Development of integrated flexible electronics is important for the construction of advanced wearable devices. And when you consider our fascination with wearables, demand for newer materials to design such wearables also rises. Such developments in the fields of material technology are happening all around us. Ranging from energy generation to lighting, we have some fascinating materials being tested out in labs. 3D printing materials and organic light emitting diodes (OLEDs) are also among areas of research.
Carbon based materials, for example, are being used to improve efficiency. Perovskites are one such wide-ranging class of materials consisting of organic molecules. These are made mostly of carbon and hydrogen, bonded with a metal and a halogen, in a three-dimensional crystal lattice. These can be made much more economically compared to conventional materials and with fewer emissions.
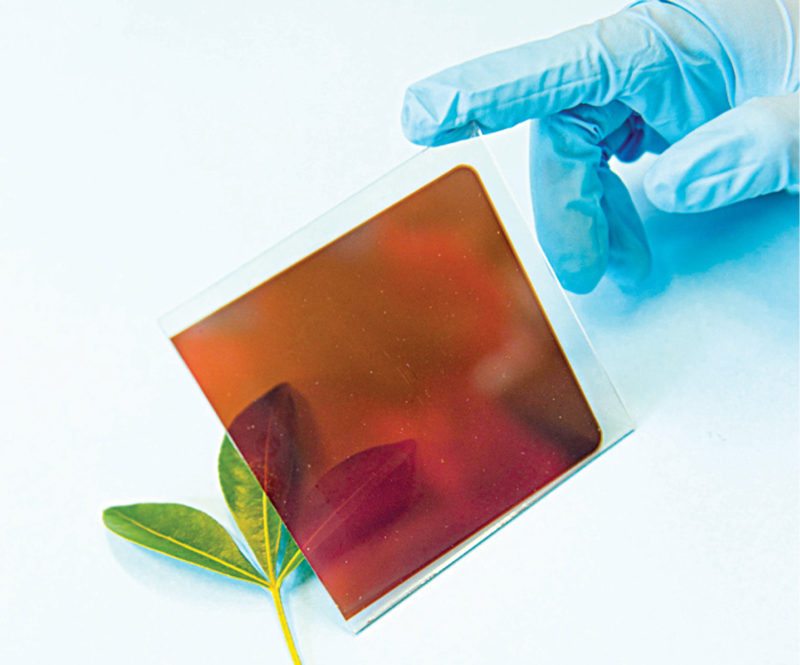
Solar researches in perovskites
Perovskite based solar cells consist of a transparent conductive oxide-coated glass substrate. With a top encapsulation, these have an evaporated metal cathode providing high-performance solutions.
On the other hand, use of lead makes these not so safe for use. An alternative is to use tin based perovskites, which are non-poisonous. However, current power-conversion efficiency of tin based devices is significantly lower than of lead based devices. Nevertheless, if their development history is any indication, we can look forward to some non-poisonous solar cells with higher efficiency.
A mix of organic and inorganic ions with crystal structures similar to calcium-titanium-oxide (CaTiO3) results in hybrids. Perovskites containing halide ions such as fluoride or chlorine are a sub-set of such hybrids. For converting sunlight to electricity, however, iodide variants are a much better option. Materials such as methylammonium-lead-iodide (CH3NH3PbI3) can convert sunlight to electricity. These have enabled urban poor communities in India to access off-grid electricity. After all, there is only so much coal and hydropower can do.
Oxford Photovoltaics, UK, has begun commercialising thin-film perovskite solar cells. These are directly printed on silicon solar cells, copper-indium-gallium-selenide (CIGS) solar cells or glass. It is one of the three mainstream thin-film technologies—the other two being cadmium-telluride and amorphous-silicon, with a lab-efficiency above 20 per cent.
Making inexpensive solar panels
Solar energy harvesting is an area that shows a lot of promise in renewable energy. The present panels employ silicon solar cells, which are highly efficient, converting up to 21.5 per cent of sunlight that falls on these into electricity, and are very durable.
However, processing silicon wafers is very expensive. Add to that the required thickness of 0.3mm in order to absorb maximum sunlight, the prices just go through the roof.
Thin-film solar cells, often dubbed as the next generation of solar technology, are another option over older silicon models. These are made by layering a thin solar absorbent material over a substrate such as glass or plastic, which can be flexible. The materials being used in the present thin films are, however, a concern. Cadmium in cadmium-telluride (CdTe) is highly toxic, making handling and placement of solar cells a major concern.
