People often talk about how advanced robotics can make factories and distribution centres more efficient. Vaidya Subramaniam S., head – product management, GreyOrange, talks about the effort that goes into designing these robots, through GreyOrange’s experience in designing their own IIoT products—Butler and Sorter, in a conversation with Dilin Anand from EFY
Q. Tell us about the communication technologies used in Butler?
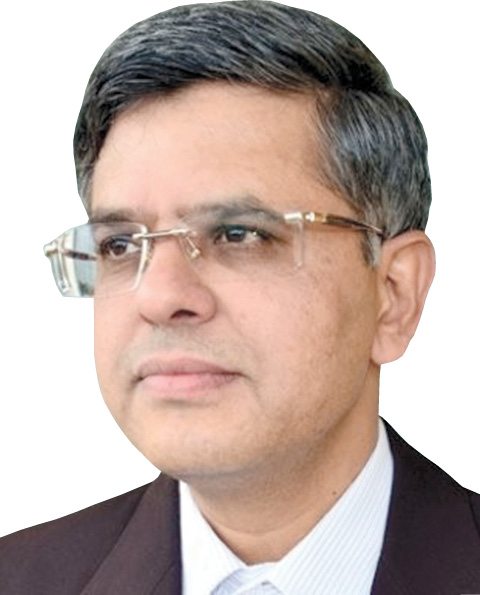
A. Butler possesses a variety of communication technologies, with sensing and security technologies at its core. The robot not only moves around in the warehouse based on programmed logic but also communicates continuously with the control unit. Butler uses two wireless technologies for communication, Wi-Fi and ZigBee, to address the unique needs of low-cost, low-power wireless M2M networks.
Q. How do you ensure Butler moves about without hindrances?
A. The sensing technology involves image processors and barcode scanners that communicate with control systems and respond automatically. For example, Butler can effectively move around at a speed of 5km/hour on a path fed into it through an algorithm. It can scan barcodes and place racks at the right place using its sensing technologies. However, if there is an obstruction in Butler’s path, it immediately stops.
Butler charges through a smart charger, and assesses the current charging level and optimises battery consumption. It utilises the central control system to monitor charging levels.
Q. What is special about the way Butler moves?
A. Butler moves in a grid. It operates in a way so that the speed is optimum. Following this grid avoids any obstruction and mismanagement.
Dynamic path planning is another feature that allows Butler to quickly adapt itself to the environment and change its functioning according to the changing needs. An operator will not need to wait or sit idle, since Butler moves quickly and effectively from point A to point B.
Q. Are there any analytical features that Butler uses in its movement?
A. Butler picks and puts the racks at the best spot so that inventory can be accurately traced and tracked. It leaves no chance for error in inventory management. The robot is artificially intelligent and has machine learning capabilities. This means that it can understand demand patterns. It places the racks with high-demand products near the operator workstation and low-demand products at the back. Therefore warehouse space and inventory turnaround time is optimised.
Q. Any hardware design challenges faced while creating Sorter?
A. Sorter has moving conveyers and arms. The most important challenge was to ensure prolonged life of these parts as there is a risk of wear and tear. We had to integrate a lot of functions in Sorter. Operators need to have a real-time view of the number of products that are placed over the belt, the ones that are sorted and the errors that need to be fixed in a stipulated period of time. So selection of drivers had to be such that it could support this process and let operators function effectively.
Q. Any peculiar challenges that you faced with Sorter?
A. At the lowest speed, Sorter sorts 3000 packets per hour to a maximum of 15,000 packets per hour. The product needs to be robust enough to handle such high speed. India being a huge and diverse country makes it a challenge to sort products on the basis of the number of destinations, cities, pin codes, etc. If delivery has to be made to 125 destinations, Sorter cannot have 125 arms to sort packets. So we divided sorting into primary and secondary.
Q. What hardware design challenges did you face while creating these robots in India?
A. One challenge was to make sure that we could manufacture on a large scale. For manufacturing, getting the right kind of quality on a sustained basis is vital. So we set up in-house quality-control teams that inspect the quality of products.
Additionally, effective implementation of products at the customer site was extremely critical. The product needed to be engineered in a way that could ensure easy installation. Thus, a functional layout was made through Design for Manufacturing and Assembling process.
For reading the full interview: Click here