Bonding adhesive
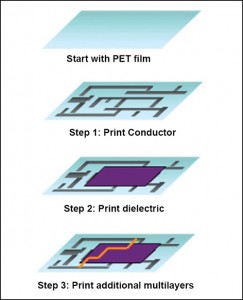
Adhesives are used as the bonding medium for creating a laminate. When it comes to temperature resistance, the adhesive is also typically a performance-limiting element of a laminate, especially when polyimide is the base material. Because of the earlier difficulties associated with polyimide adhesives, many polyimide flex circuits presently employ adhesive systems of different polymer families. However, some newer thermoplastic polyimide adhesives are making important in-roads.
As with the base films, adhesives come in different thicknesses. Thickness selection is typically a function of the application.
Metal foil
A metal foil is most commonly used as the conductive element of a flexible laminate. A metal foil is the material from which the circuit paths are normally etched. Copper’s excellent balance of cost and physical and electrical performance attributes make it an excellent choice.
There are actually many different types of copper foil. In certain non-standard cases, the circuit manufacturer may be called upon to create a specialty laminate by using a specified alternative metal foil, such as a special copper alloy or other metal foil in the construction.
Types of flexible circuits
There are a few basic constructions of flexible circuits, but there is significant variation between the different types in terms of their construction. Following is a review of the most common types of flexible circuit constructions. Flexible circuits have a rich history and are extremely diverse in their nature. This diversity opens them to use in a wide range of applications, with new applications being developed on a regular basis.
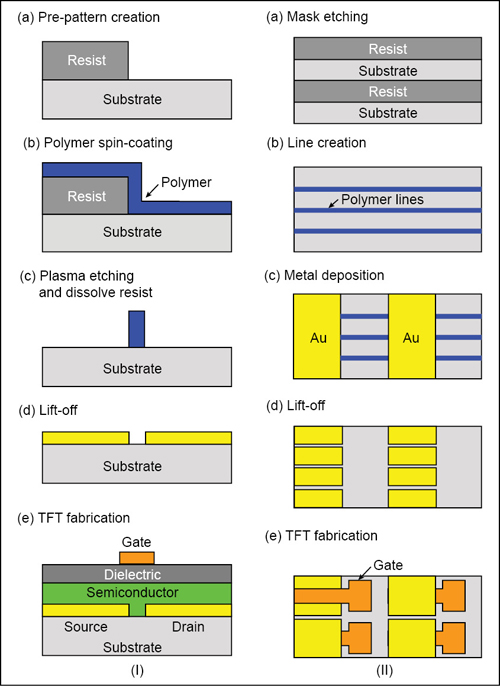
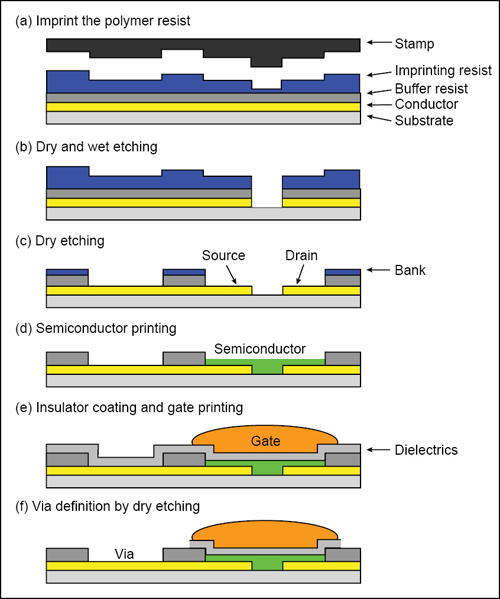
It is hard to predict where the technology will go next. However, roll-to-roll processing is likely to play an important part. Flexible electronics opens the door to foldaway smartphone displays, solar cells on a roll of plastic and advanced medical devices—if we can figure out how to make them.
Single-sided flex circuits
A single-layer flex circuit is the most basic and consists of a flexible polyimide film laminated to a thin sheet of copper. The copper layer is then chemically etched to produce a circuit pattern specific to your design requirements. A polyimide cover lay is then added for insulation and environmental protection of the circuit.
A single-sided flex is used for:
1. Dynamic flexing applications
2. Unusual folding and forming applications
3. Installation/service applications/repair
4. When there are limitations on space/thickness
Some important features of single-sided flex are:
1. Very thin construction, under 0.1mm-0.2mm (0.004-0.008 inch)
2. One conductor layer
3. Reverse-bared or back-bared pads
4. Supported and unsupported finger areas
Back-bared flex circuits
Double access flex, also known as back-bared flex, are flexible circuits having a single conductor layer but they allow access to selected features of the conductor pattern from both sides. While this type of circuit has certain benefits, the specialised processing requirements for accessing the features limit its use.
A dual-access flex circuit is simply a single-sided flex circuit that is manufactured such that its conductive material can be accessed from both sides of the circuit. Flexible Circuit is a front runner in this technology, which utilises specialised lasers and processing to skive open the polyimide layer of the base material to allow dual access to the single copper layer. While this type of circuit has certain benefits, the specialised processing requirements for accessing the features limit its use.
These flex circuits find application in such fields as:
1. Medical
2. Environmental
3. Test and Measurement
4. Automotive and other general electronic devices
Sculptured flex circuits
Sculptured flex circuits are a novel subset of normal flexible circuit structures. Their manufacturing process involves a special flex circuit multi-step etching method to produce a flexible circuit having finished copper conductors whose thickness differs at various places along their length. The conductors are generally thin in flexible areas and thick at interconnection points.
Sculptured circuit technology enables the thickness of the copper conductors to vary at any point on the circuit. In addition, selective application of the supporting dielectric enables integral exposed fingers to be produced. All holes are etched, providing the flexibility to create precisely-located apertures of any shape or size at any position on the circuit.