Flexible electronics is lightweight, rugged, bendable, roll-able, portable and potentially foldable. Ever-evolving advances in thin-film materials and devices have fuelled many of the developments in the field of flexible electronics. These advances have been complemented with the development of new integration processes, enabling wafer-scale processes to be combined with flexible substrates.
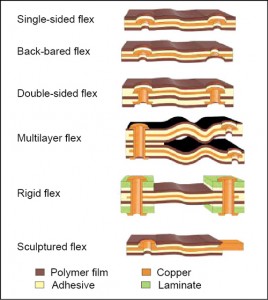
Diodes and transistors are two of the most common active thin-film devices used in digital and analogue circuits. While they have been successfully used in flexible platforms, their performance and applicability is limited by requirement of exotic device architectures and novel materials. In order to achieve the goal of full-system integration in next-generation flexible systems, a paradigm shift in design and fabrication is necessary.
There are many potential applications of flexible electronics in healthcare, automotive, human–machine interfaces, mobile communications and computing platforms, and embedded systems in both living and hostile environments. Besides, there are market-specific applications, such as human-machine interactivity, energy storage and generation, mobile communications and networking, touching the application of flexible electronics on ubiquitous computing platforms throughout.
Flexibility in electronic materials is very attractive for medical and bioengineering. Living organisms are intrinsically flexible and malleable. Thus, flexibility is a necessity for successful integration of electronics in biological systems. Further, in order to carry out daily tasks, flexibility is less likely to hinder over stiffness.
Materials
The fundamental properties of thin-film materials, as well as the quality of various device interfaces, give rise to inherent limitations in device performance. Each element of the flex circuit must be able to consistently meet the demands placed upon it for the life of the product. In addition, the material must work reliably in concert with the other elements of the circuit to assure ease of manufacture and reliability.

The materials and technologies behind flexible substrates are an important consideration for flexible electronics. Perhaps two of the main flexible substrate candidates are plastic and stainless steel. Although stainless steel is incompatible with standard deposition temperatures, it results in a substantially heavier system due to its higher mass density—a critical consideration for portable flexible technologies. Also, stainless steel is not particularly deformable, and is thus unsuitable, in particular, for wearable electronics. Plastic substrates are lighter and deformable alternatives.
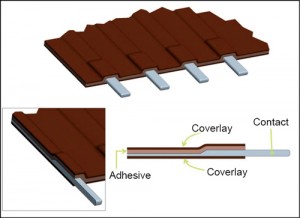
Substrates need to be solvent-resistant, so that standard optical photolithography process can be used. Additional substrate requirements include low cost (allowing large area, mass production) and moisture resistance. Table I compares some of the more critical properties of some key plastic substrates.
One of the main challenges facing plastic as a next-generation substrate is the substantially reduced processing temperature window. The maximum fabrication temperature is related to the glass-transition temperature above which inelastic deformation takes place and the substrate no longer retains its original dimension, which is essential for photolithography. As an example, polyethylene naphthalate (PEN) satisfies all requirements and tolerates temperatures as high as 160oC.
More recently, a number of electronic devices and circuits have been demonstrated, utilising paper as a substrate and/or as a gate dielectric. Such approaches lead to electronic devices with the potential for en masse integration at low cost, which are also disposable and fully recyclable.
Base material
A polymer film provides the foundation as a base material for flexible electronics. Under normal circumstances, the flex circuit base material provides most primary physical and electrical properties of the flexible circuit. In the case of adhesive-less circuit constructions, the base material provides all of the characteristic properties.
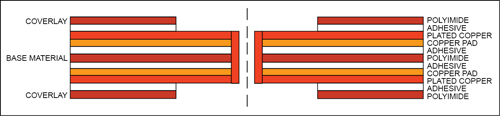
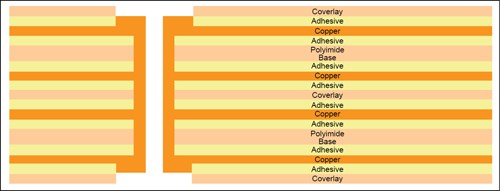
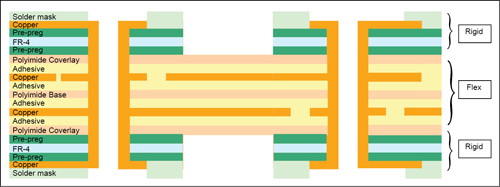
While a wide range of thickness is possible, most flexible films are provided in a narrow range of relatively thin dimensions from 12µm to 125µm (1/2 mil to 5 mils). But thinner and thicker materials are possible. Thinner materials are, of course, more flexible. For most materials, stiffness increase is proportional to the cube of thickness. This means that, if the thickness is doubled, the material becomes eight times stiffer and will only deflect 1/8 as much under the same load.
There are a number of materials used as base films, including polyester (PET), polyimide (PI), polyethylene naphthalene (PEN) and polyetherimide (PEI). These, along with various fluropolymers (FEPs) and copolymers polyimide films, are most prevalent owing to their advantageous electrical, mechanical, chemical and thermal properties.