In the highly competitive world of system design, there are times when you face a challenge that seems impossible to tackle with conventional wisdom. What if you could use your humble automotive solution to tackle a military design challenge? What if a Raspberry Pi could do it too?
P. Chow Reddy, manager-R&D (Power Division), ICOMM Tele Limited, spoke to Abhishek Mutha of EFY on designing solutions deduced from existing solutions in other disciplines
Q: What are the most exciting trends in R&D?
A. There is immense requirement of USB, Internet connectivity and RS232 in power distrib
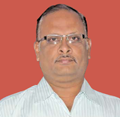
ution boards (PDBs) and automatic changeover against mains failure (AMF) panels for their access to the media and system connectivity. Apart from this, I have identified the utility of ruggedised, dedicated computing systems for military applications. For all military applications, one single solution would be Raspberry Pi.
Q: What makes Raspberry Pi work for such serious applications as in military and defence?
A. We have been working on Raspberry Pi. It consumes less power, and is virus-free (since it is Linux-operated) and rugged (as it uses solid-state memory in the form of a SD card compared to a hard disk). It is small and minimally configured, and can fit into a small cabinet or on the back of a monitor. Its HDMI is faithful enough in giving a marvellous picture quality. Above all, it is very inexpensive and customers accept it.
Q: What kinds of Raspberry Pi projects could help design engineers?
A. We have raised proposals of the projects based on Raspberry Pi. In parallel, we have also developed a small application that involves data storage memory, display, RS232 and input/output (I/O) port handling. All this is operated on Python and has been found to be operating up to the mark. One thing that an engineer has to keep in mind is that it lacks real-time clock (RTC).
Personally, I am very keen on using Raspberry Pi for military applications. There are numerous other applications and fields where it can be utilised. It has a big future ahead and if its cost reduces further to the declared figure of $25.00, one can think of replacing microcontrollers with Raspberry Pi.
Q: Could you elaborate on incorporating USB, Internet connectivity or even RS232 in PDB and AMF panels by utilising a Raspberry Pi?
A. AMF is used for changeover from mains to a diesel generator (DG) set and vice versa depending on the conditions. In these panels, USB is required to store the logged data like power fluctuations, DG run time and fuel filling updates to estimate the consumption at all load levels. All this is saved into a pen drive.
When it comes to RS232, I personally would require it for communication between other panels, LCD instrumentation displays and annunciation through GSM/GPS. Internet connectivity is used to take the stored data for a view on the performance of the panel, loads and power sources. All this exists as hardware in Raspberry Pi. Additionally, all the logical decisions, and activation of relays, contactors and solenoids are possible through software.
Q: Could you tell us about a recent cost-effective solution developed by your team, deviating from existing approaches?
A. Mil-grade air-conditioners are designed and manufactured in monopoly by very few companies. These are costly and use hermetically sealed compressors that are designed and integrated into the application cabinet to withstand vibration, dust and harsh climatic conditions.
I have come up with a cost-effective solution based on a pre-existing automotive solution. It comprises an existing automotive air-conditioner compressor and an AC induction motor for driving it. The motor can be controlled to operate for a select temperature required in the cabin. These compressors can sustain dust, high temperatures and vibration. Leakage of R-134A gas from the compressor is also almost impossible for applications in shelters. This serves the purpose in shelters as well, as it is a cost-effective solution.
Q: What were the biggest design challenges faced while re-engineering the system for a military application?
A. In military applications, the compressor must withstand the following conditions:
High temperatures. According to MIL-STD 461E, the compressor should withstand up to 55°C. This temperature range is already available in a vehicle’s engine with temperature running up to 100 degrees centigrade.
Dust test. The compressor is already proven to dust of all terrain conditions where the vehicles run around and still perform without any hindrance. This explains why I use it in my solution.