It took several years for device packaging technology to advance to the point where half watt LEDs could become commercially available. Companies such as Philips and General Electric spearheaded these developments, resulting in the eventual availability of watt-class white LEDs. Once these devices became available, systems designers set thinking about designing lighting systems that could take advantage of the many benefits offered by LED-based luminaires.
A radical departure from conventional means of generating light, LEDs have features that make them especially suited for lighting applications. Their small size, extreme efficiency in converting electrical energy to light, availability in many colours (including white) and absence of any environmentally harmful substance that might pose a problem during disposal make them ideal as light sources for any conceivable application. Little wonder then that LED-containing lighting systems are finding increasing acceptance all over the world. The market for LEDs and solid-state lighting systems has been growing at close to 25% per annum for the past several years and by all indications will continue to do so for the foreseeable future.
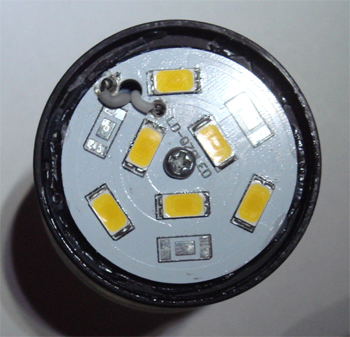
The first luminaires to be designed with high power white LEDs were shaped to resemble traditional tungsten filament light bulbs. These so-called retrofit bulbs have standard screw or bayonet bases to fit in existing lamp sockets. The argument was that this was the quickest way to market for LED lamp makers as it required no modification of existing lighting infrastructure. In spite of their significantly higher cost, the sales of retrofit LED light bulbs have been rising over the past five years. Manufacturers cite their very long lifetimes as the feature that offsets their purchase price – a typical LED light bulb can last for 10,000 to 20,000 hours before needing replacement. Compare this with the typical 800 hours lifetime of a tungsten incandescent bulb and the higher cost of an LED bulb doesn’t seem too onerous. The increased cost of these bulbs results from the need to incorporate a complete power supply inside every bulb, as LEDs only operate with low voltage DC power. The power supply is also the most vulnerable part of any LED bulb because the failure of any of its components can render the bulb useless. The actual LEDs themselves are much less prone to failure and are the reason manufacturers are able to quote such ambitious figures for their products. Figure 3 shows the interior of an 8 watt bulb containing 6 surface mount power LEDs. With prolonged use, LEDs tend to grow dimmer and a bulb’s useful life is considered over once its LEDs drop to half of their initial brightness. The fall in brightness is caused by a slow degradation of the LED chip and the colour conversion phosphor. The fact that LED bulbs do not fail abruptly like incandescent bulbs also reduces chances of untoward accidents.
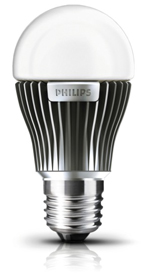
In addition to a miniature switch-mode power supply, retrofit bulbs also incorporate a good heat sink to dissipate heat generated by the LEDs. Keeping the LEDs cool during operation with good thermal management can vastly increase their useful lifetime. This heat sink is usually a prominent feature of any LED bulb and designers try to make it as aesthetically appealing as possible (see figure 4). Over the years, manufacturers have been freely experimenting with the form factor of LED bulbs and this shows up in the many shapes and sizes now available on supermarket counters.
During the first few years after the appearance of LED light bulbs their consumer acceptance was mainly limited by the inferior quality of their light output. To many users their light appeared too cold and markedly different from that given off by incandescent lamps. This remained an issue for several years until LED manufacturers developed better LED phosphors. These luminescent materials consist of a crystalline host, such as an oxide, sulphide or nitride, doped with one or more transition metal or rare-earth element. Typical dopants include manganese, copper, cerium and europium. A typical widely used phosphor is cerium-doped yttrium aluminium garnet (Ce:YAG). Phosphors are inert organic materials and thus present no dangers to their use in LEDs.