Second, the concept of machine operators is becoming kind of archaic. Machines can work by themselves. Technically, these can be operated and controlled by anybody from anywhere. They can even be managed by other machines, through machine-to-machine communication and peer-level synchronisation. They can be controlled by intelligent sensors and other measurement devices. Some intelligent systems can even take care of contingencies—they can automatically detect faults and anomalies and fix them as they have been taught to.
Of course, all this does not happen completely devoid of human participation. It is human programming that teaches the machines how to function and control themselves. Plus, engineers continue to monitor the systems and intervene in extraordinary situations. But even this has become easy, as engineers can watch and control the entire factory using user-friendly dashboards on small handheld PCs or even their mobile phones. What’s more, machines become less intimidating when seen through simple software interfaces, and it is easier to tell them what we want them to do.
Third, the factory per se is becoming a very flexible and logical entity now, thanks to automation. It can be reprogrammed to work in different ways, and even produce different things in different quantities and different speeds—and quite easily too. Hence a bunch of machines need not keep functioning in the same way all their life. This flexibility, which has been brought about by the ability to control the machines at a logical level through simple software interfaces, helps meet the ever-changing needs of consumers in a fast and inexpensive way!
In short, the factory is becoming a very integral part of the entire enterprise and its varied management in-formation systems. This trend is being fuelled by multiple technologies at various levels—embedded systems, wireless technologies, artificial intelligence, industrial networking, advanced software engineering, mobile devices and networks, security and more. These technologies are constantly evolving, contributing to further growth in the industrial automation space too.
[stextbox id=”info” caption=”Cookie-cutters to semiconductor fabs”]
Although pharmaceutical, life-sciences, automotive, semiconductor fabrication and other such industries where quality is crucial are the most eager adopters of automation, industrial automation is not confined to the large firms alone. Automation need not necessarily involve integrated, wireless-enabled, mobile-capable systems either.
Cookie-cutters, automated voice responses, simple process-control loops in small manufacturing firms, sensors that start or stop a hand blower are all examples of automation too! On another level, there are assembly lines that are completely automated, putting together micro-, even nano-scale components, controlling and managing themselves.
Both levels can be justly called as automation.
The primary motive of automation is to tap the predictability and dependability of machines – program a machine to do something and it will do it in exactly the same way even after the millionth iteration. Therefore the basic goals of automation are to achieve precision and uniformity, eliminate errors and improve quality, and enhance control over the entire process. Plus, automation also becomes indispensable for certain tasks which man really cannot handle—for example, even with a magnifying glass it would be difficult for you to put together a computer chip and make sure it is perfect. And a fabrication plant would have to churn out thousands of these chips within hours. Or, look at hazardous tasks such as handling chemical vats, which are not safe for humans. Such processes cannot really do without automation!
In general, it is found that the error rate of 1-1.5 per cent found in manual working can be brought down to 0.00001 per cent with automation. Automation also improves the efficiency of machines as processes are optimised. This reduces the cost of operation. As stakeholders begin to increasingly demand certain quality standards, automation has also become a key part of today’s manufacturing setup. It has penetrated the whole lifecycle of a product right from product engineering tasks like concept development, solid and surface modelling, engineering data porting, product design and reverse engineering, to product manufacture and quality control.
[/stextbox]
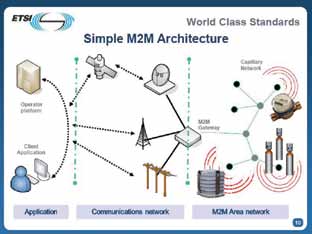
Let us take a quick look at five such recent technological developments in this space.
1. PC-based platforms gaining popularity
Dedicated embedded systems were doing well, no doubt. But too many technologies and too many standards were making life very difficult. As a result, a part of the industrial automation world is now moving from rack-mounted PLCs to more generic PC-based platforms… but not all of them!
“With a PC-based solution, you can integrate PLC control, motion control and your supervisory control and data acquisition (SCADA) requirements on a single high-performance controller platform. With a PC-based controller platform, your software and know-how investments are protected in the long run due to the use of standard control components. PC-based solutions also provide the flexibility of integrating the control solution with the enterprise resource planning and management information system (ERP/MIS) solutions,” explains Jitendrakumar Kataria, managing director, Beckhoff Automation.