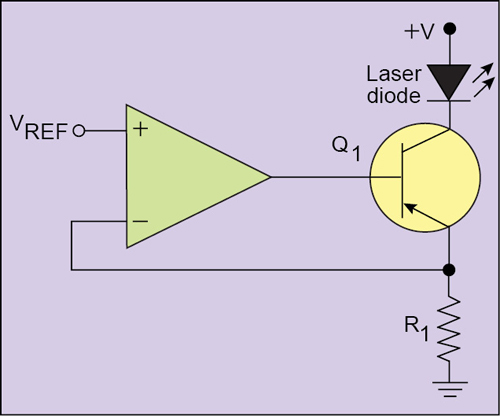
While semiconductor diode lasers, or simply laser diodes, are extensively used in a range of laser devices intended for tactical military applications, such as short and medium-range laser rangefinders, proximity sensors, short-range laser dazzlers and laser aiming devices, it needs to be emphasised here that they are invariably used as the optical pumping source for all Nd:YAG laser-based military systems.
Laser-diode electronics primarily comprises a constant-current source that can provide to the forward-biased laser diode the desired magnitude of current and also has in-built features to provide protection to the device against all those parameters it is adversely sensitive to. The other important circuit block is the temperature controller that can maintain the laser diode junction at the desired value of constant temperature irrespective of ambient temperature. The need for a precise constant-current source and constant-temperature operation arises from the dependence of laser-diode wavelength on drive current and operating temperature. Not all laser-diode applications, including military applications, have stringent requirements of ultra-stable wavelength necessitating a high degree of current and temperature stabilisation, though for efficient and reliable operation, stability of drive current and operating temperature are always desirable.
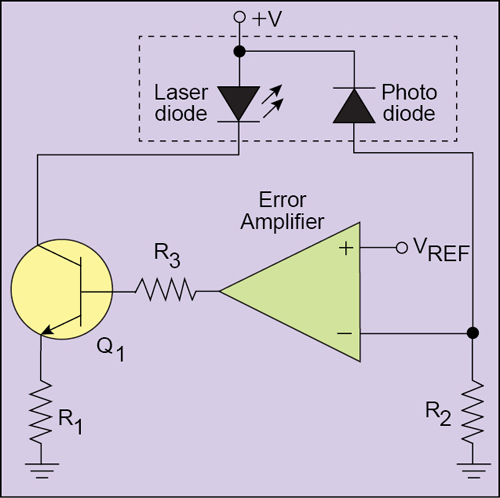
Although laser diodes exhibit excellent reliability under ideal operating conditions, these are highly susceptible to damage due to excessive drive current, electrostatic discharge (ESD) and transients. Laser diode damage manifests itself in the form of one or more of the following problems, namely, reduced output power, shift in threshold current and increase in beam divergence and failure to laser action, thus producing an LED-like output only.
Relevant damage mechanisms are overcurrent, overheating, current spikes and power-line surges. Improper grounding and shielding lead to radiated electrical transients. Improper power-line conditioning also leads to severe fast transients. ESD caused by improper handling during storage, transport and mounting is considered as the single leading cause of premature laser diode failure.
Constant-current and constant-power operational modes
There can be two possible circuit topologies the laser diodes can be operated in, namely, constant-current and constant-output power modes. Operating temperature is of course an important factor in both the modes. In view of dependence of laser diodes’ performance on operating temperature and drive current, the preferred mode of their operation is the constant drive current with precise control of operating temperature. Constant-current operation without temperature control is generally not desirable. Even at constant drive current, output power would increase with decrease in operating temperature. With significant decrease in temperature, output power could easily go past the absolute maximum value.
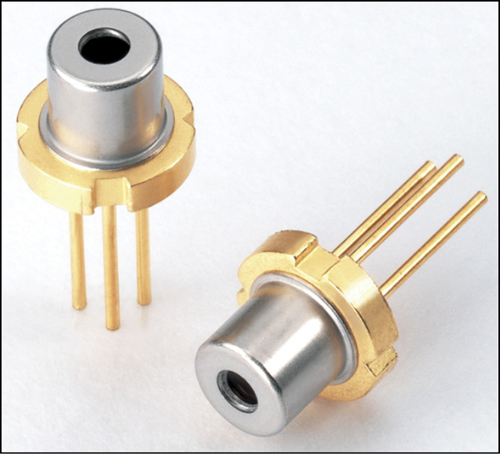
photodiode
The circuit topology in the case of constant-current mode of operation is usually configured around a current- sensing element that continuously senses the drive current and produces a proportional voltage. This is then compared with a reference voltage representing the desired value of drive current to generate an error signal. The error signal, after suitable conditioning, is fed back to restore the drive current to the desired value. Fig. 1 shows the basic schematic arrangement of constant-current drive circuit.
Practical circuits with in-built protection features are far more complex. Typical constant-current drive circuits and related design issues are discussed in the following paragraphs.
There are applications where constant output power is more relevant. In such a situation, direct dependence of output power on drive current can be exploited to maintain a constant output power. Even when a laser diode is driven by a constant current, the heat dissipated at the laser-diode junction leads to rise in temperature and hence fall in output power. Increase in temperature could be because of absence of any active temperature control mechanism or even inadequacy of heat sink in the presence of active temperature control. This reduction in output power can be compensated by increasing the drive current. The current source can be designed in such a way that it adjusts the drive current in a feedback mode to maintain a constant output power instead of maintaining a constant drive current. Fig. 2 shows the basic circuit topology. The basic circuit topology of constant-output- power drive circuit is similar to that of constant-current drive circuit, except for the nature of sense signal, which in the present case is a photo current proportional to the output power.
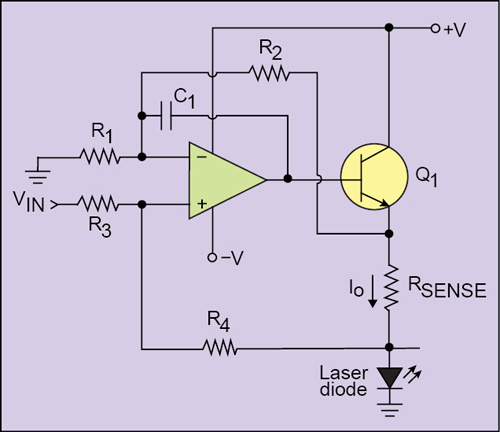
grounded load
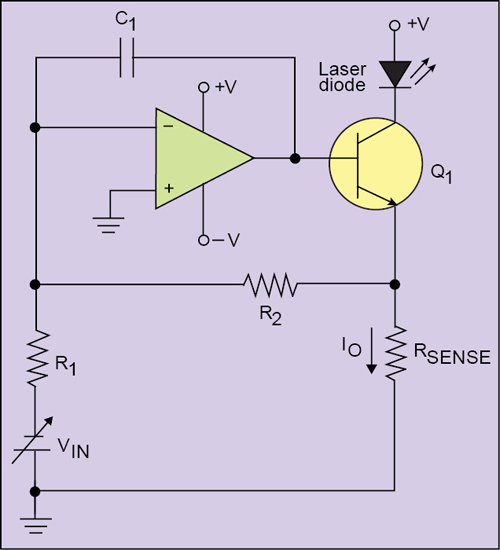