As mentioned earlier, several manufacturers have also realised the importance of the grey-collared mobile workforce, and invested in enhancing their role in the organisation. Some have adopted manufacturer-friendly applications from companies like SAP, Sybase, Microsoft, Capgemini, Wonderware and SAT Corporation, while others have developed their own mobile-enabled applications or added mobile capability to their existing systems. Having realised the power of the grey collar, manufacturers are even eagerly waiting for the roll-out of fourth-generation (4G) networks to invest further power in their hands—anytime, anywhere video conferencing, live demos and factory checks, remote troubleshooting by technicians and more.
[stextbox id=”info” caption=”If this is v2, what will v3 be like?”]Jitendra Kataria of Beckhoff says v3 will include use of:
1. Object Oriented Programming extension of IEC61131-3
2. Higher-level programming languages for programming PLC/motion control logic
3. Multi-core PC-based platforms which can do multiple tasks, viz, robotics, motion control and PLC, at the same time using different cores of the same PC-based system[/stextbox]
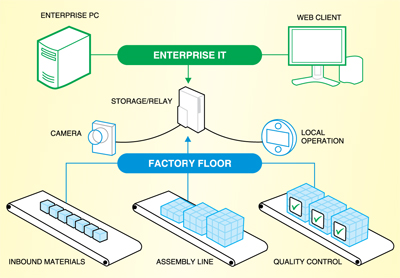
Rosy as the picture seems, in truth the large number of mobile devices and applications are not easy to manage. Each device is a gateway to the organisation and security can be easily compromised if a device is lost. Solution providers are coming up with enhanced security and management features to help manufacturers over come this hurdle. One significant move in this direction is the subscription based managed mobility service being offered by the Verizon-Sybase team. It provides an integrated framework of management and security services delivered via a Web portal. More such services are sure to come as more manufacturers go mobile.
3. Factories are becoming networked, and that too wirelessly
Without a doubt, networking has been one of the best things to happen to industrial automation in the past decade. Without Ethernet and IP, interoperability would have been still a distant dream. Networking brought about what can be called the design-to-product continuum. It has enabled a lot of aspects of industrial automation ranging from integration to diagnostics.
Now networking has become even more powerful yet simple, thanks to wireless.
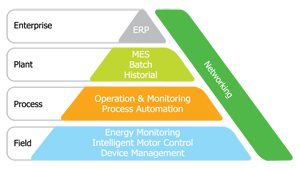
Wireless technologies make the communication setup within campuses quite easy and cost-effective. Initial installation and maintenance of wireless networks is comparatively inexpensive because one does not need to lay wires or replace them in the long run. Plus, adding new devices to a wireless network is also easy. Quite obviously, one can reach even difficult areas through wireless. This is especially useful in the case of sensor networks.
Perhaps one of the most important benefits of wireless networks is the reliability that is achieved by combining meshing with spread-spectrum technology. While doubts about security continue to nag manufacturers, the truth is that if done right, encryption, frequency differentiation, and techniques like direct-sequence spread-spectrum (DSSS) can surely ensure tight security for industrial wireless networks.
Several technologies such as Zig-Bee, ultra wideband (UWB), Wi-Fi, Bluetooth and WirelessHART are contending to rule the industrial automation space, while standards such as the ISA100 are attempting to streamline things.
Efforts are constantly on to make wireless the de-facto choice for industrial automation and to improve interoperability between various technologies. In May 2009, for example, the DASH7 Alliance was formed to create wireless technology that extends the ISO 18000-7 standard for low-power wireless data transfer. The group aims to im-prove interoperability between radio frequen-cy identification (RFID) devices and applica-tions, which will, in turn, improve tracking of materials and cargo in the supply chain. Soon, DASH7 will align itself with complementary technologies like cellular, passive RFID, WiFi, and 2-D barcode.
4. smart devices can talk to each other, and even make decisions
Almost all industrial automation equipment are becoming smart nowadays, acting as standalone units without any dependence on PCs. In a modern factory floor, a device can store a wealth of information such as when it was installed and by whom, uptime and downtime, critical specifications, diagnostics, availability of spares, replacement alternatives, repair instructions, usage patterns and more. With a wee bit of intelligence, it can also update this information to reflect otherwise invisible machine activity. Some advanced systems may include decision-making technologies such as operations research and artificial intelligence, which control work flow, material and information flow, etc.
