Tru-Vu uses optical bonding to improve daylight viewing on their LCDs. Optical bonding injects a transparent optical-grade epoxy resin to bond a protective glass panel directly to the face of the LCD. This eliminates the air gap between the LCD and the cover glass, drastically reducing the reflections which cause the visual wash-out typically seen in bright conditions. Optical bonding also increases the durability of the LCD monitor by bonding the LCD panel to the cover glass and the monitor’s enclosure. It also avoids fogging due to moisture trapped between the layers.
Eco angles—power, heat, greenness
Users want to use their mobile devices for longer hours on a single charge. So it is critical that these devices consume less power. For larger displays, it is a matter of reducing electricity bills. Hence companies are coming up with several innovative technologies to reduce the power consumed.
For example, this November, Japan Display showcased a reflective LCD panel with power consumption as low as 3 mW at the time of displaying a still image. The panel has a 17.8cm screen and is targeted at mobile devices that require low power consumption.
Japan Display has used a low-temperature polycrystalline silicon TFT as the driver element. It has also included a static RAM circuit on each pixel to retain image data to be written, with the aim of lowering power consumption. Another distinctive aspect of this display is that the company has achieved a natural display like paper by optimising the optical design of the scattering layer.
Materials engineering is also contributing a lot to making cooler and power-efficient displays. An organic LED display, for example, if designed properly uses only 40 per cent of the power of a comparable LCD. Nano-technology has also given rise to better structures, materials and technologies. Cambridge University’s polymer organic light-emitting diode (P-OLED) display is an example, which is extremely eco-friendly and power-efficient. POLEDs are basically OLEDs made with conjugated polymers.
The heat dissipated by the display is also a critical factor. If a display heats up, its basic components wear out faster and the life of the display goes down. If a lot of heat emanates from the display, it will also affect the surrounding parts of the device—this is very critical for mobile devices where the components are packed closely together. A hot device is also difficult to hold in your hand. So this is another point of innovation for display-makers.
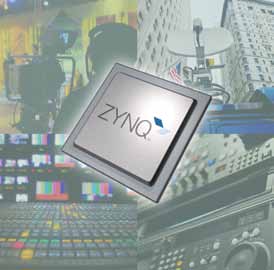
Greenness is a universal parameter that almost all industries are focusing on. The eco-friendliness of products is a very important factor as it influences product ratings, customer decisions and the manufacturer’s social responsibility in general. At GITEX 2012, Panasonic was apparently the largest exhibitor and its focus was on eco-friendly products. The company claims that its displays are free of lead, mercury and other toxic substances that can harm the environment.
Little chips, big wonders
It is possible for display makers to quickly design and manufacture products with a range of readily-available intellectual property and programmable components.
The field-programmable gate arrays (FPGAs) available from companies like Xilinx and Altera enable faster adoption and migration to the latest technology and standards, interfaces and codecs due to their programmability and flexibility. This allows manufacturers to evolve from 3D TV to Digital Cinema (4K2K) and ultimately to 8K4K Ultra HDTV (such as what was used in theatres in London to broadcast the Olympics footage this year).
“Emerging display technology is an area where FPGAs are always needed, given the newness of the technology. There has been a tremendous amount of innovation and breakthrough in semiconductor and IC technology relative to bringing immersive display technologies such as 3D TV, LED local dimming and 4K2K (Quad HD) to life,” says Aaron Behman, senior product marketing manager-Broadcast & Consumer Segment Marketing, Xilinx Inc.
He adds, “The precipitation of mobile devices putting constraints on video production and the reach of video networks (to fuel mobile-based insatiable video demands and the like) put the spotlight on FPGAs, which are increasingly the only option to meet the demands of an ever-changing broadcast industry. A growing number of OEMs are adopting these flexible devices because hard-cast silicon solutions like application-specific integrated circuits (ASICs) and application-specific standard products (ASSPs) geared for implementing system integration and video processing, are too expensive and take too long to develop in an era of rapid standards evolution. The combination of programmable devices, market-specific intellectual property, reference designs and hardware boards fosters broad-cast design innovation and algorithm enhancements that deliver real-time capabilities of HD and higher resolutions of Digital Cinema and 4K2K.”