At MathWorks’ second annual India user conference in Bengaluru, customers and technical experts discussed the capabilities of MATLAB and Simulink for design, modeling and simulation.
Jalaja Ramanunni of Electronics For You had a chance to speak to Steve Miller, technical marketing manager, physical modeling, MathWorks, who explained how physical modeling capabilities enable automotive engineers to identify and fix problems early in design, rather than late in development when testing the final hardware
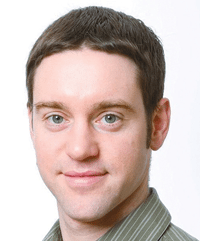
JULY 2012: What’s the role of simulation in automotive?
Traditionally, when people develop systems, they use hardware. That means if you build a prototype, test it, and find that it does not work, you’ll have to start all over again—build a new prototype and iterate on the design that way. This can be a long process. Engineers can now use simulation to make designs virtually before committing to hardware and prototyping.
Hardware prototyping has been used for a very long time. The first design starts with a prototype, and eventually, the designer comes up with a car that he is willing to sell. But this process takes a very long time—to come up with an idea, build it, test the hardware, iterate the idea and so on.
By using computers for modeling and simulation, designers can perform iterations faster. So feedback such as “The engine that took you two months to build requires changes. Make it ten percent smaller and we will see if it works for us” is painful to hear if you are developing using hardware prototypes. However, using a computer model, it takes much less time to make such large changes.
What are the challenges in automotive development? How does modeling and simulation help to address these?
One of the benefits of model-based design is that from the initial stages, you can create a model of the system in the computer and test and verify all the requirements. By the time you build the first piece of hardware, say, the first car engine, you would have already discovered a lot of problems you typically find at a later stage when it is much more expensive to fix them.
When automotive companies develop a car, they focus on many aspects, cost-efficiency being one of the key areas. Getting to the market soon is also one of their focus areas. Since they are not the only company building cars, they would want to build a car as quickly as possible and release it in the market. Sometimes, it takes over six years to come up with a product. This is a risky situation for an automotive company as others might beat it.
Once an automotive company comes up with an idea, it should execute that idea immediately. If you can shorten the development process, you can save a considerable amount of money by building fewer prototypes and reducing costs in the development process.
A hand-built prototype can cost millions of dollars. In the first prototype, we often see that the manufacturing process is not yet in place and that the prototype can get insanely expensive. The more the engineer can do in a virtual environment, the less it will cost to develop the idea to a point where it can be put to production.
Engineers can use modeling and simulation to make sure that yours is not just another design, but one that is optimised well. When designing a vehicle, maximising the speed and the load it can carry is a basic, rough requirement, and there are a lot of designs that will meet it. If you put an engine of a certain size or bigger you will meet the speed requirement, and if the control system of the car is set up properly the car will still remain stable in spite of the number of people in the car. However, you would not want to go overboard with the design and make it so expensive that you do not have customers. Modeling and simulation can help you ensure that your design has met all the requirements without a heavy price tag. There are so many components working behind the scenes.
What’s the key to the best possible overall performance?
Modeling and simulation helps in designing a perfect combination of subsystems. For instance, when developing an electric or hybrid electric vehicle, there are a number of systems like the motor, generator, battery and engine, all of which have their own separate requirements. Simulation can help to decipher information such as how big the motor and battery should be. If the engineers want to shrink the battery by ten per cent, they can check whether they can increase the motor’s size by that amount. The final design does not use the perfect motor or the perfect battery, but it is the perfect combination of the subsystems. The combination is optimised and helps the manufacturer in achieving his goals by meeting the needs of buyers and producing it as quickly and as cheaply as possible.