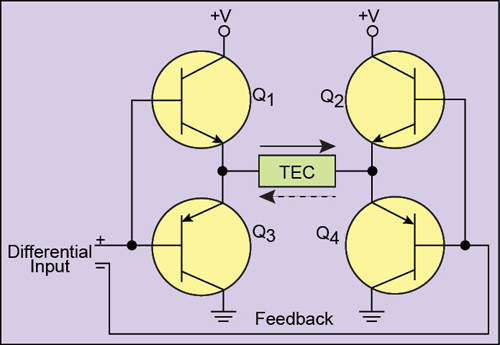
half-bridge circuit
In the case of quasi-CW operation of laser diode arrays used for optical pumping of solid-state lasers, peak- current-pulse amplitude typically varies from a few tens to a few hundreds of amperes. The current drive stage in this case is usually a cascade arrangement of a drive and control stage and a power stage. Drive and control stage is a preamplifier stage with some kind of control feature that allows to vary the amplifier gain and hence the drive current to the power stage. Fig. 10 shows the block schematic arrangement of a typical quasi-CW laser-diode drive circuit.
The circuit operates as follows. The astable multivibrator produces a train of pulses having pulse width and repetition rate at which the laser diode or laser-diode array needs to be driven. Soft start in-built into the circuit provides protection against damage due to instant power on. Power stage contains the active device(s) and associated circuitry capable of delivering required current pulse amplitude.
The drive and control stage could be configured either around discrete bipolar transistors/metal-oxide-semiconductor field-effect transistors (MOSFETs) or an op-amp with JFET as one of the gain determining elements. The power stage could be configured around one or parallel connection of more than one bipolar transistors or MOSFETs. The sensing element is usually a resistor connected in series with the diode or diode array. The peak pulse voltage across the sense resistor representing the peak amplitude of current pulse is amplified and then subsequently stretched. The stretched pulse train, after filtering, is fed to a differential amplifier stage where it is compared with a standard reference to produce an error voltage. The error voltage here represents deviation of peak amplitude of current pulse from the desired value. The error voltage is added to a fixed bias and fed to the control element in the drive stage to control the drive current to the power stage.
Again, a large number of manufacturers internationally offer compact laser-diode drivers for OEM market catering to the requirements of CW, conventional pulsed and quasi-CW operational modes. Fig. 11 shows photograph of one such laser-diode driver for quasi-CW operation. One cannot miss the bank of capacitors connected across the DC supply input to provide high peak current drive capability required in such an operation.
Laser diode temperature control circuits
Laser diode junction gets heated due to power dissipated at the junction, and one of the methods to remove heat away from the junction is by using a heat sink. This passive technique of heat removal using heat sink becomes impractical for moderate-to-large power-diode lasers. Also, it cannot be used to operate the laser diode at a temperature lower than the ambient temperature, nor can it be used to stabilise the temperature. Use of an active temperature stabilisation mechanism therefore becomes essential while working with moderate-to-high-power-laser diodes and also in low-power laser diodes where application demands precise temperature control. Thermoelectric (TE) cooling device based on Peltier effect is the heart of such a system. A practical TE module is usually a two-dimensional array of P-N couples connected electrically in series and sandwiched between two thermally conducting and electrically insulating faces (Fig. 12). Both single-stage and multiple-stage TE cooler modules (Fig. 13) are commercially available. Multiple-stage modules offer higher cooling/heating capacity and maximum differential temperature specifications.
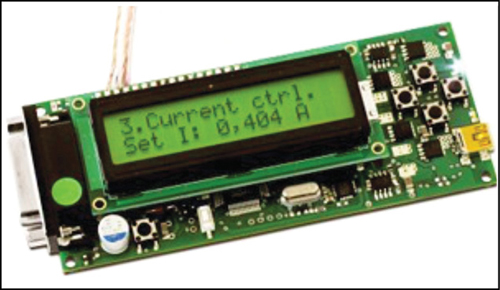
TE-cooler-based active temperature stabilisation circuit uses TE module as the control element, a temperature sensor and a properly designed feedback loop. The TE cooler is a reversible solid-state heat pump whose operation is based on the Peltier effect. According to the Peltier effect, when electric current is passed through a junction of dissimilar metals, heat is created or absorbed at the junction, depending upon the direction of flow of current. The heat transfer according to the Peltier effect takes place in the direction of flow of charge carriers.
A TE module literally pumps heat from one place to another, heating one face and cooling the other in the process. Whether a particular face becomes hot or cold depends upon the direction of current flow through the TE module. Thus, by controlling the magnitude and direction of the current drive to the TE module, it can be used as a control element in a temperature stabilisation circuit. The TE module pumps the heat dissipated in the laser diode on to a heat sink mounted on the supposedly hot face of the TE module. The heat is transferred from heat sink to the ambient.
TE modules are characterised by maximal performance parameters, namely, maximum temperature difference ΔTMAX at zero heat load, maximum heating capacity QMAX for zero temperature difference, device currentIMAX measured at ΔTMAX, terminal voltage VMAX corresponding to IMAX with no heat load and coefficient of performance (COP), which is the ratio of pumped heat load to electrical power supplied to the device.