Human workers, who once saw industrial robots as a threat to their jobs, are now quite happy to share the space with the current generation of cobots, as these are proving to be truly cooperative, collaborative, and congenial co-workers.
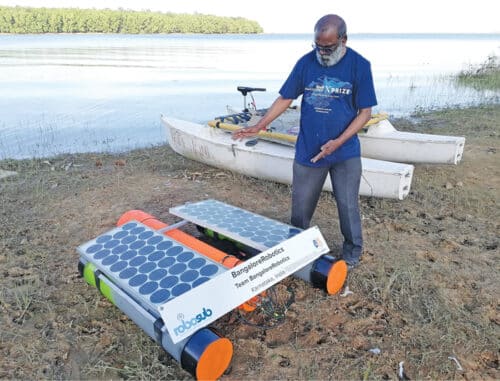
Some years ago, a hammer fell into a high-pressure steam pipe at Tata Power’s plant in Mundra, Gujarat, stalling the plant’s operations. It was a pretty complex situation, as the 90-degree bend of the pipe made it almost impossible to see where the hammer was stuck. Interestingly, the plant sought the help of Gridbots Technologies, an Ahmedabad based robotics startup. The Gridbots team made some modifications to the gripper of their Stinger pipeline robot and managed to get the hammer out in a five-hour operation, at a cost of ₹1,600,000. Compare that with all other alternatives, which would have taken several days and cost the company tens of billions of rupees in expenses and losses, and you will understand why a lot of robotics enthusiasts remember and recall this story even after so many years.
That indeed is what robots are meant to do. In the robotics world, this is known as the 4D principle—let robots do tasks that are dull, dirty, dangerous, or dear. That is, work that is repetitive, unhygienic, risky, or costly (where one cannot afford to err). For this purpose, robots have been used in heavy industries like automotive, and dangerous conditions like mines, for a long time now.
However, the robots of yore were generally expensive, huge, heavy, and often dangerous. They had to be confined to work-cells, away from human workers. Most robots were also difficult to program, and hence used for specific, unchanging tasks. This put them out of the reach of small and medium sized industries characterised by high-mix, low-volume jobs. On top of everything else, human workers often looked at these intimidating robots as the bad guys who had come to steal their lunch!
Potential applications |
• Material handling
• Machine tending • Palletising • Dispensing • Warehouse automation • Kitchen automation • Greenhouse automation • Automated kiosks • Agricultural processes • Cleaning and sanitisation • Lab automation • Healthcare assistance |
Enter cobots
Cobots, or collaborative robots, are robots that work alongside humans. They are generally lightweight, affordable, and easy to program. Most of them are just arms and wheels and look nothing like the Jetsons’ maid Rosey—but they are quite endearing in their own way, and human workers welcome their assistance.
In the mid-90s, General Motors (GM) faced a challenge from the Occupational Safety and Health Administration to find ways to improve ergonomics in factories. Ergonomics was a pressing issue for most heavy manufacturing industries, as these problems ended up as injuries in the long run, hitting both workers’ health and productivity.
Prasad Akella, who led the effort to develop cobots at GM, explained the problem in a media interview of that time: “If you tried doing something as simple as picking up and installing a 40-pound car battery, one a minute for eight hours a day, 200 days a year, your back is going to start feeling very sore.” So, GM started working with researchers at Northwestern University and the University of California, Berkeley, to develop safe robots that could work with people, helping them with lifting heavy objects and other unergonomic tasks.
Michael Peshkin and J. Edward Colgate at Northwestern University ended up developing collaborative robots, and the team at University of California, Berkley developed extenders or human power amplifiers. Colgate and Peshkin first called their people-friendly robots as programmable constraint machines (what an unfriendly name!) and later adopted the term ‘cobot,’ which was suggested by Brent Gillespie in a lab competition to come up with a better name.
It is clear from the story of its birth, that cobots were never intended to replace humans. They were only intended to work with humans to improve their efficiency and effectiveness by extending their strength and precision and augmenting their intelligence with data.
