Before electronic circuits based on printed circuit boards (PCBs) found their advent in industrial applications, electrical conductor wires were protected against short-circuits by applying a coating based on organic resin. With the use of PCB for connecting different components together and development of circuits capable of operating even under extreme conditions, such as in tropical climates and the military, space and automotive sectors, the requirements of protective properties for electronic circuitry have increased.

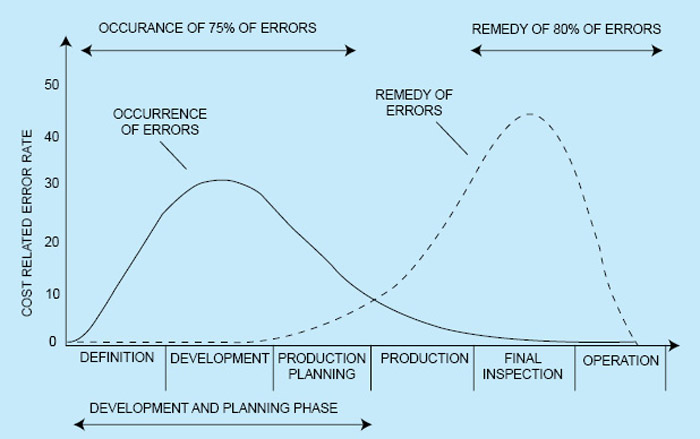
Polyparaxylene was employed in the early stages of electronic circuitry as a protective coating in military applications. Its use in other industrial mass production failed due to the high cost of the material, application costs, and especially the costs for masking (covering of areas that should remain uncoated).
As an alternative, inexpensive materials modelled after wire coating were sought for mass production, keeping their coating costs and protective properties in mind.
Therefore coating materials like ‘Tempomatlack’ were created in the mid 1970s, which were based on oxidation-cured polyurethane resins. This material was suitable, due to its viscosity for both dip coating as well as manual application with a brush. In the course of development, coating materials based on epoxy resins, acrylic resins and silicones were added, which, in various modifications, also met requirements for development of coating technologies such as spray coating and selective coating.
The coating materials also had to be adapted to the latest additions in drying/curing processes. The demand for reduction in emissions led to the emergence of coating materials with reduced organic solvents in view of the volatile organic compounds (VOC) guideline, water-borne lacquers and solvent-free UV hybrid lacquers.
Why are electronic assemblies provided with a coating material
Besides the solder joints recessed by the solder resist, there are also various potentials in contact with the different components on the PCB that are not shielded. Depending on the requirements, conformal coatings, thick-film coatings or casting compounds can be employed to shield against such potentials. Their main task is protection of the completed assembly against malfunctions or failures in robust operating conditions.
For this purpose, the Institute for Interconnecting and Packaging Electronic Circuits (IPC) Standard, under IPC-T-50 terms and definitions, defines a conformal coating as being “an insulating and surface-compliant coating which represents a protective coating against the detrimental influences of the environmental conditions…”