From in-vehicle communication to fuel efficiency and regulatory norms, every automotive innovation is becoming more complex and highly integrated. It implies that test and applications engineers must be innovative and resourceful in approaching every test for better design, shorter time-to-market and lower cost
SHWETA DHADIWAL BAID
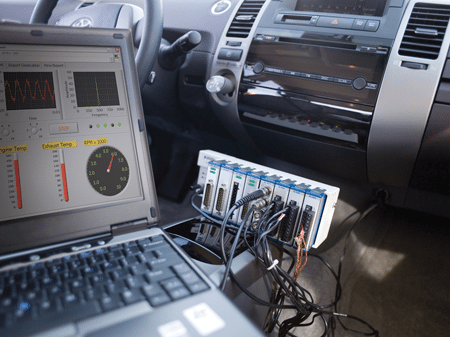
When you build a system that integrates many small systems, the biggest challenge is effective communication between all the smaller systems to make the big integrated system work as one. Today’s automobiles consist of various interconnect buses to communicate between sub-systems. To test these systems, you need tools and solutions that support serial communication standards.
An evident change which the automotive industry has gone through over the years is the use of electronics in automobiles. “If you see a new-generation car, the use of electronics is conspicuous right from the security and vehicle access system to the driver interface, powertrain, safety and enticing infotainment and telematics,” says Asish Jain, applications engineer, Agilent Technologies.
Test and measurement tools have been used for many years now in the design and testing of engine control systems, entertainment systems and safety systems. “What is now emerging as a critical area is energy conservation and power management,” adds Evan Sun, technical marketing manager, Tektronix. Agreeing to this Prabhakaran P.V., business unit head-MDTS from TTL Technologies, shares, “With the increasing commercial and regulatory pressure for safer and environment-friendly vehicles, most of the automotive OEMs are looking for more efficient and green designs to position themselves on top.”
Rajesh Pathak, advanced specialist-technology, Delphi, explains, “An automotive controller has to undergo many tests in sub-systems as well as integrated environment. Some of the tests include vibration analysis, crash testing, accelerated tests, temperature test, EMI/EMC test, safety standard requirement, emission test and structural tests. Apart from these, there are non-electronics related tests like oil test, salt test, water test, soak test, sand test and drop test.”
“The test and measuring solutions have to be versatile, adaptable and exhibit excellent forward/reverse compatibility to cater to an extremely varied nature of testing requirements of the automotive industry without affecting the integrity of the test methods,” says Tapesh Gautam, assistant manager, product support & application, Rohde & Schwarz.
Commercial off-the-shelf equipment
Automobiles, though specialised applications, are basically an integration of many sub-systems. To test these systems, there are several commercial off-the-shelf (COTS) bench equipment available that fit the general requirements. However, “the difference may lie in the frequency ranges of the applications and implementation,” says Jain. Illustrating with an example, he says, “The radars used in aerospace and defence typically operate below 40 GHz and involve complex design and stringent tests. However, radars used in automobiles for collision prevention work in the 76-77GHz band with a relatively simpler set-up. The testing solutions vary to match these specifications.”
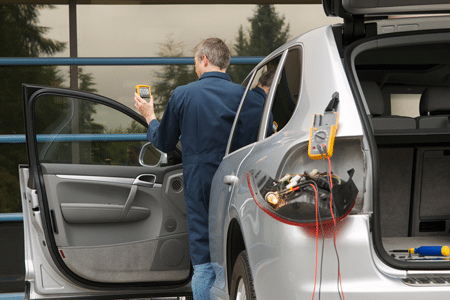
Digital and mixed-signal oscilloscopes, specialty probes, expert power measurement software, logic analysers, signal generators and real-time spectrum analysers are among the general-purpose equipment used in automotive design as well as production. “Switch-mode power supplies, electronic loads and data loggers are used in design and verification and life-cycle testing of any automotive component or system,” shares Prabhakaran.
“Equipment can be standalone box tester units with predefined test functionality or modular with I/O cards added based on the sub-system being tested,” says Rohit Panikkar, technical marketing manager, National Instruments. During R&D, dynamometers are used to study the effect of various conditions on engine, brake and chassis. Test systems to study the endurance of system components and noise, vibration and harshness (NVH), as well as safety test systems are also used at this stage. An RF signal generator and RF analyser with spectrum analysis capability are used to test remote keyless-entry modules.
Automotive vehicle power systems are very harsh electrical environments. “High-current motors, solenoids and other components on the power system often cause power system voltage transients and dropouts to occur. Successful operation of automotive electronics depends on adequate power transient immunity. These transients can be studied using a scope. However, a DC power analyser reduces the test time and improves ECU test coverage by allowing engineers to easily capture and re-play power system transients. Libraries of transient cases can be developed and archived for future use as well as for long-term support and ECU re-qualification,” explains Jain.
Data acquisition systems and highly accurate digital multimeters (DMMs) are also required in almost all the stages of design and development cycles. “There are specially designed loads and power supplies used for testing of fuel cells, batteries and charging of electrical vehicles,” adds Prabhakaran.