Industrial automation products cover a gamut of applications such as remote monitoring, programmable logic controllers (PLCs), human machine interface (HMI), robotics and so on. Let us explore and consider the pros and cons for embedded development platforms that can be used in building these products.
Cost and labour optimisation has created a huge demand for industrial automation products in a variety of industries. Apart from tangible reduction in manufacturing and labour costs, replacement of human labour with precise and rugged control systems also adds reliability to the manufacturing of goods and products. Industrial automation products are application- and industry-specific. Owing to the specificity of products’ use, their sales volume can be as low as 20,000 to 30,000 per year.
Challenge for OEMs
Usually, embedded development involves high non-recurring engineering and manufacturing costs, so low sales volume creates a non-optimal cost structure. Economies of scale cannot take effect due to low sales volume, so the original equipment manufacturers (OEMs) have to bear higher overhead costs.
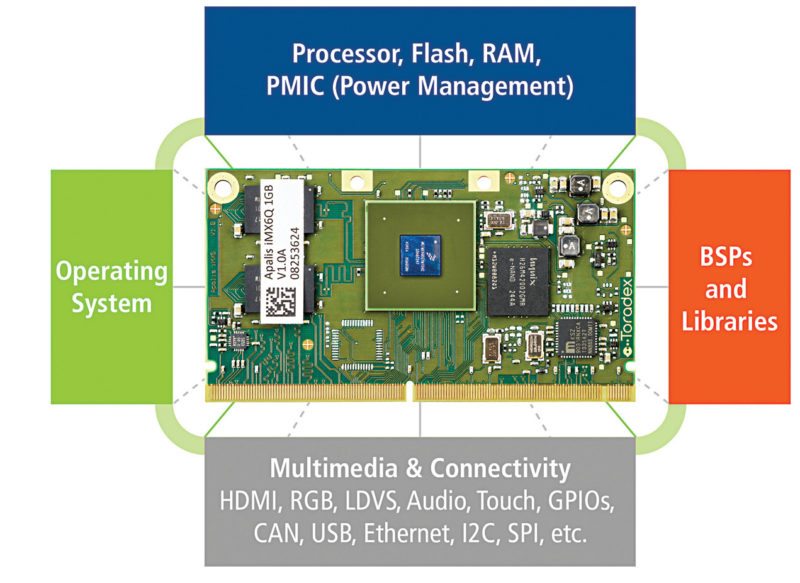
Long product life. Although OEMs carry out multiple sourcing of components, long life of industrial automation products adds burden to the supply chain. Component obsolescence has to be handled throughout the product life of ten years or more.
Industrial automation includes products such as PLCs, HMI, robotic arms and more. These can be used in a variety of industries including marine, automotive, medical and food processing, among others. As the products are used for ten years or more, these should be supported for an extended period.
Embedded development: build versus buy
Chip based development or full custom development offers flexibility to OEMs to build products as per their budget and application requirements. However, owing to low sales volume, chip based development is not an ideal option for achieving cost optimisation. Full custom designs are preferable only if sales volumes exceed 70,000 to 80,000 per year.
Since industrial automation products are usually application- and industry-specific, sales volumes are not high enough to recover the investments in engineering and manufacturing. In order to generate positive economic returns, OEMs prefer to use the platform for longer duration to increase overall sales of the platform. However, this strategy has an issue.
Technological advancements happen at a faster pace and, thus, a platform becomes outdated in less than two years. As predicted by Moore’s Law, the innovation cycle of processors leads to faster, power-efficient, smaller and cheaper solutions every two years or so. To catch up with new technologies, competitors and customer expectations, OEMs are bound to upgrade the platform, leading to substantial investment.
Another problem with chip based development is that it is not scalable. Future enhancements cannot be accommodated in an existing platform. A new platform with the latest technologies has to be built instead.
Yet another problem arises from the long life of industrial automation products. Customers need extended availability and support for products, as these are used for ten years or more. However, supporting a platform for such a long period becomes an issue.