Add to this the power of networking, and you have smart devices that can share information, instructions and decisions with other devices as well as organisation-wide information systems.
The ability of today’s machines to communicate with each other is called machine-to-machine (M2M) communication, and is one of the main benefits of wireless technology on the plant floor. M2M communication makes the information stored and generated by a machine more useful. It makes the information about assets, costs, liabilities and activities more visible to managers and to the decision-making process. The effect is an unprecedented level of productivity and efficiency.
“Increased intelligence of industrial automation and ‘smart’ inspection devices has led to systems which are more compact and cost-effective. This has also led to more flexible systems which can be reconfigured easily to quickly handle changing automation demands, reducing the total cost of ownership (TCO),” says Yashasvi Nathan, senior engineer-Marketing, Soliton Technologies.
“We can take an example of vision-based inspection systems to illustrate this. In conventional PC-based vision inspection systems, the images from a camera would be fed to a processor. The image processing would be carried out on this separate processing platform (a PC typically). This would lead to bulky inspection systems. With smart cameras, however, the processor and camera are integrated into a single, highly-compact package. This is a completely standalone inspection unit which does not require any external processor for running the inspection algorithm. This system can be set up with minimal disturbance to the existing equipment. The standalone nature of this system makes it a very useful product. These smart cameras come with network connectivity, enabling decision makers to get information online for quick and appropriate decision-making.”
Smart devices, pervasive computing and M2M communications are all set to change the role and scope of industrial automation, representing a huge business opportunity for industrial automation equipment suppliers. Their job will no longer be to supply mere machines. In order to tap a larger market, they will have to start looking at each machine as part of a larger system, and bundle the equipment with so-called smart services.
5. Integration gives more choice to customers
Networking, standards, convergence of communication technologies, powerful software platforms and open systems in industrial automation have made it possible to integrate different control disciplines into a single platform.
[stextbox id=”info”]several technologies such as ZigBee, ultra wideband (UWB), Wi-Fi, Bluetooth and WirelesshArT are contending to rule the industrial automation space, while standards such as the IsA100 are attempting to streamline things[/stextbox]
The possibility of combining things like PLCs, robots, computer numeric controllers (CNCs), human-machine interfaces (HMIs) and vision systems from different manufacturers onto a single platform allows users to exercise their judgement and choose just the right mix of control disciplines for every application. Plus, the user has the flexibility of upgrading, replacing or scaling up just some of the components at a time and not all. He can reorganise the devices to work in different ways. In such and many other ways, integration enables better asset management and flexibility as well.
Advanced software engineering has been one of the main enablers of such integration. Web services, data access specifications, service-oriented architecture, composite application frameworks, workflow engines and application integration have made information and control flow possible between industrial automation systems and other enterprise systems. At a very basic level, all these technologies enable disparate applications to share information and instructions with each other, by using a common standard/language that all of them can under-stand at the interface.
[stextbox id=”info”]Networking, standards, convergence of communication technologies, powerful software platforms and open systems in industrial automation have made it possible to integrate different control disciplines into a single platform[/stextbox]
This enables integration at various levels—machines can be strung together into a seamless workflow, the plant automation system can be fit into the entire product lifecycle, the product (from design to manufacture) can be integrated into the business, and the business itself can be linked to other businesses such as the suppliers’ and OEMs’!
The result: a real-time enterprise
A real-time enterprise is one that is equipped to act on events as they happen. It is not a new concept, but a melange of several old concepts such as just-in-time inventories, enterprise resource planning, supply chain management, customer relationship management and more.
It is about getting information in and out quickly, monitoring the business as it happens, and making quick, effective, agile decisions. In the past, there existed a gap between the factory and other information systems that always stood in the way of implementing truly real-time enterprises.
Today, industrial automation and its league of smart devices, mobile and wireless technologies, M2M communications, pervasive computing and powerful software engineering have removed this disconnect by making the factory an integral part of the en-tire enterprise. What’s more, beyond such integration, modern technologies have also made industrial automation systems accessible from anywhere using mobiles and PCs, literally encapsulating the whole enterprise into the employees’ hands!
The author is a technically-qualified freelance writer, editor and hands-on mom based in Bengaluru