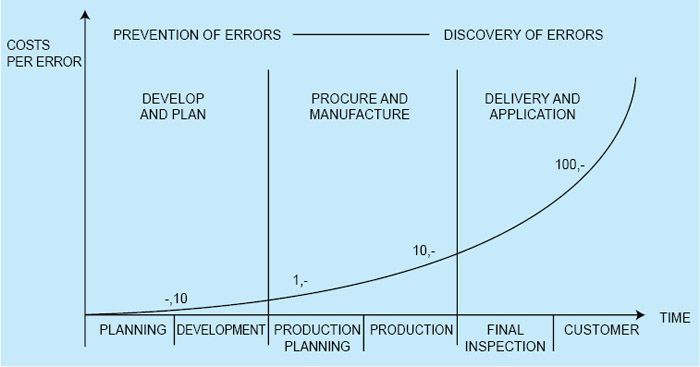
For market success of any electronic product, reliability and customer satisfaction play decisive roles. Therefore manufacturers take necessary measures to ensure that their electronic equipment function properly even under demanding conditions. This is especially true for assemblies which are incorporated in aerospace and military, medical and also automotive systems (engine control, electronic central locking, electric windows and air-bags). In many cases, worldwide marketing of electronic components is possible only if these have a protective coating.
Coatings are employed for different requirements of the system:
1. Mechanical protection, e.g., against mechanical abrasion, vibration, minor impact loads
2. Corrosion protection, e.g., against atmospheric humidity, dew-point condensation, hand perspiration and diverse chemicals
3. Protection against mould infestation when employed under tropical conditions, for minimising dendritic growth
4. Improvement of electrical insulation between two potentials, e.g., in case of requirements for explosion protection and in case of high-voltage stress, particularly at greater heights
In case of higher stress, particularly aggressive industrial atmospheres and exposure to material such as fuels, oils and lubricants, a one-component conformal coating no longer offers sufficient resistance; two-pack conformal coatings or casting compounds are employed to protect such electronics.
In practice, electronic assemblies are always more or less tolerant to normal range of humidity. Under ‘normal’ circumstances, i.e., approx. 40 per cent to 70 per cent R.H., a problem-free operation is normally ensured. At a humidity level above 70 per cent, proper operation becomes critical. Increasingly, humidity absorption becomes negatively noticeable in the form of possible leakage currents. The first signs of dewing behaviour may appear because the critical relative humidity of many salts has already been reached. For a reliable operation with the possible danger of dewing, a protective coating is advisable. (See Fig. 1)
The possibility or necessity for a protective coating should be considered during the planning phase, or it should be incorporated at an early stage into the design of the assembly. Care has to be taken here in the choice of components with respect to their coatability and layout specifications for the coating process. The latter can include space requirements for non-coatable areas as well as arrangement of edge connectors.