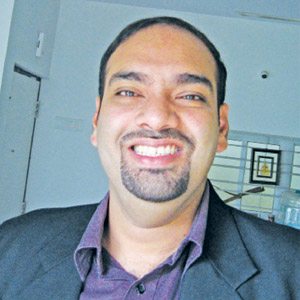
Q. What is the most exciting technology that your Indian research and development centre is working on?
A. TE Connectivity has research and development centres in India in addition to similar locations and labs across the world. In the last few years, we have developed some of the latest technologies in this space. Currently, some of our teams are working on fibre-based technology that will replace portions of copper-printed circuit boards.
Q. That sounds interesting. Could you share more details on the fibre-based technology?
A. For quite some time, while copper-based infrastructure solutions were still represented, there seemed to be a lot more flaunting of fibre from cabling and connectivity manufacturers than ever before. Today, both fibre and copper have major advances in bandwidth capability. To support the next generation of LANs at 10Gbps (gigabits per second), multi-mode fibre has advanced to new levels to support laser-based systems. Although the industry does have UTP/STP cabling that will provide at least a three-fold increase in bandwidth, it faces the limitation in distance compared to that of optical fibres media.
Q. What kind of applications are we talking about here?
A. Fibre-optic is the dominant type of cable for connecting separate buildings on campuses and connecting floor distributors to building distributors and data centres. Because of its high cost on the LAN equipment side, it has been limited to the backbones. If we compare the cost of a fibre port on the active equipment and that of gigabit copper port on the active equipment, the fibre is almost six times costlier.
Within DC segment, fibre-connected device ports already exceed copper-connected ports in every major global market, and within India the ratio is almost 54 per cent of fibre against 46 per cent of copper.
Some also predict that by 2014, over 85 per cent of the connections made in the data centres will be over fibre. Prime drivers are space, cost and power consumption, and for major content providers, video-on-demand services are driving an increase in the number of servers and the amount of disk storage. Reduced latency is the key to delivering the quality of service viewers seek.
Q. What are the challenges designers face to overcome while transitioning from copper to fibre?
A. It is a different game. While fibre opens up a world of very high-speed and almost unlimited bandwidth, the design of fibre devices, the management of thermal profiles and EMI-related issues at the transceivers and the delicate handling of fibre-optics can pose quite a challenge.
Q. So how would replacing fibre with copper help designers, if it is so challenging to begin with?
A. It is advantageous to use fibre connectivity over copper because it offers the product unmatched superior performance as far as bandwidth is concerned. Single-mode fibre has practically unlimited bandwidth. With the costs of copper shooting up, fibre connectivity solutions can sometimes be cheaper. With significant increase in volumes in the manufacture of fibre components, the prices of fibre transceivers installed in optical equipment have also dropped to very competitive levels.
Q. What are the challenges you face while designing and manufacturing products for connecting and protecting the flow of power, data and signal?
A. The flow of power and signals is defined by global standards. New challenges arise when these products are meant to operate in environments that are very different from the ones in which they were designed. For example, in an Indian environment, cable assemblies run high risk of damage from rodents and harsh UV radiation if used outdoors. This has required introducing new variants of our global product lines for the Indian market.
Q. Buying the most expensive passive components would not necessarily solve a problem. So how does a designer take a decision?
A. In times where design piracy is rampant, a designer must ensure to buy a genuine product. Also, it is important to buy products that are compliant to global standards and that are rigorously tested for reliability and longevity. It is safest to stick with reputed manufacturers who can furnish mean time between failures and third-party test reports. It is no longer sufficient to go just by description or look and feel of a product. Critical requirements need to be identified early and product compliance checked. Most reputed technologies conduct trainings on technologies that go into making these products. These can be invaluable to enable the designer to make and define the right specification before it goes to the commercial teams who may not have this exposure.