Read Part 5
Beginning with a brief introduction to various techniques and related sensors, this concluding part of the article focuses on optronic triangulation and time-of-flight sensors for position and displacement measurement and velocity screen used for measurement of projectile velocity during detonation.
Optronic sensors are at the core of a large number of optronic instrumentation setups used for a variety of applications in detonics. Some representative examples include interferometric sensors for blast pressure measurements, visar (an acronym for velocity interferometer system for any reflector) sensors for measurement of surface velocity of solids, spectrometric and spectroscopic sensors for measurement of fireball temperature, chirped-fibre Bragg grating (CFBG) sensors for measurement of detonation velocity, and triangulation and time-of-flight sensors for measurement of position and displacement caused by blast loading and laser velocity screen for measurement of velocity and aiming accuracy of projectiles of different calibres.
Beginning with a brief introduction to various techniques and related sensors, this concluding part of the article focuses on optronic triangulation and time-of-flight sensors for position and displacement measurement and velocity screen used for measurement of projectile velocity.
Common optronic sensors with applications in detonics depend for their operation on one or more of the following techniques. These include laser interferometry, laser velocimetry, laser spectroscopy, spectrometry, laser triangulation and laser time-of-flight ranging. Laser velocity screen is also based on time-of-flight principle, where time taken by the projectile to travel a known distance is used to compute projectile velocity.
Interferometric sensors
Interferometric sensors have demonstrated tremendous potential in the measurement of blast parameters such as peak-over pressure, pressure-time history, detonation velocity, shock-wave phenomenon and so on. Fabry-Perot cavity sensors, for example, can be used for the measurement of peak-over pressure and pressure-time history resulting from explosive blasts.
A pressure sensor comprises a fibre-optic probe (Fig. 1) and an interrogation system for Fabry-Perot cavity-based pressure sensor. The system involves exciting the fibre-optic probe with a broadband laser radiation through a fibre-optic coupler. A part of laser radiation enters Fabry-Perot interferometer terminated in a pressure-sensitive diaphragm. Two laser beams—one reflecting from the front face and the other reflecting from the diaphragm interfere—produce a fringe pattern. Interference pattern is processed further to extract pressure information in terms of peak-over pressure and pressure-time history.
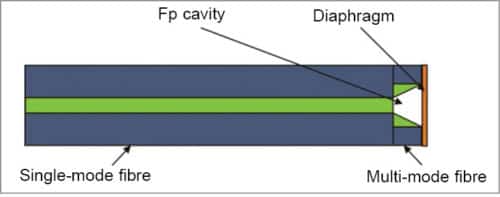
Visar uses laser interferometry to measure surface velocity of solids moving at high velocities. It is a useful diagnostic tool for measuring shock-wave velocity of matter in extreme conditions, and is used in many laboratories as a tool to study high-pressure shock. Visar measures changes in Doppler shift of light reflected off a moving surface to compute velocity and velocity-time history.
Doppler shift appears in the form of fringes. Measurements made at different times give velocity-time history, which, in turn, gives the shock-wave profile. Velocity is computed as the product of magnitude of fringe shift and a parameter called velocity per fringe.
Chirped-fibre Bragg grating sensors
A CFBG is a grating sensor having a periodic pitch. Grating is characterised by three important parameters: grating period, refractive index and length of grating. Fig. 2 shows the schematic of one such grating in which grating period is increasing linearly with the length of grating. In this figure, λ1<λ2<λ3<λ4
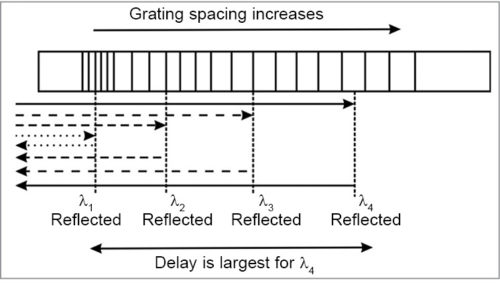
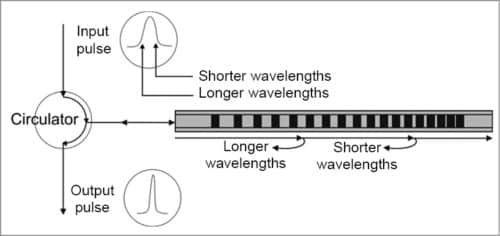
Another linearly-chirped grating could have a linearly decreasing grating period (Fig. 3). These gratings are Bragg reflectors, and wavelength of incident light that would be reflected from a particular point along the length of grating depends on the grating pitch at that point.
