably 100 percent of the time. This has allowed manufacturers to improve the reliability of their products, improve efficiency by using variable speed motor technology and eliminate costly position sensors from their system.
Kilby Labs engineers developed and patented a sensorless control algorithm that turn the power electronics into ‘smart’ gate drivers and eliminate the need for a position sensor. The end result is a more reliable motor system that will start a motor every time under full load conditions.  The system also continues to drive and control the motor as the load and speed performance change as required by the application.
What features to look forward to?
As we move ahead, improving efficiency will always be the focus. New semiconductor technologies like Gallium Nitride (GaN), Silicon Carbide (SiC) and such might enable in reaching higher efficiencies.
Apart from efficiency, Total Harmonic Distortion (THD) is also a concern in motor driving applications. Currently passive filtering is used to mitigate this effect. But this is bulky, can introduce resonance based on load. To increase the system performance, combining active and passive methods (hybrid) or pure active methods are the feasible solutions. Developing suitable harmonic mitigation solutions become quite vital for complying with the new and future standard regulations
Motors and Drives are moving towards smaller, smarter, safer and faster solutions. IoT (Internet of Things) is emerging in industrial, personal electronics and automotive applications. In all home automation and industrial applications, motor drives will be integrated with RF chipsets for remote control. This enables remote diagnostics of the motor drives as well.
Inputs from Naveen Bevara, Analog Applications Engineer, Texas Instruments (India) Pvt. Ltd. and Anatya Vallabh, Technical Sales Engineer, Texas Instruments (India) Pvt. Ltd.