A satellite has to operate in very harsh conditions after launch. Also, building a good satellite requires billions of dollars. Therefore it’s crucial to test each satellite properly before it enters space to ensure good performance and safety. This article covers the various types of satellites testing and challenges that may occur during the process.
Satellites, one of the long-existing inventions, are exhibiting their muscular and exuberant strength in the right way. For years, satellites have been providing services like navigation, communication, remote sensing, surveillance, earth observations, etc. Since satellites face lots of hazards in space during their operation, efficient technological standards are required to design them.
Today, most of the people depend on satellites in one way or the other, from GPS-based vehicles to weather forecasting to many other things in their lives. Currently, there are almost 1,500 active satellites in orbit around Earth.
Building a good satellite is not cheap. Government or private companies spend millions or even billions of dollars a year on satellites, and it would result in a heavy loss if a satellite fails during or following launch. So, tests and measurements play an important role in the case of satellites.
Tests and measurements are required for components of satellites manufactured for sub-systems and final assembly. Evaluating the performance of satellites is essential even on the ground station terminal. Such smart test and measurement solutions ensure good performance and reliable safety and security on every stage during a satellite launch.
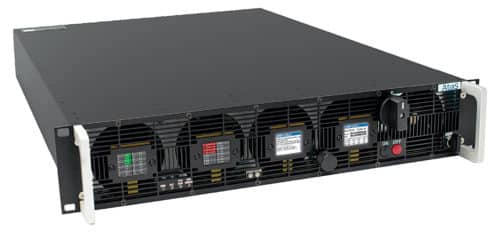
Inside the world of satellite testing
Extreme vibrations and high acoustic levels exist during satellite launch. Further, a satellite has to operate in very harsh conditions after launch. It has to function in a vacuum while handling high levels of electromagnetic radiation and fluctuation in temperatures.
Companies like NTS maintain a network of facilities across the US to conduct necessary tests to analyse how a satellite responds to a vacuum of space or extreme changes in temperature.
More tests are required for vibration, solar radiation, dealing with the dust of space, or pyroshock, which might occur during the booster separation stage or satellite separation stage from exploding bolts. Sometimes explosive shock might also occur during the booster separation stage. This can even damage circuits, lodge contaminants into satellites, or short circuit electrical components.
Other elements of a satellite that need testing during its construction, design, and payload include:
- Solar panels
- Antennas
- Batteries
- Electrical circuits
- Centre of gravity and mass measurements
- Information transmitting systems from satellite to the ground station
- Fuel cells
Currently, NASA and other private companies are trying to build smaller vehicles that would be capable of repairing satellites. NASA is also working on ideas that would help assemble satellites in space itself.
The satellite’s assembly team is the first group to test it. Next, a quality control team conducts a separate series of tests. The team often repeats many of these tests to gather enough data to decide whether or not the satellite is fit to go into orbit.
Testing has to be carried out in a clean room. Scientists and engineers involved in testing can be usually seen wearing a white suit. A clean room or environment is an integral part of satellite testing because one tiny outside contaminant can produce a drastic effect on a satellite.
The United Launch Alliance Atlas V rocket stands ready for liftoff with NOAA’s GOES-S satellite on Space Launch Complex 41 at Cape Canaveral Air Force Station in Florida (Credit: NASA)The two major satellite tests are as follows:
Antenna deployment test
The uplink/downlink commands and telemetry data are established once the satellite antenna is perfectly deployed in space. So, for establishing reliable communication between the ground control station and satellite, this test is essential.
Subsystem testing
It involves activities such as battery voltage and bus voltage testing, primary and secondary battery voltage testing, solar panel voltage testing, actuator and sensor testing, momentum wheel testing, magnetic voltage testing, sun sensor testing, etc.
Testing story of GOES-S
National Ocean and Atmospheric Administration tested its Geostationary Operational Environmental Satellite-S (GOES-S), a weather satellite, in March 2017. As a part of testing, the team had placed GOES-S in a thermal vacuum chamber to determine its ability to operate in the extreme cold conditions of space.
The vacuum chamber tested the satellite across four different cycles that ranged from intense cold to intense heat. Severe temperature fluctuations in the airless chamber gave scientists a chance to check how well the satellite’s sensitive instruments perform in these harsh conditions. Scientists had also tested GOES-S thrusters, which helped orient its orbit after its launch vehicle released it.
During testing, a satellite’s exact centre of gravity and mass are also measured. This ensures that the satellite is compatible with its launch vehicle. It also helps control the orientation when the satellite is in orbit. This even helps to know how long it will operate in space.