As is evident from the CFBG of Fig. 2, shorter wavelengths (or higher frequencies) are reflected off nearer points and longer wavelengths (lower frequencies) are reflected off farther points. A sensor of this kind can be very effectively used to measure position, velocity and pressure resulting from a blast. It can also be used to measure temperature due to temperature dependence of wavelength. It measures total light return of an incoherent or a broadband light source reflected off a linearly-CFBG sensor in contact with the explosive (Fig. 3).
The circulator isolates input and output optical signals. Assuming flat emission and detection profiles over CFBG length, the operation depends on the linear relationship between wavelength-integrated reflectivity and CFBG length. Complete instrumentation comprises a CFBG sensor and an interrogation system.
Spectroscopic sensors
Both atomic emission and ultraviolet (UV) absorption spectroscopy have been used for the measurement of fireball temperature of explosive blasts. While emission spectrometry is effective for the measurement of fireball surface temperature, UV absorption spectroscopy is effective for the measurement of temperature of fireball core. Atomic emission spectrometry for fireball temperature measurement makes use of intensity of light emitted at a particular wavelength to determine temperature (Fig. 4).
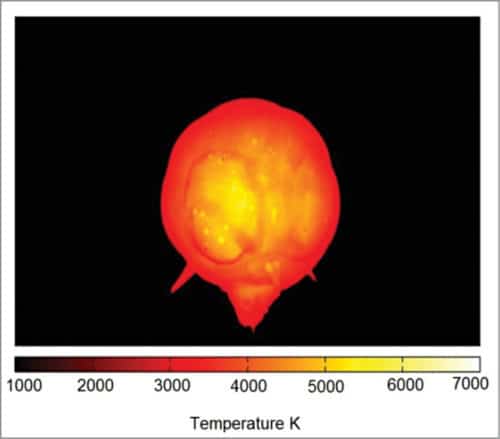
In the case of optically-dense fireballs, temperatures derived from emission measurements may be representative of only the outer edge of the fireballs. Preferred method in such cases is UV absorption spectroscopy, which provides quantifiable information on the temperature of the core. Dye laser pumped by third harmonic of Nd-YAG laser is generally used for UV absorption spectroscopy.
Proximity sensors
An optronic proximity sensor is a type of laser rangefinder designed to accurately measure relatively smaller distances to target, as compared to those encountered in conventional laser rangefinders used in tactical battlefield applications, such as observation, surveillance and fire control.
A conventional battlefield laser rangefinder measures distance to target. Range information is displayed to the observer when the device is used in observation and surveillance role, or fed to a fire control computer in a fire-control application. In the case of a proximity sensor, processing circuitry generates a command signal when distance to target is equal to the preset distance value within a certain specified tolerance.
Command signal, in turn, could be used to perform a variety of control functions. In military parlance, the most common application of a proximity sensor is in a laser proximity fuse where command signal is used to initiate detonation of warheads of large artillery shells, aviation bombs and guided missiles.
A number of laser-based range-finding techniques have been exploited successfully for building military rangefinders. These include time-of-flight, phase shift, and frequency-modulated continuous-wave (FM-CW) and triangulation methods of range finding. Suitability of each technique for a given application depends on targeted range, desired range accuracy, range update rate and so on.
