“3D printing is now moving towards becoming mainstream,” notes Vishesh Shishodia, co-founder, www.3dprintronics.com. Earlier, 3D printing was restricted to big industries or research labs that used industrial 3D printers for rapid prototyping. With the proliferation of desktop fused deposition modelling (FDM) based 3D printers, this technology has now come to the masses. He says, “The massive do-it-yourself (DIY) movement in the USA and Europe in the field of open source 3D printers has a huge contribution in making this technology affordable and available to common people. Project RepRap is one such movement.” He adds, “Most of the present desktop 3D printers are based on ideas taken from such open source printers.”
Latest developments in this field can be classified into two domains: desktop 3D printers and industrial 3D printers. Let us take a look at both simultaneously.
Exciting progress in desktop 3D printers
Last year was a very exciting one for 3D printing, believes Prasad Rodagi, founder-director, Altem Technologies, due to the emergence of low-cost 3D printers in Indian market, including some of those made indigenously. He says, “Though these might not have massive implications on an industrial level, these printers made 3D printing more accessible to a lot of people and generated significant interest in the common man due to the cost factor. These work great for DIY projects and allow for more design prototyping.” He adds, “While you might be able to 3D-print quirky little coffee mugs and mouse pads on hobby printers, it creates awareness about what these printers can do. It opens up one’s imagination to other possibilities, which is one of the wonderful things about low-cost printers.”
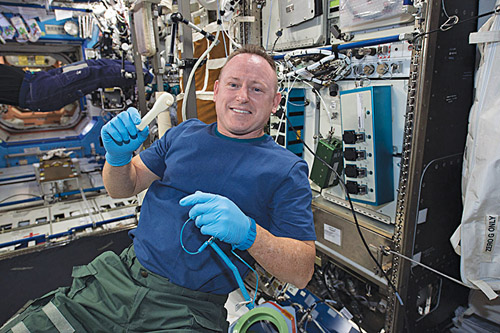
Another noteworthy development has happened in adopting entry-level 3D printers offering stereo-lithography (SLA) based technology to make very-high-definition and complex industry applications, like electronics, manufacturing, automobile, dental and medical devices, informs Chandan Mishra, co-founder-director, 3Digiprints. SLA is a highly-accurate, additive manufacturing process used to create parts from 3D CAD data in a matter of hours. In this process, CAD data is sliced into very thin cross-section or layers, and this data is then transferred to an SLA additive manufacturing 3D printer, where it creates the model one layer at a time. Models created with this technology are typically used as concept models. Desktop SLA based printers have begun to make a mark, with Formlabs (a designer and manufacturer of desktop 3D printers) leading the pack.
A lot of companies have also started manufacturing their own desktop 3D printers. Talking about the launch of Stratasys’ new printer in July, 2014, Rodagi says, “The Connex3 colour multi-material 3D printer series features a unique triple-jetting technology that combines droplets of three base materials to produce parts with virtually unlimited combinations of rigid, flexible and transparent colour materials, as well as colour digital materials, all in a single print run.”
Progress in industrial 3D printing technology
Significant development has happened in the last couple of years in the industrial 3D printing sector. Industrial 3D printers that use materials like titanium and other highly-refined materials can print new and replacement parts for aerospace, automobile and medical device industries. Mishra says, “A more refined workflow system is helping many companies to use 3D-printing processes to offer distributed-parts delivery systems, enabling them to cut cost in terms of inventory and product upgradation.” On personal printers front, he adds, “Many companies have now started offering products on reliable FDM platforms with low-cost printers (starting US$499) and making these affordable for professional as well as home use.”
Coming years will see 3D-printing materials get more suitable and compatible with injection-moulded parts, feels Mishra. Consequently, the cost of these 3D-printed parts would fall down. He says, “It will also see a huge technological upgradation in terms of productivity and printed sizes to allow companies to use 3D-printed objects in their final production process.”