“The idea is to have a world where people work with robots, not work like robots. Unlike industrial robots that require safety fences, cobots are capable of working alongside human workers without the need for the installation of safety cages (upon risk assessment). Cobots can take on dull, dirty, and dangerous tasks, relieving human workers to focus on higher-value tasks. They can, for example, take on repetitive tasks like packing and palletising, or delicate and risky jobs such as handling grippers, spot welding, screwing, and other difficult activities like lifting heavy parts,” says Sougandh K.M., Country Manager – India, Universal Robots (UR).
Workers who do the same task requiring a similar physical movement constantly often suffer from what is known as repetitive strain injury (RSI). Cobots are ideal for such jobs. Advanced vision systems and precision tools enable cobots to do high-precision jobs that can be very stressful and time-consuming for humans.
Venkatesh Gurappa, Founder Director, Bangalore Robotics Pvt Ltd, India and Bangalore Robotics Science and Research gUG, Grünwald, Germany, and President, BlrAUV Inc, USA, explains further that cobots are small, cheaper than traditional robots, efficient, intelligent and fast. “They will be very helpful in industrial production units, where they can assist the technicians very efficiently and reliably. They can see and reach difficult areas easily. A cobot’s mechanical arm can have more movable joints than the human hand, and so can reach inside the depths for a screw or bolt hidden behind many parts. Besides, the cobot can be trained to do any particular sequence of tasks. It can learn and mimic the actions of the human master,” he says.
Guruprasad S., Associate Vice President, ABB India Limited, adds, “Cobots are designed for low payload applications such as handling small parts and inspection tasks. But there is so much more: AI integration and use of software can transform any connected industrial robot with higher payloads and faster speeds into a collaborative one. From testing samples in labs to making computer chips, collaborative robots (cobots) are working together with humans to transform our lives. Cobots are taking on repetitive and mundane tasks and helping create the flexibility and scalability for small and medium-sized enterprises to grow.”
What makes cobots special
A cobot is a robot that meets certain requirements. First, of course, is its ability to work along with humans without caging—and this is no easy feat as humans are known for their unpredictability. And then, there is everything else that makes it a worker’s friend and not a threat.
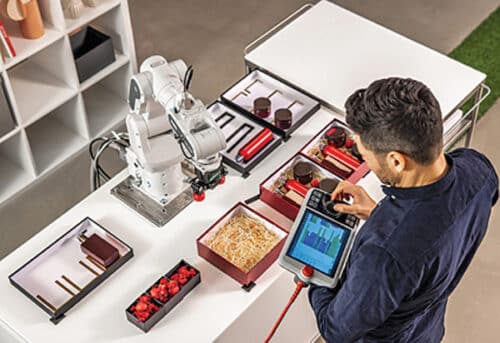
Katherine Scott, Developer Advocate, Open Robotics, explains, “First and foremost, cobots need to be safe to operate alongside their human colleagues. The primary implication of this is that often cobots aren’t as fast or as strong as industrial robots to avoid potentially dangerous situations. Cobots usually have more sophisticated control systems that allow them to interact with humans safely: A good cobot will stop or slow down if it bumps into another object. Since cobots can work alongside people, they are capable of degrees of autonomy that weren’t available to industrial robots. An autonomous mobile robot, for example, can be tasked with moving an item from point A to point B, but it makes its own decision on the best way to make that delivery. Lastly, cobots are armed with a degree of sensing and data collection that were not available to industrial robots. Cobots can collect data from a warehouse floor, for example, and have that data fed into a larger automation strategy. Industrial robots were stand-alone devices, without a larger view of the automation strategy.”
Open Robotics is the primary maintainer of the Robot Operating System (ROS). ROS gained popularity after its utilisation by many of the robots at the Defense Advanced Research Projects Agency (DARPA) Robotics Challenge, which began in 2012. NASA used it on its Robonaut 2 humanoid robot and Astrobee systems, which are deployed on the International Space Station (ISS), and in the VIPER, a mobile robot that NASA aims to send to the South Pole of the Moon in 2024.