In time-of-flight technique, a narrow pulse-width laser beam is transmitted towards the intended target. Target range or distance to target (d) is given by:
d=(c×∆t)/2
where d=target range (m), c=speed of light=3×108m/s and t=time interval between transmitted and received laser pulses.
Range accuracy in this case depends on receiver processing speed, and rise and fall times of laser pulses. Range is measured as the time interval between rising or falling edges of the transmitted pulse and the corresponding edge of the received pulse. Uncertainty due to finite values of rise or fall times causes range inaccuracy. Received pulse is processed in a high-speed counter, and clock speed determines processing speed.
Time interval and, hence, range-to-target is measured in terms of number of clock pulses counted by the time interval counter, that is, started by the start pulse corresponding to the leading or trailing edge of the transmitted laser pulse and stopped by a stop pulse corresponding to the leading or trailing edge of the relevant received pulse. In terms of number of clock cycles, distance-to-target is given by:
d=(c×N)/(2׃CLK)
Here, N is the number of clock pulses counted between start and stop signals, and ƒCLK is clock frequency. Range inaccuracy in this case is given by ±c/2ƒCLK
Worst-case range inaccuracy equals one clock period. Range resolution is determined by laser pulse width, which implies that the laser rangefinder based on time-of-flight principle cannot discriminate between two targets separated in radial range by a distance corresponding to the distance travelled by light in a time period equal to pulse width.
In phase-shift technique of range finding, the laser beam with sinusoidal power modulation is transmitted towards the target, and the diffused or specular reflection from the target is received. The phase of received laser beam is measured and compared with that of the transmitted laser beam. Phase shift is 2 times the product of time-of-flight and modulation frequency. This allows computation of time-of-flight and, hence, distance-to-target from known values of phase-shift and modulation frequency.
Higher modulation frequencies can result in a higher spatial resolution. Phase-shift method appears similar to time-of-flight, as phase shift is proportional to time-of-flight.
FM-CW laser range-finding technique is similar to the one followed in the case of its radar counterpart, that is, FM-CW radar. In this, frequency of a narrow line width laser is modulated with a ramp or sinusoidal signal, collimated and then transmitted towards the target. Received signal corresponding to the reflected laser beam, specular or diffused, is mixed with the reference signal representing the transmitted laser beam. Beat frequency produced as a result of homodyne detection is used to derive range information.
Distance-to-target (d) is given by:
d=(ƒB×c×TR)/(4×∆ƒ)
where ƒB is beat frequency, TR is ramp waveform time period and ∆ƒ is modulation frequency bandwidth.
In triangulation technique, range is determined by using simple laws of trigonometry. Fig. 5 shows the basic principle of operation of a laser triangulation proximity sensor. The sensor has a transmitting channel usually configured around a semiconductor diode laser or a passively Q-switched diode pumped solid-state microchip laser along with associated transmit optics and a receiving channel comprising receiving optics, PIN or APD sensor, and range-processing circuitry.

As shown in the figure, transmitted laser beam reflected from the target located at three different distances produces beam images that are displaced across the active area of the photo sensor. The receiver is designed to produce the focused laser beam spot at the centre of the active area for preset value of proximity distance.
There will be a distance both longer and shorter than the desired distance where the focused beam spot falls just outside the active area. Distance-to-target (d) from the laser transmitter location can be computed from known values of length (l) between transmitter and receiver and angles, (α) and (β), using the following equation:
d=(l×sin β)/sin(α+β)
Here, α is the angle made by line-joining transmitter and receiver and line-joining transmitter and target, and β is the angle made by line-joining transmitter and receiver and line-joining receiver and target.
