The Ministry of Electronics and Information Technology(MEITY) has recently concluded the SemiconIndia-22 conference with the aim to promote India as a global hub for semiconductor design, manufacturing and technology development to bring India on the world semiconductor map.
During the conference, it was stated that India has a strong footprint in chip design and there are plenty of chip design/ R&D centers in India run by leading chip makers and fabless companies. These companies have been designing chips using Indian talent, creating intellectual property and reaping huge profits but have never ventured into chip manufacturing in the country.
It was also brought up that the missing links in the Indian semiconductor value chain are primarily wafer fabrication, package and test areas. Equipment and material vendors of the semiconductor ecosystem start providing services once chip manufacturing scales.This scenario may not change unless India promotes the local semiconductor industry through the public-private partnership model.
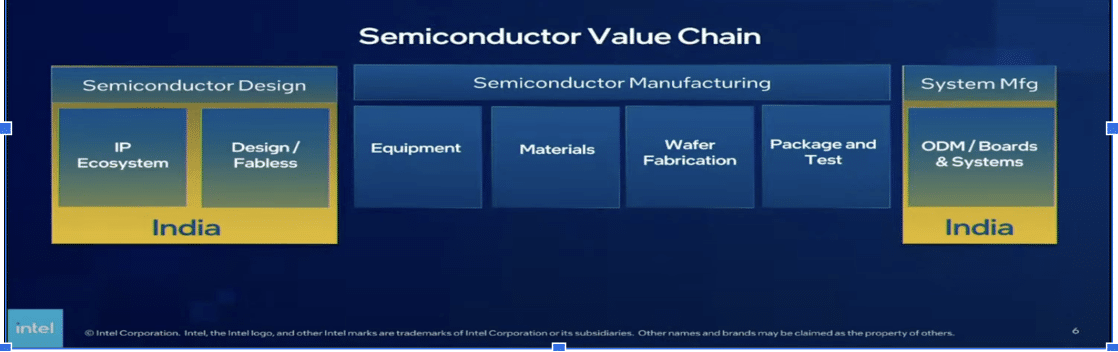
Normally it takes three to four years to build a chip plant. To keep a chip plant operational, it is run round the clock to maintain clean-room conditions and carry out the process recipes. This can be quite expensive. Thus it is imperative to load the plant as soon as possible to recoup the up front costs and meet operational expenses. India needs to identify and start designing at least five to ten types of chips having sizable market demand to load the plant.The work on designing those chips should start now.
Theodore Roosevelt had once said, “We must either wear out or rust out”. It is better to work hard, wear out and flourish rather than lying dormant, rust out and disappear. Indian engineers and scientists therefore, will have to soil their hands to make this happen else it will be a non-starter. Since setting up a chip plant involves massive capital investment, the government can help and encourage Indian entrepreneurs to rise to this challenge.
We need to start looking for potential areas where chips get used in large numbers. The author has suggested some areas and proposed a roadmap for setting up a mega chip plant in the country in an earlier article titled India’s Resolve for Self Reliance in Microelectronics dated 12th April, 2022. As a sequel to this article, a favourable market segment identified for the ‘First National Chip Project’ has been described.
Challenges of discoms
Our country has been incurring heavy Aggregate Technical and Commercial(AT&C) losses due to theft of electricity, inadequate metering and poor recovery of electricity bills. This has enormously impacted the distribution companies’ (Discoms) financial performance1.
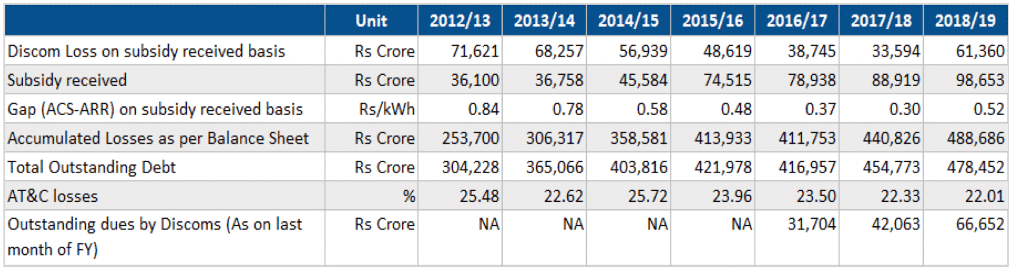
The distribution losses in some of the states are as high as 56% (Arunachal Pradesh). Even after the enactment of the Anti-theft legislation of 2007, annual distribution losses are on the rise. The losses of 62 discoms put together were Rs 90,000 crores during 2021 with a national average of 24.54% compared to 4% in Japan, 5% in China, 6% in the USA and a world average of 8%2.. If large countries such as the USA and China can contain their losses, why is this a challenge for India?
If we bring down these losses to the world average of 8%, we can replace our entire 25 crore conventional meters in a few years out of accrued savings. This can be made possible through improved distribution infrastructure, administrative measures and installation of smart meters. State-wise distribution losses are shown along with losses of other countries in the following chart 2.