Each and every component on the platform should be available for at least ten years. Since this is unlikely in many scenarios, OEMs use a risk-mitigation strategy of multi-sourcing components. Still, when a component reaches its end of life, the platform has to be revalidated with the new replacement component. This involves some cost and labour.
Let us now consider the buy option for off-the-shelf embedded computing platforms, since these are being widely used for embedded development.
Fully-integrated solutions
Single-board computers (SBCs) offer a ready-to-use embedded platform comprising firmware and hardware, including system on chip (SoC), memory, power requirements, interfaces such as universal series bus, controller area network, high-definition multimedia interface, ethernet, display and the like on a single PCB, for building any end product.
OEMs select SBCs best suited for their requirements and then develop the application software.
In SBCs, processing and input/output (I/O) sections are integrated on a single PCB, so performance enhancements based on the latest technologies and customer demands are not possible. For example, let us assume an HMI is based on an SBC that can offer a peak frequency of 500MHz. After a year, the market may demand an HMI with 1GHz frequency. If so, the OEMs have to use a new SBC, which can support 1GHz. The entire platform has to be redesigned in that case.
Further, SBCs are available with fixed I/O types and configuration. Adding new peripherals will require interface boards, which are not ideal for size-constrained applications. Thus, SBC based platforms are not flexible. Component obsolescence is not OEMs’ concern any more, as vendors start offering the latest SBC.
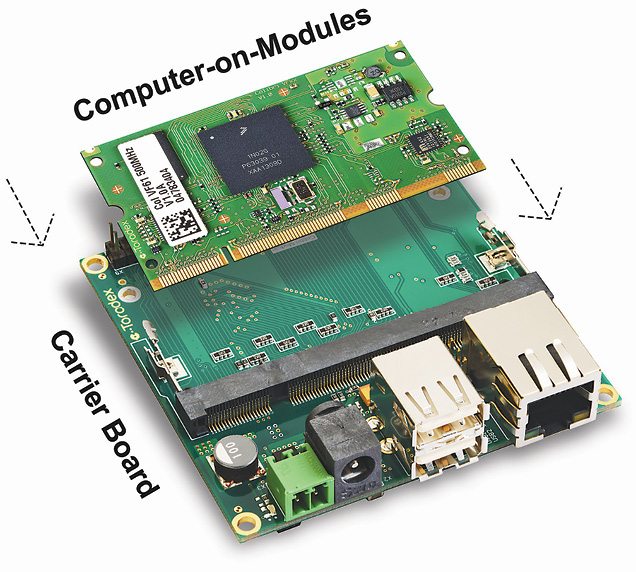
Cost-effective alternative
A computer on module (COM) or system on module (SOM) is a cost-effective, reliable and ready-to-use computing solution that consists of the essential design commodities such as processor, memory, power circuitry, operating system, board support package, etc. SOM is connected to a carrier board, which houses I/Os by means of some connectors such as a small-outline dual-inline memory module. OEMs can design carrier boards based on their I/Os, configuration and size requirements.
Design scalability. Pin-compatible SOMs enable plug-and-play for scaling up platforms based on future technologies and market requirements. New SOMs can be easily connected to existing carrier boards, and the application software may need some minor updates.
Taking the previous example, consider that the HMI is based on an SOM, which can run at 500MHz. The platform can be easily upgraded to operate at 1GHz by migrating to a SOM that supports 1GHz operating frequency. No change in the carrier board or application software is needed in this case.
Design flexibility. By using SOMs, computing and memory section is isolated from I/O section. OEMs can design and develop carrier boards as per their size and configuration requirements and then connect an SOM to it. The entire platform, which has the least possible size, is tuned to OEMs’ design requirements.
Conclusion
To sum it up, buy option for embedded development seems more suitable for industrial automation products. This would control the development cost and time-to-market better than with build option.
Further, while choosing between SBC and SOM platform options, SOMs are better equipped to handle the challenges of OEMs caused due to long product life and low sales volume.
Prakash Mohapatra is product manager at Toradex