- The 3D printer is so fast that is has the ability to switch between different printing materials rapidly while ensuring that the size and texture of the printed object is consistent throughout.
- Design engineers involved in creating flexible electronics products can take advantage of this new technology for fast and efficient execution of their projects.
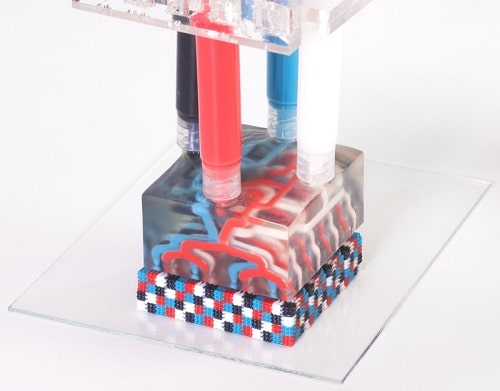
The invention of 3D printers has proved to be a great boon for designers who can now realise their complex ideas without worrying about the involved cost. However, there is one problem.
Conventional 3D printers take quite a long time to build a single material. And if a project requires multiple parts to be connected later, then that time could extend even more.
Now, it seems this issue has been resolved. A new technique called Multimaterial Multinozzle 3D (MM3D Printing) developed by engineers at Harvard’s Wyss Institute for Biologically inspired Engineering and John A. Paulson School of Engineering and Applied Science (SEAS), allows seamless switching between up to eight different materials with a single nozzle. This makes the 3D printer capable of precisely printing complex 3D objects in much less time as compared to traditional 3D printing methods. And that too at a high resolution.
Fast switching of printing materials
The process with which this is achieved is interesting. The 3D printer uses high-speed pneumatic actuators that apply pressure to multiple ink channels that later converge in a Y-shaped junction inside the printhead. This provides quick and continuous switching between up to eight different printing materials that flow through the nozzle. Each nozzle can switch materials 50 times per second, which is faster than what the human eye can detect. Add to that an array of multiple nozzles and the 3D printer can simultaneously print even more complex shapes, which reduces time even more.
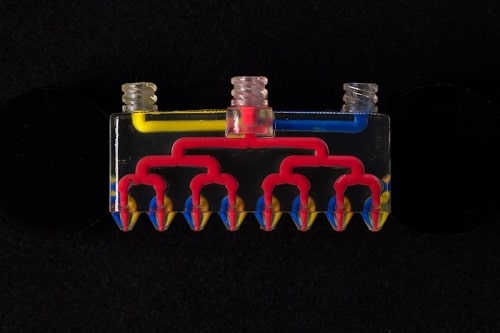
“When printing an object using a conventional extrusion-based 3D printer, the time required to print it scales cubically with the length of the object, because the printing nozzle has to move in three dimensions rather than just one,” said Mark Skylar-Scott, Ph.D., Research Associate at the Wyss Institute. “MM3D’s combination of multinozzle arrays with the ability to switch between multiple inks rapidly effectively eliminates the time lost to switching printheads and helps get the scaling law down from cubic to linear, so you can print multimaterial, periodic 3D objects much more quickly.”
One-way flow
At the printhead, precise tuning of the nozzle shape, printing pressure and ink viscosity prevents ink from mixing or flowing back into the static ink channel when pressure is applied at the Y-shaped junction. By using fast pneumatic actuators, a rapid and continuous one-way flow of ink from nozzle/nozzles enables creation of a 3D multimaterial part. This one-way flow is akin to railway signalling, where only one train can run on a particular railway track (in order to avoid collision with another train).
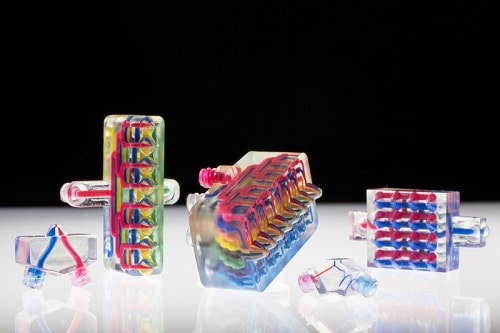
Flexible robotic movement
The researchers used MM3D printing to create a soft robot that has rigid and soft elastomers on different rows and connected with embedded pneumatic channels. By alternating the positions of the rigid elastomers between each row and sequentially compressing and decompressing the pneumatic channels, the soft robot is able to walk (much like a millipede, albeit slowly).
“Because MM3D printing can produce objects so quickly, one can use reactive materials whose properties change over time, such as epoxies, silicones, polyurethanes, or bio-inks,” said co-first author Jochen Mueller, Ph.D., Research Fellow at the Wyss Institute and SEAS. “One can also readily integrate materials with disparate properties to create origami-like architectures or soft robots that contain both stiff and flexible elements.”
During a test run, the soft robot was able to move at nearly half an inch per second and carry a load eight times its own weight.
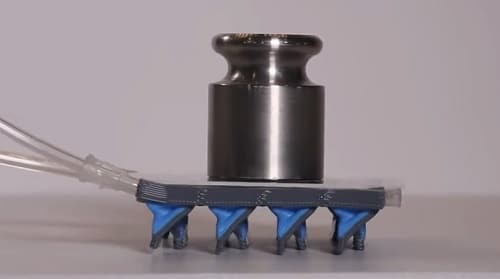
Further development for increased complexity
At present, the research team is further modifying MM3D printing to enable individual nodes to produce different inks for creating even more complex patterns and objects.
The above publication titled ‘Voxelated soft matter via multimaterial multinozzle 3D printing’ is available in Nature.