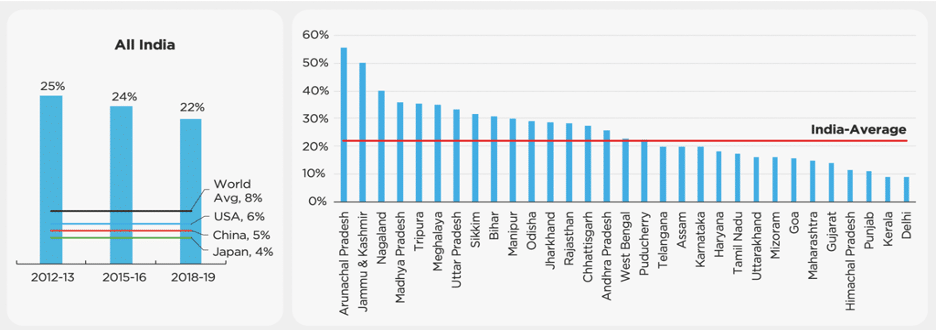
If we bring down these losses to the world average of 8% through improved distribution infrastructure, administrative measures and installation of smart meters, we can replace our entire conventional 25 crore meters in a few years due to accrued savings on account of reduced distribution losses.
Electronic energy meter manufacturing
Historically, the installation of electronic energy meters started in India around the mid 90s. Semiconductor Complex Ltd, HPL India, L & T, Landis & Gyr, Secure Meters, Avon meters and Genus were some of the companies instrumental in manufacturing and selling electronic energy meters in the country. These organisations together produced more than 20 lac meters annually during the 2000s. More than a dozen organisations are manufacturing electronic energy meters now in the country.
During the last two decades, more and more features have been added to electronic energy meters to make these “smart”, similar to cell phones to address needs of the Indian Discoms and electricity consumers. The features include online capturing of metering data, monitoring and control of power consumption and meter tampering, ability to convert postpaid meters to prepaid, integration with the power grid, auto meter reading capability and making online bills payment possible. These features help Discoms reduce their distribution losses and also lowers down human intervention.
Smart meter national programme – An opportunity
The decision by the Ministry of Power to replace conventional meters with smart meters throughout the country is a step in the right direction2. Under the Smart Meter National Programme (SMNP), the Ministry aims to replace the country’s 250 million(25crore) conventional meters with smart meters on a build-own-operate-transfer model 2. Energy Efficiency Services Limited(EESL), a joint venture set up by National Thermal Power Corporation, Rural Electrification Corporation, Power Finance Corporation and Power Grid Corporation of India has hit around 1% of the installation target with 2.5 million smart meters installed in Uttar Pradesh, Madhya Pradesh, Bihar, Haryana and Manipur.
The smart meter is a major component of the revamped distribution scheme proposed by the government in the 2021–22 budget. The total expenses to the tune of Rs 1.5 lac crores are likely to be spent on the SMNP project3. This brings a big opportunity to manufacture smart meter chips to help make these meters indigenous with more local components. The demand for electronic metering chips shall remain high in the next 8-10 years.
First national chip project
Semiconductor Complex Ltd(SCL) had initiated design of the energy meter chip in the late 80s. The design, however, could not be completed due to devastation of the chip plant in a fire incident during 1989. Perhaps designing a meter chip by SCL was ahead of its time and the focus upon rebuilding the chip plant remained on standard VLSIs, Application Specific ICs (ASICs) and strategic devices. Energy meter chips are still imported from Analog Devices and Atmel of the United States, ST microelectronics of France, SAMES of South Africa and Chinese companies.
Why is indigenous manufacturing of energy meter chips a good candidate for India’s first national chip project? It is the author’s opinion that meter chips have a mass market and will remain so for a long time. Energy meter chips, unlike cell phones, microprocessor and memory chips, do not necessarily require lower geometry technologies and can be produced in 90nm or larger 180nm technology nodes. The meter chips can be standarised with minimal variants by Discoms based on nationally agreed meter specifications. The specifications and manufacturing challenges of meter chips are less stringent compared to memory, microprocessor, mobile and automotive chips due to their lower geometries, higher transistor count, processing speed and operating environmental conditions etc.
It’s time to manufacture meter chips!
To become self-reliant, an action plan for manufacturing meter chips is proposed for the first national chip project.The time to take action and start working on the first national chip project is now.
- MEITY to help prepare and standardise specifications of single and polyphase smart meter chips in coordination with EESL, Discoms, a few chip design companies and meter manufacturers.
- Get the meter chips designed by at least two design houses for a higher success rate.
- Manufacture chips in a local and foreign foundry, later transfer to the new chip plant when ready.
- Integrate the meter chip with MOUSHIK SoC RISC-V processor developed by IIT Madras, fabricated by Semi-Conductor Laboratory and offer complete metering system solution to the Indian meter manufacturers.
The extent of planning, effort and dedicated team work that goes into chip designing, manufacturing and offering solutions to the end users is enormous. ‘Roses do not grow on the road side whereas wild grass does’. It takes almost a year of hard work before a rose shows up after its stem is planted, is a fitting analogy.
MEITY and the Ministry of Power should work together in a mission mode to make it a success. This will be a first milestone to develop an ecosystem for the semiconductor industry. More such projects should be identified for undertaking chip design and manufacturing to load to the Indian chip plant.
References:
- Report of Institute for Energy Economics and Financial analysis August 2020.
- NITI Aayog Report “Turning Around the Power Distribution Sector- Learning and Best Practices from Reforms” August 2021.
- The Ministry of Power ‘revamped distribution Scheme’ to reform discoms.
By Ajay Saini, Former Group Director, Semi-Conductor Laboratory, ISRO email: [email protected]