Ever since I was a student some laws of physics always fascinated me. Something about the Bernoulli’s Law, or the Capillary action seemed interesting. This might have been some time back, when we didn’t have appropriate tools to make the study of such laws interesting. But today we certainly do. Valerio Marra, marketing director, COMSOL, Burlington Massachusetts, takes us through how they make the understanding of complex laws of physics fascinating through simulation.
Q. What are the considerations for development of physics based software?
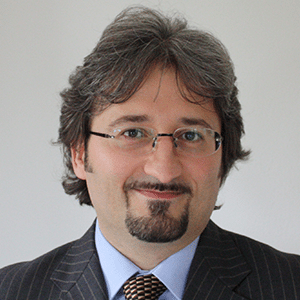
A. Several laws of physics are needed to accurately represent our complex world. The mathematical models are based on the principles of physics. All the details relevant to the simulation at hand are included and coupled correctly. The goal is to provide the user with simulation results using a reasonable amount of computational resources. These can be used to model gears as well as to easily set-up power transmission and automotive simulations by taking into account all these phenomena.
Q. How do you design a system?
A. The next step is to convert the model into difference equations, which we have to solve using the correct solvers. The goal is to provide the user with simulation results using a reasonable amount of computational resources, such as computer memory, and solution time. We also need to control the desired solution accuracy. The user might be varying several parameters and a quick solution process is in order to select a few designs from the many possibilities so that more time can be spent in terms of accuracy and optimization. Software quality control procedures should be in place.
Q. How to improve precision in simulation?
A. Improving the accuracy of a simulation depends on several factors. The available computational resources have an impact on the simulation. It allows the user in solving their model using fine discretization, both in terms of mesh type and size, element order and shape function. It is recommended to perform a convergence study where the problem is solved increasing the discretization until the solution doesn’t change, which means that the model used was allowed to capture the phenomena it described.
Q. What are the major areas that benefit from physics simulation?
A. The adoption of numerical simulation at an early stage to optimize their design is really beneficial for a design team. It is more efficiently and effectively reduces the number of physical prototypes, resulting in a shorter time to market. The multi-physics approach reports similarly while working on electrical, mechanical, acoustic, fluid, heat, and chemical designs. Also physical testing cannot reveal certain information because measurements are dangerous or impossible to take. Such scenarios include products that operate in space, harsh environments, or at very large or small scales.
Q. How are the usage options with multiphysics?
A. Simulation tools promoting collaboration across departments have a significant impact on design teams and their workflow. Different departments need to test the effect of a new product requirement before initiating a design iteration. It unloads the design team from repetitive tasks performed on previously validated numerical models. Design engineers could let their colleagues run an app and perform analysis on their own. The app user doesn’t need to be an expert in software or physics. They can directly benefit from the simulation through a user-friendly interface.
Q. What are the challenges involved with gear simulation?
A. Gears, commonly used to change the speed, torque, or direction of rotation, pose many design challenges. They transfer rotation from one shaft to another leads to twisting and torsional vibrations. These get transferred to other components of the system, such as bearings and housings. This in turn manifests as noise in the surroundings. It is necessary to include non-linearity such as the flexibility of shafts and bearings, as well as that of the gear mesh, as well as transmission error, backlash, and friction.