A vast expanse of applications is driving innovation in micro-electro-mechanical systems (MEMS), feels Uday Prabhu, general manager, electronics product engineering and product management, Robert Bosch Engineering and Business Solutions Pvt Ltd. Let us find out how as he talks to Dilin Anand and Priya Ravindran of EFY about the growth and scope of MEMS technology
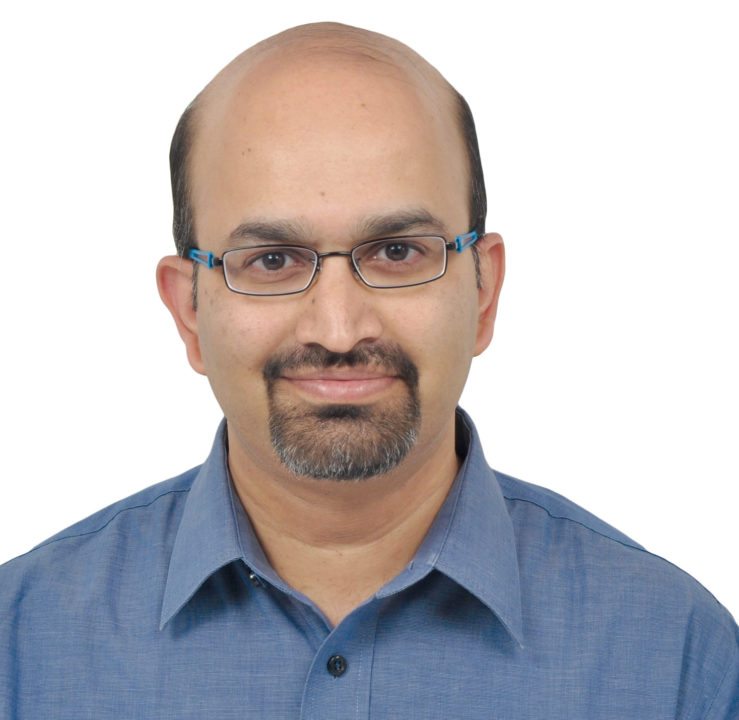
Q. How has MEMS technology grown in the last five years?
A. From a research and development perspective, MEMS has seen an explosion of sorts and quite a few diversifications. It started proliferating in the automotive segment, with regards to electronic stability programme.
The technology then exploded in the consumer space, with increasing demand for smartphones, gaming devices and wearables, so much so that companies currently manufacture about five million MEMS sensors each day.
Q. What are the primary enablers for the improvement of sensors?
A. MEMS is about how best we can integrate mechanical structures into printing on electronic substrates. People are now looking at the fundamental physics of sensing. The number of axes that we use determines the kind of resolution we can achieve with respect to gathering information about the moment, and we see an expansion in the sensing dimensions.
New sensing elements like pressure, humidity and other environmental parameters are coming out. Any physical element that can be leveraged for sensing is now being transformed into MEMS. Also, upgrades in the process of production have resulted in smaller form factors.
Q. Please tell us more about these upgrades?
A. There is compression happening on a large scale. An increase in the number of transistors that can go into a chip has resulted in reduced size with higher functionality. Earlier, MEMS elements functioned exclusively as sensing elements. Now, intelligence, which is the processor, is built into the MEMS chip itself.
This is the primary influencer for the wearables segment, with MEMS chips doubling as control units. Structural advances also help make finer measurements of acceleration, momentum and so on.
Q. What parameters should be taken care of while integrating a MEMS sensor into a wearable application?
A. It is very important to engage the sensor in the right manner. Take the case of Fitbit. The accelerometer has to be positioned along the direction in which acceleration is to be measured, for accurate measurement.
A rugged laptop has an accelerometer placed vertically. If the laptop is dropped, it immediately puts the hard drive in safe mode, to prevent damage or loss of data. Any change in its orientation will not protect the laptop.
Q. Available wearables have to be connected to a smartphone for analysis. With advancements, do you see the entire system compressed onto the MEMS set-up itself, without offloading data?
A. We have to look into three categories. Sensing and processing should follow their own evolution paths, with processing predominantly following the Moore’s Law.
The communication roadmap also needs to accommodate this change, which means getting 2G/3G into smaller packages. However, their power requirements are very high and it is not possible to fit this into a small gadget.
Thus, there is a need for the other side, where we have multiple technologies. It is good to separate fast- and slow-moving technologies. Otherwise our wearables will become obsolete very fast and may not support usage with a new, upgraded phone.
Q. What latest trends are being driven by MEMS?
A. Air-quality testing is a requirement that is catching up fast. In the case of outdoor pollution, focus is on pollutants from vehicles and industries, while in indoor, the onus is on proper ventilation.
The biggest problem is with regards to volatile organic compounds, which are the fumes released from upholstery like furniture and plastic. These could also lead to gloominess in the environment.
From the perspective of representing air quality, there have been quite a few interesting applications. One such is the integration of MEMS sensors into a painting of Mona Lisa; when the air quality goes bad, her lips turn blue, and stay pink otherwise.
Another area is indoor location monitoring, where a measure of momentum helps arrive at the direction and coordinates of your movement.
Q. How does indoor location monitoring work?
A. In this case, MEMS are used as counters. A combination of sensors is used to determine not just your position but also the direction in which you should move. Three beacons are used to achieve triangulation and a conversation is carried out between the beacons and the connected device.
A simple time-of-flight measurement for this question-and-answer session gives you the position of the device, relative to the beacons. MEMS are used to find coordinates, while magneto sensors give the direction. These are then used to tell you the number of steps you need to take in a particular direction to reach your destination.
Q. Do you see any influence of MEMS in the telematics industry?
A. Yes! Adding to distance the direction measure from point A to B, the telematics industry is looking at a three-dimensional perspective of maps. Being called e-horizon concept, MEMS sensors can be used to provide information about the gradient or geography between places. It could be data on the altitude upfront or whether the surface is rocky. An auto-driving car could use this information to prepare itself for the drive.
Another application in this industry is for understanding how good a driver is. MEMS sensors are used to study and understand driving patterns such as how the driver accelerates, decelerates or applies brakes. This can be used for analysing driving patterns, maintenance of the vehicle and also to predict its life.
Also booming is the e-call concept, where data is used to interpret a crash or an accident and immediately alert emergency services, automatically.