We hear a lot about the massive productivity increase that completely automated and connected factories can deliver over the existing setup. This talk by Dilin Anand of EFY with senior executives of Tata Technologies takes a look at the various elements that come into play when moving from a traditional factory to a futuristic connected factory.
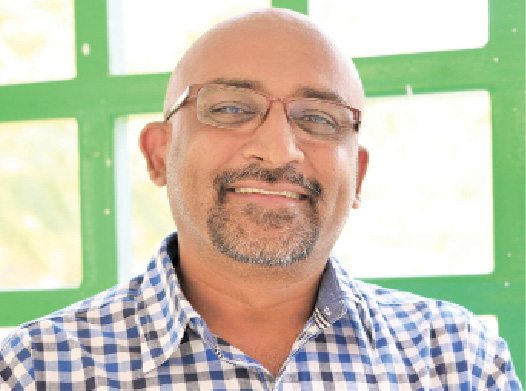
Q. While connected factories are obviously more efficient than non-connected factories, what reasons do you hear from companies that are hesitant to take the leap?
A. The quantum of change management in the journey towards connected factory operations is huge. Besides, you need to factor in other organisational show stoppers as well. Chief among them is the technophobia, the hang-ups about technology itself. Other considerations include the high costs involved, the wearisome task of integrating disparate blocks of technology into a seamless whole and, importantly, the very availability of these building blocks. The perceived fear about data security and cyber-attacks needs to be calmed.
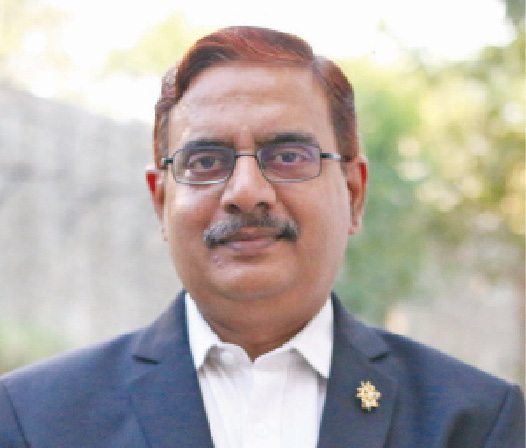
Q. Does the shift to a connected factory affect the classic production process used by various industries?
A. Realistically speaking, yes it does. Changes in technology, components and workflow are bound to affect the production process to an extent. On the other hand, the benefits are many. The shift to a connected factory will move some of the challenges. Like mobility, interoperability and capacity utilisation. In turn, it will lead to faster responses, quicker and more informed decisions, as well as bring about a change in overall operational style—from reactive to more proactive. Connected factory approach is not a facelift or something simply skin-deep, it’s a complete body lift.
Q. Since this shift leads to a lean manufacturing set up, how do people manage the tighter supply chain challenges that crop up?
A. In India, the challenge is not always about connecting the factory—there is a whole lot of logistics snarl-ups and there is a need for systems to face and deal with them. Kanban techniques for effective production scheduling and just in time systems, which ensure materials are delivered only as required, are already up and running. And a lot of Japanese firms that have popularised lean manufacturing, which pare out wasteful processes, are facilitating the shift to a connected factory environment.
Q. Any examples you can give of early-adopters of Industry 4.0?
A.Industry 4.0 is at a fairly nascent stage. As a coming-of-age concept, there are not many full-blown examples at the moment to support it. Even so, in this regard, Siemens’ Amberg facility in Germany merits some attention since it has gone quite some distance down the Industry 4.0 road. Amberg’s highly connected ecosystem turns out controls, automation products and components with an optimal turnaround time of 24 hours, and the quantum of confirmed defects is a mere 12 per million. The availability is reportedly around 99%. Plus, Amberg boasts a lot of automation and agility.
Q. What are your views on how the IoT paradigm will play out over the next 10-15 years?
A. It has a great potential from design and customer experience perspectives. Technology is shaping up with IPv6 communication rules setting the stage for the creation of unlimited number of IP addresses for billions of IoT devices on the network. 5G mobile networks, likely to go operational by 2020, are not only faster than 4G but also support large-scale sensor deployment. This could be an inflexion point for IoT as also cloud computing. However, the industry needs to be ready with all requisite standards around security and handshaking. There isn’t much time left either; standards must be in place in the next 1-2 years. In the next 3-5 years, when all the pieces of this jigsaw are in place, we are going to see the connected enterprise at its peak.
Do you like this interview? You may also like other interviews: click here