Safe to work with humans
ISO/TS 15066:2016 specifies safety requirements for collaborative industrial robot systems and the work environment, and supplements the requirements and guidance on collaborative industrial robot operation given in ISO 10218-1 and ISO 10218-2.
Suraj K.K., Senior Sales Engineer, Systemantics India Pvt Ltd, an Indian company that has designed and developed collaborative robotic arms indigenously from the ground up, explains that one or more of the following requirements must be met to ensure that humans are not exposed to unacceptable risks.
One, the robot stops when humans enter the collaborative space. Two, its motion is controlled by a human hand. Three, the robot maintains a specific distance and speed. Or four, its inherent design and controls limit impact at contact events. “Our products comply with the second and fourth point, partially complying with the third,” he says.
Different applications require different levels of collaboration—and different levels of collaboration require different levels of safety.
Guruprasad of ABB explains further, “There are three types of collaboration: coexistence, intermittent collaboration, and cooperative or close collaboration. Coexistence means safe and shared use of the same workspace between the cobots and humans without protective fences, for example, palletising. Synchronised collaboration means planned but more intermittent interaction between the cobots and humans, such as in machine tending. Cooperation is the highest level of collaboration where workspace and tasks are shared continuously, for example, on small parts of an assembly line. Cobots enable human interventions multiple times during the robot operational cycle, for example, where a part of the assembly of a component is done by the cobot and another part by a human. The safety functions of ABB cobots are according to ISO10218-1 and ISO/TS 15066. In order to account for the unpredictability of human behaviour and movements, ABB’s collaborative robots are enabled with safety functions such as power and force limiting, speed and separation monitoring, hand guiding and safety-rated stop.”
“Cobots go through various safety and security measures before they are deemed safe to be used in factories. Each machine passes through various tests and safety standards. Cobots come with robotic vision such as sensors and laser cameras. Robotics arms are integrated with laser cameras and sensors to sense their surroundings and work accordingly. Technology has advanced in the last few decades, and artificial intelligence (AI) has developed to a great extent that if a human comes in contact with a machine working area, the machine stops automatically and saves humans from any potential injury,” says Sougandh.
Balancing safety and functionality
Suraj remarks that a user’s perspective of an ideal cobot will depend on where the emphasis lies—safety, functionality, or both. The safety features explained above have to be balanced with functional requirements like ease-of-use (which also translates to flexibility), support and service, weight of the robot, and accuracy and repeatability (depending on the area of application).
Compact and lightweight
In addition to the smaller footprint, lower weight, ease-of-use, and safety make cobots more versatile than regular industrial robots. They can be deployed even in places with space constraints, comfortably placed near workers, to assist them without eating into their workspace. “A collaborative robotic arm can be mounted on a pedestal to service a cell, a floor gantry to service a line, or a vehicle to service an area,” says Suraj. Cobots can be easily moved around and set up for multiple applications within the same plant. Generally, they require minimal or no infrastructural modifications to the work floor.
Adaptable to multiple tasks
Sougandh of UR says, “Traditional robots need engineers to operate them, and their functions are predetermined. Cobots are adaptable and capable of carrying out many activities. Each machine is built to carry out a range of functions and is simple to program. Even operators with limited or no robotics or programming background can operate a cobot; in fact, certain end effectors allow you to swap between tools several times a day.”
Today, cobots can be easily programmed to perform one or more tasks using user-friendly software, mobile apps, and even through physical movement or “lead-through programming” as ABB calls it. You can just hold the robotic arm and move it physically to ‘train’ it to do something—just like you would teach a kid yoga! It can also be reprogrammed as easily as that—so the same cobot can do multiple tasks as and when required.
There are various tools available—grippers such as finger-grippers for pick-and-place operations, end-of-arm tooling like glue dispensers, automatic tool changers, range extenders, supply systems, vision and software tools—which can be used to adapt the cobot for doing multiple chores.
“The best part about a cobot is that it can learn from the master and do the taught task even better than the master,” quips Gurappa.
Technologies for better collaboration
Apart from mechanical and material improvements, advancements in technologies like AI, machine learning (ML), sensors, data analytics, and open source software are having a significant impact on the emerging generation of cobots. The experts we interviewed spoke of some of the significant technologies influencing cobots today.
