[stextbox id=”info” caption=”So where are the robots?”]
If your idea of a robot is a walking, talking mechanical man, you will probably not find many on the factory floors! But if you take a practical view of what a robot really does, you will find them in many factories, especially in the automotive industry.
According to the International Standards Organisation, an industrial robot is an automatically controlled, reprogrammable, multipurpose manipulator programmable in three or more axes. So it is nothing but another ‘machine’! The mechanical hand that fits the engine into cars is a robot, really. Robots can be used for doing tasks like welding, painting, assembly, pick and place, packaging and palletising, product inspection, and testing speed, precision and reliability.
There are many kinds of robots used in industries, the main ones being articulated robots, gantry robots, selective compliant articulated robot arm (SCARA) robots and cylindrical robots.
“Gantry Robots, SCARA, articulated or parallel kinematics are highly dynamic handling devices with high repeatability, and require control systems that guarantee minimum delays for all sub-processes including physical signal sampling, processing in the motion controller and response at a physical output. Robotics also requires complex mathematical calculations based on the kinematic transformation required for the robot structure. It also calls for integration and coordination of the robotic controller with various other processes in the vicinity of robot. These requirements from robotics have challenged the industrial automation controller to provide single platforms which can fulfil these performance requirements,” says Kataria of Beckhoff.
Robotics is evolving quite fast. Robots are becoming more capable, both on the mechanical and intelligence fronts. Costs are also going down, if only slowly. As a result, robots are now beginning to play a greater role in industrial automation than before.[/stextbox]
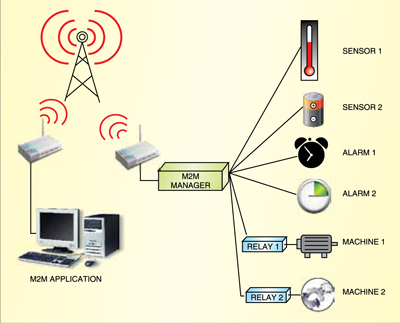
The need to connect multiple devices seamlessly for control data exchange, the increasing use of robots in manufacturing, and the constantly widening dimensions of industrial automation has led to a great demand for PC-based automation and industrial PCs. A PC-based control platform provides a single canvas to integrate all the control functions, visualisation functions and database features required by a manufacturer. It ensures speedy configuration, scalability, flexibility, fewer interfaces and open standards.
Companies such as Beckhoff and Siemens offer a variety of PC-based solutions such as industrial and embedded PCs, multi-core 64-bit PC-based controller systems, automation software, Web-based diagnostic solutions and so on. Such tools are fast gaining popularity.
We also see industrial versions of floating-point processors, dynamic random-access memory (DRAM), solidstate storage devices such as CompactFlash, fast Ethernet chip sets and field-programmable gate arrays (FPGAs) in industrial control products.
However, not everybody is game to replace their PLCs with PC-based options. They argue that the operating systems of PC-based controls are not designed and dedicated to providing uninterrupted real-time control. Further, they share their resources between applications and system activities. Some of these activities are under the user’s control while some are not. This affects the speed and repeatability of PC-based systems at a level that cannot be controlled by the user. From this viewpoint, PLCs seem to be more robust and reliable than PCs.
As a way around this dilemma, some vendors and end-users began to develop powerful software with the flexibility and usability of PC-based control systems that could run on real-time operating systems for reliability. Research firm ARC Advisory Group called these programmable automation controllers or PACs, and the name stuck! A PAC kind of merges the advantages of PLCs and PCs. It offers performance, flexibility and multi-discipline control comparable to PCs, along with the added benefits of reliability, speed, real-time connectivity and integration that can greatly simplify production processes. PAC products such as GE Fanuc’s PACSystems are emerging as a key contender for both PLCs and PCs.
James Truchard, president and CEO of National Instruments, explains in a recent report that the future of PACs hinges on the incorporation of embedded technology. One example is the ability to use software to define hardware. Consider FPGAs. “FPGAs are electronic components commonly used by electronics manufacturers to create custom chips, allowing intelligence to be placed in new devices. These devices consist of three main components: configurable logic blocks that can perform a variety of functions, programmable interconnects that act as switches to connect the function blocks together and input-output (I/O) blocks that pass data in and out of the chip. By defining the functionality of the configurable logic blocks and the way they connect to each other and to the I/O, electronics designers can create custom chips without the expense of producing a custom ASIC (application-specific integrated circuit). FPGAs are comparable to having a computer that literally rewires its internal circuitry to run your specific application.”
2. mobile-enabled manufacturing is finally materialising
When everything is going mobile, why not manufacturing too? While there has been a lot of talk of ‘mobile manufacturing’ or mobile-enabled manufacturing in the past few years, it was in 2009 that the concept actually picked up steam. Mobile manufacturing is basically a situation where your industrial automation systems can be accessed and controlled via a mobile network, using a PDA, laptop or mobile phone. Applications, services, infrastructure, standards and most importantly proof-of-concepts, are all emerging, making it a real concept and not a distant dream.