The poisonous potential
Solar, an American photovoltaic manufacturer of rigid thin-film modules, has announced an efficiency of 22.1 per cent using experimental cells made from CdTe. It is a thin-film technology, requiring less material to produce a comparable amount of electricity than conventional silicon technology. It is also poisonous to humans. The poisonous material has proven to be highly efficient; in labs, at least. So it would be a boon if we could work around these materials.
Manufacturing process for CdTe solar cells is also simpler, resulting in lower costs for electricity production—purely theoretical, of course. Trade-offs seem to be pretty high there.
Some low-cost solutions
Tara Dhakal, interim director, Centre for Autonomous Solar Power, and assistant professor, department of electrical and computer engineering, Binghamton University, UK, is working with pyrite and copper-zinc-tin-sulfide (CZTS) as these are non-toxic and available in abundance. He has explained the details in a paper earlier this year. The paper reads, “CZTS costs about 0.005 cents per watt, and pyrite costs a mere 0.000002 cents per watt.” The biggest advantage is that, thickness of these chips can go as low as a thousandth of a millimetre.
In a study earlier this year, researchers at Stanford University, USA, and University of California at Berkeley, USA, estimated that, by 2050, 45 per cent of electricity in America could be dependent on solar energy. Fool’s gold seems to be taking over liquid gold, at least in the western hemisphere.
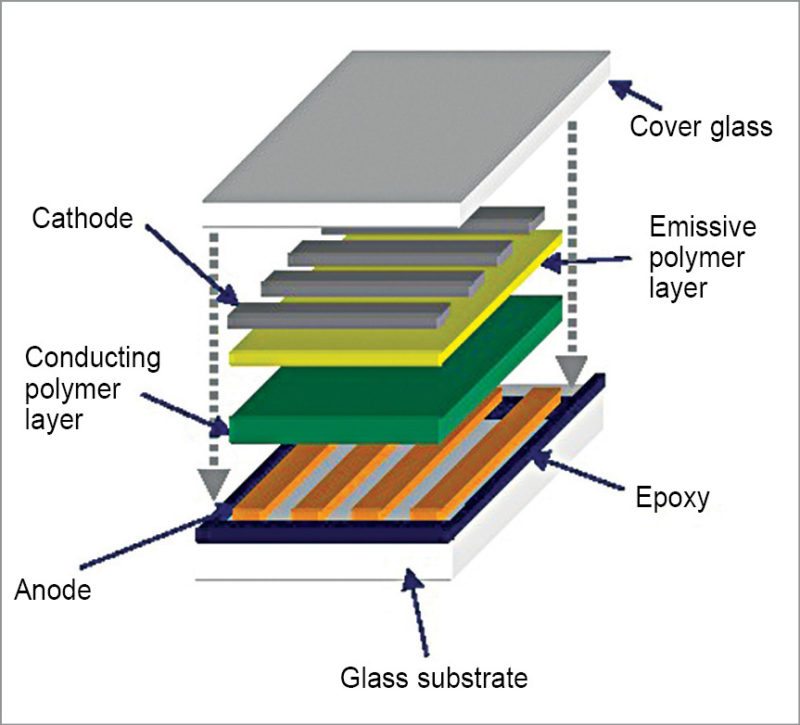
Organics in lighting
Organics are coming in use in lighting as well. Moving on from regular LEDs, we now have OLEDs with high luminescence. Some of the best displays in 2016 have been various variants of OLEDs. AMOLED and super-AMOLED are premium lighting devices with amazing clarity. The story behind OLED, however, deals with a lot of chemistry.
Pyrimidine is an aromatic heterocyclic organic compound similar to pyridine that is marking significant changes in OLEDs. Pyrimidine-containing thermally-activated delayed-fluorescence (TADF) emitters are being used to bring out improvements in efficiency. OLEDs based on blue pyrimidine based TADF emitters have exhibited high external quantum efficiency of 20.8 per cent and power efficiencies of 31.5lm/W.