AI and ML. “Advancements in ML are fuelling the growing deployment of cobots. Applications being rolled out allow cobots to mimic human behaviour—much as any human trainee would. This saves the time that previously would have been required for programming,” says Sougandh.
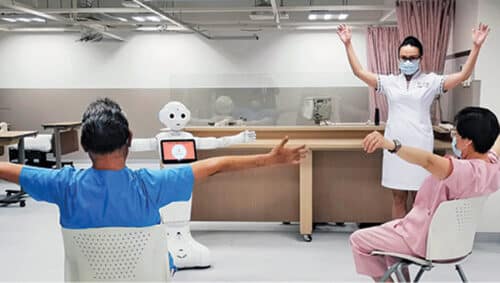
Guruprasad adds, “Technologies like big data and AI are at play to develop bots such that one day they may be able to perform unrestricted movements they’ve figured out on their own. Apart from that, industrial cobots, sometimes, must work in harsh conditions that affect their data connection, so durability is quite necessary on that front. Heavy duty conductors (HDCs) are designed for this, and we’re working on further innovations, since reliable connectivity is quite necessary. With their always-on connection to big data and AI, collaborative robots may eventually be able to perform unrestricted movements they’ve figured out on their own. This breakthrough will further boost their viability in less-structured manufacturing environments.”
Cameras and sensors
Advanced sensors and cameras are essential to enable precision, learning, performance, and safety. Scott says regarding the cameras, “The rise of robust, affordable, smart cameras has been critical. The past few years have seen a number of camera systems come to market that feature depth sensors and integrated deep learning co-processors. These cameras make building a cobot cost-effective and improve its overall reliability.”
Singrow, a Singaporean agri-tech company that harnesses technologies like vertical farming and robotics to produce healthy fruits and vegetables without pesticides, partnered with Universal Robots and Augmentus, a leader in easy-to-use and rapid AI-robotics software, to automate pollination and harvesting in their strawberry farm. “The company deployed a UR cobot adapted with a camera that would identify flowers using Augmentus’ integrated AI technology for effective pollination and the picking of ripe strawberries,” recalls Sougandh.
Open source software
“Open source software is one of the most important developments in the rise of collaborative robots. When the robotics industry was largely focused on industrial robots, each robot had its own software and hardware. Due to the proprietary nature of this software, there was little or no collaboration among industrial robots, and for decades not much innovation. In the same way that open-source initiatives like Linux, Apache and others gave rise to the Web, software initiatives such as the Robot Operating System have given rise to collaborative robots and more advanced robotics applications,” says Scott.
ROS 2 is the second generation of ROS, and it has been built from the ground up to work in industrial settings. As ROS 2 becomes more prevalent, more and more vendors have begun to support it, thus simplifying system integration. micro-ROS is a variant of ROS built for embedded microcontrollers, which make it even easier to build robot components that support ROS out of the box.
Is there a place for hobbyists here? |
Many innovations at the grassroots level come from hobbyists. And there are quite a few very enthusiastic hobbyists in the robotics space too. So, what is the feasibility of them developing innovative cobots? Here is what Venkatesh Gurappa, mentor to many a roboticist, has to say: “It is difficult for a hobbyist to develop a cobot, due to constraints like unavailability of components and absence of sufficient open-source alternatives. “Most of the usable precision components are proprietary and expensive, if at all it is possible to import them, considering the many import-export restrictions on such components. The critical aspect of safety depends on the precision and quality of the moving components and the accuracy of the sensors. The costs are relatively high due to this. The idea may be more feasible if the individual components are indigenously-developed and manufactured in India, and has a greater potential too. “If hobbyists do manage to build one, getting it to the market is not a problem since the industry itself is looking out for such systems.” |
Miniaturisation
People want more compact designs that are even stronger—and collaborative robots are no exception to that. Guruprasad says, “Miniaturisation of cobots also opens unique opportunities for electro-mechanical helpers that can exist outside huge production facilities. Institutions and businesses could benefit from miniaturised cobots with the intelligence to complete day-to-day mundane tasks.”
