Pearce, who is well-versed in 3D printing and solar technologies, is known for developing open source, low-cost 3D printers. Recently, he added two more solutions, both open source and solar-powered, to his useful repertoire.
The first scheme comprises an array of solar photovoltaic panels and a stand-alone printer. It is quite cost-efficient and can make very good models, but is more appropriate for schools and businesses as it is not very portable. It can be stationed at a sunny yard and used effectively.
The second solar-powered solution is more portable. It uses a RepRap printer, which is small enough to fit in a suitcase but has a lesser capacity than the previous option. It can be taken by social workers to backward communities to make essential stuff needed by them. Since it is a RepRap, it can even be used to make another RepRap or print parts to make a larger 3D printer.
Quasi-crystals make a strong entry
As more and more industries, ranging from aerospace to healthcare, resort to 3D printing to manufacture equipment, it becomes important to have lighter materials with stronger functional properties. Researchers at University of Lorraine in France say that new composite materials developed with the help of quasi-crystals, a type of complex metal alloy (CMA) with crystal-like properties, can meet that demand.
CMAs have very desirable properties like low friction, corrosion-resistance and durability. However, being brittle, it is difficult to use them as the main bulk material. The team at Lorraine suggests that instead these can be used as reinforcement particles or coating material. Hand-in-hand with metals, CMAs can be used to 3D-print light-weight parts with mechanical properties similar to heavier steel-brass counterparts used in the industry.
Likewise, quasi-crystals can also be used to reinforce polymer matrix composites used in 3D printing.
Such materials, which offer great strength at a lower density, would be very useful in industries like automotive, aerospace and healthcare. In fact, functional parts using such alloys are already commercially used in pipes and intake manifolds used around car engines. The team is now working on developing functional parts for certain healthcare applications.
Quantum-dot LEDs light up 3D printing
In the previous example, we saw how combining metals and metal alloys for 3D printing resulted in great advantages. There are several such attempts being made across the world to improve the versatility of 3D printing by seamlessly integrating diverse materials into the process. One such attempt, by a team at Princeton University led by Prof. Michael McAlpine, is very promising.
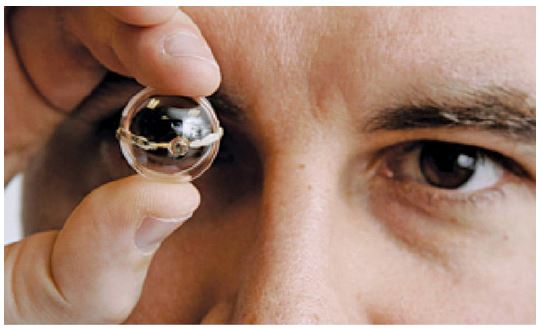
By seamlessly interweaving five materials, they have 3D-printed a 2×2×2 cube of encapsulated light emitting diodes (LEDs). All components of the cube, including the electronics and connectors, were 3D-printed using a custom-made 3D printer.
The bottom layer of each quantum-dot LED has silver nano-particles. The next two are polymer layers that push electrical current up to the top layer. On the top, a simple gallium-indium layer is used to direct electrons away from the LED. The printer starts building the LED cube, one layer after the other, from the bottom up. The significant thing to note is that each layer is of a different material, a feat which today’s commercial printers are incapable of.
The McAlpine research group at Princeton is focused on 3D printing bionic nano-materials. They convey on their website, and in research papers, that by interweaving biology and nano-materials, one could create bionic devices with unique dimensions, properties and functionalities. In the beginning, this could help in research, but over time it could enable healing and rehabilitation too.
The group also hopes to make some headway into printing transistors.
When homes become factories…
3D-printing gurus, leading companies and DIYers are able to build an unimaginably-large array of 3D-printed things, from prosthetics and living tissues, to food, arms and ammunition. Basically, man is becoming a creator. Unfortunately, whenever technological power spirals, regard for nature nosedives. The power of creation vested in the hands of common men can lead to a slow, steady but significant abuse of nature. Take transportation as a simple example. As long as people were using the few, but controlled, public transport options, pollution was within control. When individuals started using their own vehicles, the problem got out of control. The case with 3D printing could be similar.
In an Op-Ed in LiveScience, an academician recalls seeing a pile of 3D-printed plastic parts outside a lab—several iterations of a print job rejected by a student before hitting bull’s eye. That, in simple terms, is a bane of 3D printing. Plastic is never good news, and the hard truth is that, although biodegradable 3D-printing materials are available, most people would still be using plastic for a long time to come.
3D printers also guzzle a lot of energy. Bingo, another environmental threat. Basically, 3D-printing will bring environmental problems associated with large manufacturing houses to people’s homes, albeit on a less dangerous scale. However, more instances of a small problem can be as hazardous in the long run.
Will somebody please find a way to avert the upcoming trouble or compensate for it by 3D printing dense woods of living, growing trees full of the juiciest fruits and the most fragrant blossoms, where animals roam free and wild, and the trumpet of the majestic elephant rises up to the skies?