In this connection, views concerning the occurrence and remedy of errors during a product life-cycle are important. It is said that 75 per cent of errors occur during the planning and development phase, whereas 80 per cent of the errors are remedied only during the final inspection or during operation. (See Fig. 2)
Of further consideration is the so-called ‘decadic law of error costs,’ which states that the error costs increase by a factor of ‘ten’ in every phase of the product life-cycle. (See Fig. 3)
The cost-driving variables can be, for example, non-optimised coating processes such as layout-related complicated selective coating instead of cost-effective dip coating in the multiple-use carrier. In particular, possible incompatibilities and their elimination from up- or downstream processes of the coating process can also assist in the run-up, in order to keep coating costs down.
In this context, it should also be observed that only a well-applied coating that has a verified compatibility to preliminary processes provides high-quality protection to the electronic assembly against the loads expected.
Requirements set upon coated assemblies
Requirements concerning climate resistance coupled to mechanical and/or electrical properties have to be maintained, in relation to their protective effect, under the most diverse climates for electronic assemblies.
Fig. 4 shows the possible climatic loads (in terms of ambient parameters or disruptive factors) that can occur during the operation of an electronic assembly.
A fundamental requirement from an electronic assembly is that, in the case of dewing conditions—when considering various climatic conditions—the functional reliability is ensured. In particular, the combination of high temperature and high humidity constitute a high load, especially when temperature fluctuations lead to dewing.
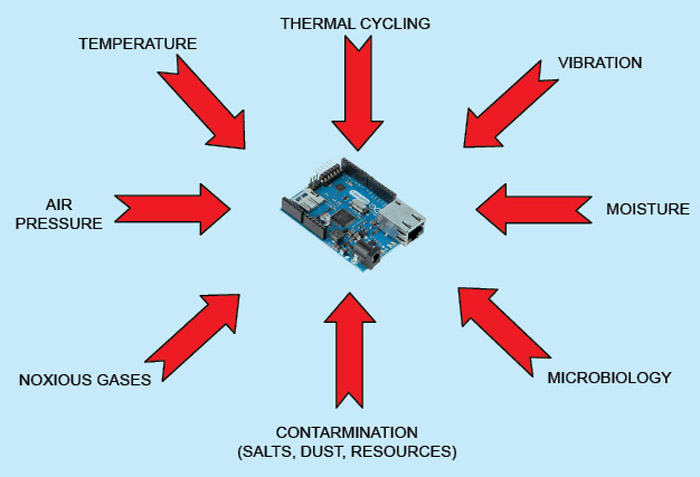
The basic demands for conformal coatings or casting compounds are derived from various requirements of the subsequent application. For this purpose, products with suitable material properties have to be chosen.
Some of the material properties to be considered are listed in Table I.
In addition, there is the processability as well as the costs for procurement and processing and, last but not the least, possibilities for recycling or safe disposal.
Another important aspect with respect to requirements is reliability analysis of coated electronic assemblies. By definition, a reliable product fulfils its function under specific operating conditions within a promised life cycle. Particularly in the case of automotive electronics, reliability plays an increasingly important role. Electronic components are used in many safety-relevant areas of automobiles. Examples of such applications are air-bag control units, control systems for anti-lock braking systems and electronic control units for the advanced driver-assistance systems.
As a matter of principle, reliability is important for all electronic products. Faulty operation and failure in subsequent operation lead to warranty and goodwill costs. The reliability of a product is essentially determined during the concept and development phase of a product. The variables that primarily affect the reliability of an electronic assembly are temperature, vibrations and moisture.
Particular attention is to be paid to these disturbance variables. Of particular importance are the appropriate acceleration models and accelerated tests for these disturbance variables, in order to ensure a sound interpretation and evaluation.
Statements concerning the reliability of electronic assemblies are usually made after conducting specific qualification tests. Service lifetime is determined by the foreseen designated use.
These numerical values are no absolute terms; the requirements change with time. Particularly, temperature limits change continually, especially towards higher temperatures. A wide variety of workgroups are discussing extended requirements for the automotive sector. These are already partially employed in the test series:
1. Thermal cycling test (shock) to 3000 cycles (temperature range -55°C to +150°C)
2. Load under full operation (electrically connected) to 1000 cycles
For electronic assemblies, the most often applied reliability tests include mechanical reliability, material reliability, electrical reliability and climatic reliability/functional reliability tests.
This article is an extract from the book titled ‘Conformal Coatings for Electronics Applications’ by the author