“Technologies that would contribute to higher levels of collaboration would be a combination of lighter materials (like carbon fibre composites) for larger cobots, sensing (real-time vision, very sensitive haptic feedback etc) for avoiding unintended contact or providing intentional engagement with humans, and intelligence (reinforcement learning etc) to learn the context of operation to minimise human attention and interventions,” sums up Jagannath Raju, Chief Technology Officer, Systemantics India Pvt Ltd.
See, what I can do for you!
“The introduction of cobots has opened up automation possibilities in almost all industries—manufacturing and service. For example, we have had discussions with companies building automated kiosks and floor cleaning robots. We are also discussing with companies providing automation solutions with cobots for warehouse solutions, greenhouse automation, construction field, and so on,” says Suraj.
Industries like food, plastics, electronics, pharmaceuticals, metal and automotive have been using cobots for several tasks like pick-and-place, palletisation, and warehousing. Now, cobots are seen in more people-facing roles like cleaning, healthcare, and food service. Let us take a look at some of these new applications, which are emerging on top of the already established industrial uses.
Cleaning the nooks and corners
Yes, the little bots that clean floors are also cobots, because they move around with people and pets in the house. That said, cobots are also being used for cleaning on a more industrial and commercial level. Cobots integrated with floor-cleaning mobile robots help to access the nooks and corners. Many airports, including London, Pittsburgh, and Hong Kong, have deployed cobots for floor cleaning, so that the humans can focus on sanitising kiosk screens, cleaning workstations, and so on.
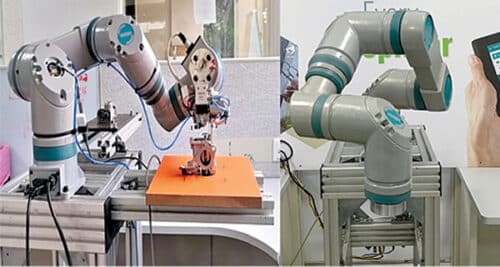
Pune based Peppermint Robotics’ robotic scrubber dryer is an intelligent and connected robot, replete with eleven levels of safety, four different types of sensors and cameras, dynamic pressure for different types of floors, and a dashboard for real-time reports. It cleans most areas by itself, but if you want to guide it into a difficult corner to clean, you can do so with a remote or by asking it to ‘follow’ you!
Gary is a household chores cobot developed by Unlimited Robotics, Israel. It can take out the laundry, work with a dishwasher, water your plants, clean the floor and windows, press your clothes, and serve snacks. It is open for pre-booking now. That sounds pretty much like Rosey of the Jetsons’ fame.
Professor C. Amarnath, known as the Father of Robotics in India, has mentored several students and their startups. He feels scrubbing of vessels, basins, and toilets is also a potential task for cobots—restaurants, hospitals, they all need it. It requires a different kind of arm movement but is definitely something that cobot makers should explore.
Assisting in healthcare—from tests to talks
Cobots are slowly being adopted by the healthcare industry for varied tasks, from sample sorting and patient monitoring to elderly care and surgical assistance.
Testing. In labs, cobots help with sample sorting as well as testing. A couple of years ago, ABB demonstrated a mobile lab concept at the Texas Medical Center in Houston. Around 2017, the Copenhagen University Hospital lab was burdened by over 3000 tests per day. Two UR5 cobots were deployed to assist the lab technicians. Even though the workload went up by 20% thereafter, the lab was able to get 90% of the tests done within an hour. Cobots like the Dobot M1 Pro four-axis selective compliance articulated robot arm (SCARA) can pipet and mix chemical liquids for lab testing. During Covid times, cobots assisted several labs to handle the burgeoning load of PCR tests.
Disinfection. In those trying times, many hospitals also used cobots to clean and disinfect beds and rooms, thereby protecting their staff. The eXtremeDisinfection roBOT (XDBOT) developed by the Nanyang Technology University in Singapore comprises a UR5 cobot equipped with an electrostatic spray nozzle, and installed on a mobile platform. It is effective for deep cleaning without the need for direct human contact.