Researchers from National TsingHua University, Taiwan, are working with two benzoylpyridine-carbazole based fluorescent materials, DCBPy and DTCBPy. These molecules have shown smaller ΔEST of 0.03 and 0.04eV and transient photoluminescence (PL) characteristics. These properties relate to TADF materials. These are also photoluminescent, with quantum yields of 14 to 36 per cent in cyclohexane. Values rise rapidly from 88 to 91.4 per cent in thinner-film variants. OLEDs using DCBPy and DTCBPy for doping emit blue and green lights, creating a possible solution for a stable blue light source in OLEDs.
With proper application, you might very well be living in Tony Stark’s mansion with windows working as screens to display notifications or other tasks!
3D printing for fun
Polylactic acid (PLA) is a popular biodegradable thermoplastic derived from renewable resources. It is also more environmentally friendly among other plastic materials. PLA is harder than acrylonitrile-butadiene-styrene (ABS) and melts at 180°C to 220°C. The most popular thermoplastic, however, is ABS. It is very durable, slightly flexible and lightweight, and can be easily extruded.
However, the catch with ABS is the higher temperature requirement of about 210°C to 250°C. Nylon 618 and 645 are also in the running due to their ease of use and lower temperatures to work with. Designed to simulate ABS plastic, tough resin from Formlabs provides comparable tensile strength and modulus required for functional prototyping.
Aesthetically-pleasing applications
Thermoplastic elastomers (TPEs) like ninjaflex and filaflex provide options for flexible 3D printing. However, printed cells have shown to be vulnerable to moisture, which could lead to contamination if a cell was to become brittle and break.
3D printing metals is also gaining popularity over the past couple of years. Gold and silver have been added to the range of metal materials that can be 3D-printed directly, with applications across the jewellery sector. These are both very strong materials and are processed in powder form. With less than 0.1 per cent residual ash after burnout, Wax Cast from Makerjuice Labs is a relatively-new resin being used by jewellery makers. Optimised for 25µm to 50µm layers, it is resistant to most solvents including alcohol and acetone.
Another material being tested out is aluminium. 3D-printed aluminium is known to be great for producing strong, light and precise end-use metal parts. Post printing, the parts looks more matte and feature rougher surfaces than traditionally-milled aluminium. Applications of such materials include functional parts, spare parts and jewellery.
Ceramics is a relatively newer group of materials that is being 3D-printed with various levels of success. However, ceramic parts have to undergo firing and glazing processes just like any other ceramic material after designing.
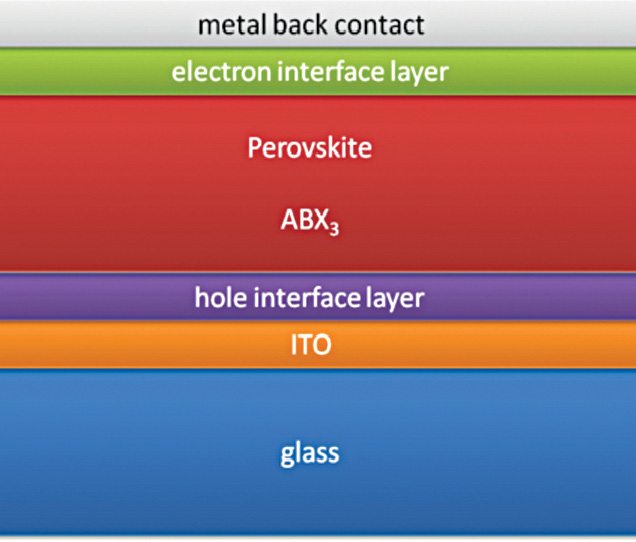
A futuristic vision
An area of development with the current systems is the increase in efficiency. Theoretical efficiency with CdTe ranges at about 30 per cent, which, in commercial implementation, drops to 16 to 20 per cent.
Perovskites have been very efficient and fast developing. Higher efficiency from these materials would eventually allow you to go for reasonable-sized solar panels. One day, maybe, your smartwatch would be made of OLED for display, which could be 3D-printed and solar-charged. Yeah, wishful thinking does make the future look nice!
Materials with increased efficiencies could very well usher in an era of dependence on renewable sources of energy for solar cells or OLEDs for lighting and display.
e-Textiles is an area of promise with OLEDs and solar cells. You never know, two years down the line a smartphone might be obsolete and we could have an advanced suit that can process and advise based on the data around us. Certainly, a big help for the differently-abled!
Saurabh Durgapal is working as technology journalist at EFY