Has the time come for fully automated testing of satellites?
Let’s take the example of Electrical Ground Support Equipment (EGSE) satellite testing solution developed by Atos, a French-based MNC. It makes sure that satellites are ready to launch and work perfectly. The Radio Check-Out Equipment (RF SCOE) is the industry-standard solution to test radio frequency subsystems of a satellite with the highest degree of precision. The payload EGSE is highly flexible as it tests the instruments of navigation, earth observation, and telecom satellites. Finally, the power SCOE ensures that the satellite’s vital power supply works reliably under all space conditions.
The RF SCOE performs fully automated S, X, Ku, and Ka-band measurements in the Telemetry, Tracking and Command (TT&C) section of the satellite during assembly of spacecraft and space environment testing at the test centre facility. It does the same in the L, S, Ku, Ka, and UHF bands for the mission communication and payload section.
The payload EGSE allows the fully automated execution of calibrations and tests, and it easily integrates with heterogeneous components from different providers and suppliers. Further, all test sequences and procedures are defined in the open source language TCL and can therefore be easily tailored and extended to the best-fit requirements of the satellite owner.
Key parameters seem to be on the rise
Thousands of satellites will be launched over the next decade to provide global Internet coverage, mobile telecommunications, earth observation analytics, and space-based Internet of Things (IoT) for real-time monitoring of assets. Testing the characters of microwave performance of antennas of such satellites is a major part of testing. Measuring group delays with unknown or unstable local oscillators and TVAC drifts are also an important part of satellite testing.
Modern computer-controlled test equipment also plays a crucial role in modern satellite testing. Detailed knowledge of antennas, microwave, RF, IF, and baseband engineering is essentially required for satellite test engineers. Further, testing techniques of many laboratories are significantly modified by taking into account factors such as rapid spacecraft temperature changes, doppler shift, propagation fluctuations, and signal propagation delay.
Small satellites stay at low earth or medium earth orbit and have life expectancies from several weeks to four years or more. The testing of such satellites helps both financially and physically. Space simulation testing is another part of satellite testing. In this, advanced chambers are used to imitate space temperature, pressure, and humidity.
A single satellite can have dozens to hundreds of spot beams. For example, the Inmarsat GEO I-4 satellite has 200 narrow spot beams. Spot beams allow satellites to transmit different data signals using the same frequency. Spot beams greatly increase the complexity of design, test, and calibration of antennas. Smaller spot beams increase antenna size. For addressing the wideband needs of satellite testing, PXA and UXA signal analysers and oscilloscopes can be used.
During testing, the satellite’s electromagnetic emission capability needs to be measured. A planar near-field scanner is also required for measuring the performance of antennas used for communication.
Challenges in establishing satellite test centres among different nations for space reforms
ESTEC Test Center in Noordwijk, the Netherlands, is the largest satellite test centre in Europe. STFC RAL Space has been awarded £99 million from the UK government’s industrial strategy challenge fund to develop National Satellite Test Facility (NSTF).
ESTEC Test Center in Noordwijk, the Netherlands, is the largest satellite test centre in Europe (Credit: www.esa.int)At NASA’s Goddard Space Flight Centre, a 3.1m×4.9m robot is busy testing satellites on Earth before it is put to use in space. A six-legged hexapod robot was built by Mikrolar, a New Hampshire-based company.
University of Illinois’ premiere space design and testing workspace laboratory supports students, faculty, and other customers to utilise small satellite resources to design, develop, and test satellites. The laboratory is equipped with a clean room, thermal vacuum chamber, vacuum oven, sun simulator, earth orbital magnetic simulator, and range of mechanical and electrical diagnostic equipment. Multiple forms of rapid prototyping design and simulation facilities are also provided.
Satellite Integration and Testing Establishment (SITE) of ISRO was established in 2006. It can integrate and test six satellites of INSAT class at different stages simultaneously. The facility has also carried out vibration and acoustic tests of Mars Orbiter Mission (MOM) spacecraft.
Moving forward
Technological evolution is immensely supporting the satellite testing sector equally. Emerging technologies such as robotics, artificial intelligence, etc, are becoming the fastest drivers of growth and improvements in satellite testing. Opportunities are emerging in the design, manufacturing, and testing of satellites. India has completed a successful decade in satellite testing, and in the coming years, more growth and advancements can be seen in the country’s space world.
Vinayak Ramachandra Adkoli is BE in industrial production. He has been a lecturer in mechanical department for ten years in three different polytechnics. He is also a freelance writer and cartoonist.