Assisting doctors and nurses. Interestingly, Singapore has several functional cobot deployments. The country, known to be one of the most effective users of industrial robots—in the electronics sector—is now pioneering the use of cobots in spaces like healthcare. The Changi General Hospital (CGH), in association with the Centre for Healthcare Assistive and Robotics Technology (CHART), has deployed over fifty cobots in its 1000-bed hospital. The robots assist in jobs ranging from surgery and rehabilitation to delivering food and linen, lifting patients off beds and cleaning. Nurses often develop backaches a few years into the job, as they frequently lift patients. Cobots are really helpful here.
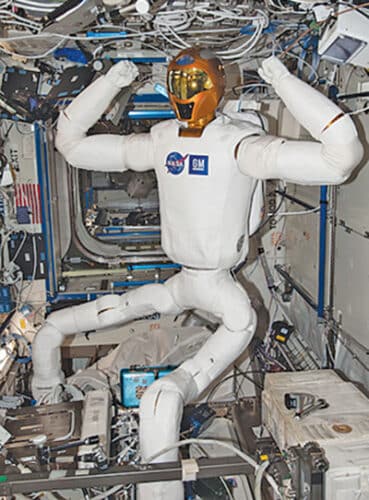
Social robots help care for the elderly patients, even playing memory games with those suffering from dementia. Some of the robots are designed to interact with people from different cultural backgrounds, in their native languages. In a media report, Selina Seah, Director of CHART, said, “One of the social robots, PARO, helped alleviate stress and anxiety so much the hospital was able to reduce its use of sedatives for dementia patients. We thought the aged patients would not take well to the robots. However, we discovered in our research that the elderly patients look at robots like life-sized toys. So, they are brought back to their childhood and, in fact, able to interact and respond better to therapy with robots than they do with a human.”
Since CGH uses robots from eight different manufacturers and running on different operating systems, it uses Robotic Middleware for Healthcare (RoMi-H), an open source system built on ROS 2, to ensure that the robots can communicate and cooperate with each other.
There have been similar deployments in some hospitals in Japan too. Last year, Hanson Robotics unveiled Grace, a humanoid robot that can assist doctors and interact with patients. In May this year, ChristianaCare, a network of private, non-profit hospitals providing healthcare services in Delaware, USA, purchased five Moxi cobots to work alongside nurses, performing nonclinical tasks such as deliveries and pickups, so that the nurses will have more free time for care delivery.
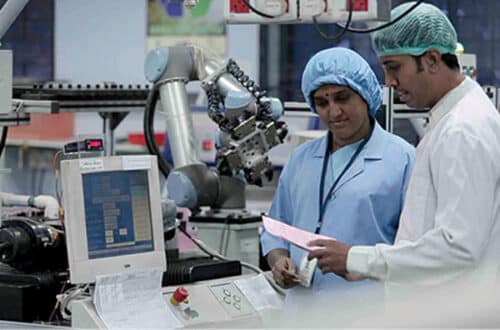
Assisting in surgeries. Bangalore based Articulus Surgical is focused on building portable and affordable surgical cobots. With appropriate tooling, collaborative robotic arms can align and hold a tool, or even provide a quick body scan, or read other vitals.
Toronto based Synaptive Medical offers a suite of robotic tools, such as point-of-care magnetic resonance imaging (MRI), automated tractography segmentation, and fully-automated robotic digital microscopy with 3D visualisation and AI-enabled voice-activated control that can help neurosurgeons.
And then there is Carlo, a cobot that can cut bones with extreme precision using cold lasers. And, ultimately, there is the famous da Vinci surgical system. “It is a very advanced machine that can perform robot-assisted minimally-invasive surgery remotely controlled by a set of surgeons. This is a real cobot. To be frank, as I have seen in person, it is safer than a human operating, due to its sophisticated sensing, control and intelligence. The system decides and can caution the human surgeon about the best instruments, cutting depth and pressure during the surgery. Yes, cobots are perfect for healthcare and therapy. In fact, they could be very efficient and dependable assistants to doctors, paramedics and caregivers in hospital wards,” says Gurappa.
