During manufacture, testing adds to the cost of the final product significantly. Sometimes the cost of testing can be even greater than the cost of product manufacturing itself. Test and measurement manufacturers have been quick to respond by coming up with innovative ways to lower the test cost and increase throughput
UMA GUPTA
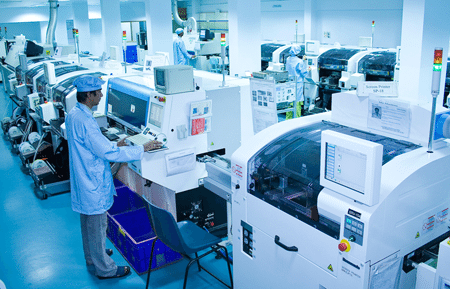
DECEMBER 2011: Testing is a critical component of product development and production process. It can improve a product’s performance, increase quality and reliability, and lower return rates. It is estimated that the cost of failure decreases ten times when an error is caught during production instead of the field, and decreases ten times again if it is caught in design instead of production. By catching these defects and collecting the data to improve a design or process, test delivers value to an organisation. At the same time, manufacturing tests add to the cost of the final product. So it’s time to drive innovation into this process through technology insertion and best-practice methodologies in order to generate large efficiency gains and cost reductions.
Testers used
Manufacturing a product involves a lot of in-line equipment. In a surface-mount technology (SMT) line, not one machine is capable of handling the entire process. There are various machines used for various purposes. Roughly, a basic SMT line requires a printer, a mounter and a reflow oven to give an assembly output. To reduce the final cost, certain measurements can be done on the manufacturing line itself.
R.S. Gupta, senior manager-Sales & Marketing, DVS India, informs that manufacturers have started using high-quality, repeatable printers capable of 2.5D and 3D inspection of the paste printing itself, so no separate testing is required at this stage. The printer introduces almost 60-65 per cent of the problems of the process in line. So by taking care of the first stage, your product doesn’t show up the kinds of problems that are incorporated at the first stage. Problems detected at an earlier stage can be corrected at a very low cost. This reduces the final product cost.
Once the product comes out of assembly, the manufacturer does various kinds of testing to check whether the product is manufactured as per the requirements or not. Testing is done for manufacturing defects and functionality.
During the product assembly, some problems may get incorporated due to human or machine mistake, or due to a faulty part put on the assembly from the supplier’s side. Out of a thousand components, one or two parts may be failing. As component manufacturers today are taking a lot of care, this is very rare. So it may not be failure from the supplier’s side but there are devices which are very electrostatic discharge (ESD) sensitive and may fail when handled with bare hands. Also, the process itself may fail due to over-heating, etc.
The basic requirement of testing an assembly is to detect whether the product is free from manufacturing defects or not. It is the cheapest testing carried out in an assembly. It detects whether the component used is correct or placed correctly. Apart from these component problems, there could be soldering-side problems as well. When solder is used in excess it could create a bridge between two nearby pins, while less solder creates a dry point. Manufacturing defect testers detect the analogue component type and its value, but can’t test digital components. These aren’t very costly either. One can use manufacturing defect analysers (MDAs), flying probe testers (FPTs), automated optical inspection (AOI) systems or automated X-ray inspection testers depending on the equipment’s return on investment. Of these, manufacturing defect analysers are the cheapest.
In the same kind of environment, one can even use a high-end tester called in-circuit tester (ICT). An ICT is a full-capacity tester capable of testing analogue, digital and mixed-signal devices. It costs ten times more than an MDA. The rate of fault detection is very high using an ICT. So a manufacturer using an ICT charges more for its products. Besides doing what an MDA does, the ICT performs power-on testing as well. That is, when you apply the power, it checks individual components on the assembly for their functionality (whether they are performing as per their specifications or not). It, however, can’t test the full product for its functionality.
ICTs are very generic. These are user-programmable. You can use an ICT to test different components by using a dedicated fixture and program written for the PCB. The fixture ensures electrical connection between the assembly and the tester. These fixtures and programs are very dedicated. That means if you have a product with ten components, you need ten fixtures and ten programs for component testing. Of course, even a manufacturing defect analyser requires a dedicated fixture and program but these two cost very less. For ICT the cost is higher due to full power-on testing.