Serving food and happiness
“Cobot technology is evolving rapidly. Today’s cobots are not only used in industrial processes but also in customer-facing environments, such as in food and beverage industries where cobots are deployed to prepare and serve food at restaurants,” remarks Sougandh.
Guests are delighted when robots Champa and Chameli take orders and serve food at the Robot Chef restaurant in Bhubaneswar. Those dining at the Yellow House Robot Restaurant in Jaipur and Noida, and Chitti in Town in Hyderabad, also get to enjoy the company of robots.
While in India robot servers are deployed just to up the glee factor, in places like Palm Beach County, Florida, it was an absolute necessity after the pandemic, as guests started arriving but employees did not! Cobots like Bella came to the rescue of restaurant owners there.
Cobots are being deployed in almost every field. How about Spot—the cobot from Boston Dynamics that scans a building under construction to avoid flaws, the smart cobot from Bloomfield Robotics that inspects vineries and notifies when the grapes are ready for plucking, the UR cobots used by NASA to inspect aircraft fuselage, or ABB’s PixelPaint-equipped cobot that can apply any design you show it on a car’s body?
Cobots being safer and less expensive are also being used by schools and colleges to teach students about automation. “As more and more businesses from different sectors begin to embrace automation, the use of collaborative robots will become more common,” says Guruprasad. With existing and emerging use cases, ABI Research predicts that cobots will grow from 5% of the global robotics market to 29% in 2030.
Do we need cobots in India?
In a country like India where labour is available in surplus, there is a general opinion that we do not need cobots. This mindset has even led to several robotics startups giving up their cobot plans. However, potential users have to evaluate cobots keeping the basic premise in mind—that cobots are here to work with human workers and not replace them. With lifestyle diseases cropping up, and health departments cracking down on various industries, it is essential to improve the working conditions of human workers by giving them an able helping hand that will reduce their physical strain, avoid unergonomic activities and keep them away from hazardous substances.
Guruprasad feels that, “In low-cost labour markets like India, utilisation of cobots is driven more by the ease-of-use and coexistence features of collaboration. There are multiple industrial applications which require even intermittent collaboration. For example, in machine tending, an associate is required to change various parameters of the machining centre on a trial-and-error basis on which the robot is being used for tending. This is possible on a seamless basis through cobots.”
He adds that the market is expanding, with the rise in automation demand, the availability of inexpensive, energy-efficient industrial cobots and the increase in R&D spending. Emerging economies have started adopting industrial cobot based solutions and, unlike earlier, when they were used by only the automotive and manufacturing sectors, now they are being picked up by other sectors like food and beverage, metals, chemical and material industries, aerospace, and electronics too.
Sougandh explains that cobots are also economically-viable in the Indian scenario. He says, “Repeated activities wear out employees, resulting in production mistakes. Unlike humans, cobots can work 24/7 while maintaining high accuracy and precision round the clock. This further leads to the reduction of manufacturing costs and the elimination of waste. Since cobots are easily programmable, employees without a programming background can easily operate a cobot. Hence, manufacturers need not spend additional sums to have an engineer on-site. In addition, cobots provide a rapid return on investment (RoI), and that too in a short span of 12 months.”
A few years back, Aurolab, an Indian manufacturer of eyecare products, deployed cobots from UR for assisting human workers in the manufacture of their cataract kit. The manufacture of intraocular lenses requires high precision and accuracy, as it is pivotal to regaining eyesight after the surgery. After deploying eight UR robots to assist employees in tasks like material handling, there was a 15% increase in the product output, with over 2,000,000 lenses per year.
Indeed, the future of collaborative robots is getting better by the day, with users slowly understanding the benefits. According to a new report from global tech market advisory firm ABI Research, the cobot market is set to grow substantially over the coming decade. The market had a global valuation of $475 million in 2020, which will expand to $8 billion in 2030, with a projected CAGR of 32.5%.
Janani G. Vikram is a freelance writer based in Chennai, who loves to write on emerging technologies and Indian culture. She believes in relishing every moment of life, as happy memories are the best savings for the future