This forms the basis of operation of a laser proximity sensor in general and laser proximity fuse in particular. Performance of a laser proximity sensor can be enhanced by using an axially-symmetric arrangement of multiple aperture photo sensors, as shown in Fig. 6. The design offers better ballistics due to centre of gravity being located on the longitudinal axis of the ammunition round and higher signal-to-noise ratio (SNR) due to averaging of multiple return signals.
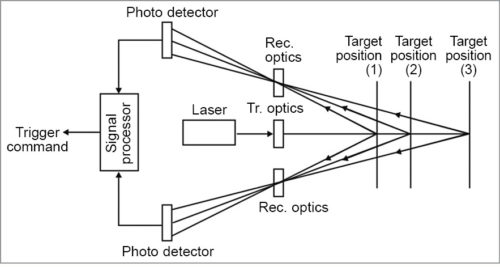
Theoretically, all these range-finding techniques, namely, time-of-flight, triangulation, phase-shift and FM-CW, can be used to build laser proximity sensors or laser proximity fuses. Triangulation technique is better suited for designing laser proximity sensors or fuses, as it can measure short distances down to a few metres with high accuracy. Range accuracy, however, falls off rapidly with increasing distance. In some cases, time-of-flight laser rangefinders have also been used to build laser proximity sensors.
Time-of-flight laser displacement or proximity sensors
Recent advances in laser technology have made possible the development of highly-miniaturised laser transmitters that can produce several tens of kilowatts of peak power in 1ns – 2ns laser pulses. These lasers are also capable of range update rates in excess of 500Hz, which is an essential requirement for proximity fuses used in artillery shells and aerially-dropped bombs.
An artillery shell or an aerially-dropped bomb has a travel velocity in the range of 200mps – 500mps in the terminal phase. At 500mps, it travels one metre in two milliseconds. This implies that, minimum range update rate to get a range resolution of one metre is 500Hz.
Also, miniaturised optics and high-speed APDs in SMD packages have led to the development of compatible receivers. To add to this, these laser modules are available in different wavelengths, prominent among these being 905nm, 1064nm and 1550nm. One such compact laser rangefinder module of DLEM family from Jenoptik is shown in Fig. 7.
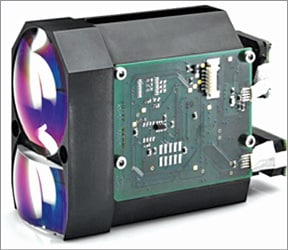
The latest addition to DLEM family, DLEM-20 weighs just 33 grams and measures ranges up to 5000m with an accuracy of 0.5m. It measures 50mm×22mm×34mm. DLEM-20 is ideally suited for handheld and weapon-mounted optronic systems. Its usage as of now as a proximity sensor or fuse may be limited due to maximum update rate of 25Hz.
Another laser rangefinder module for OEM applications that does not have the limitation of update rate is LDS30M from Astech (Fig. 8). LDS30M is an OEM laser module intended for distance measurements that require extremely fast data acquisition. It provides up to 30,000 range measurements per second.
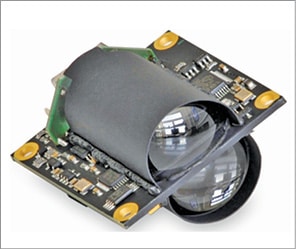
Laser triangulation displacement or proximity sensors
Laser triangulation sensors for building proximity sensors or fuses are available as commercially-off-the-shelf (COTS) modules. These cover a wide range of performance specifications in terms of maximum measurable distance, measurement accuracy, range update rate and so on. Almost all of these contain a solid-state laser source, which is generally a semiconductor diode laser, and a position sensing detector (PSD) or CMOS/CCD detector.
A laser beam is projected on the target whose distance from the sensor or whose surface displacement is to be measured under extraneous stress. A fraction of laser beam power is reflected towards the sensor. Reflected radiation, whose intensity depends on reflectivity of the target surface, is focused onto the detector through focusing optics. As the target moves, the laser beam proportionally moves on the detector, as shown in Fig. 9.
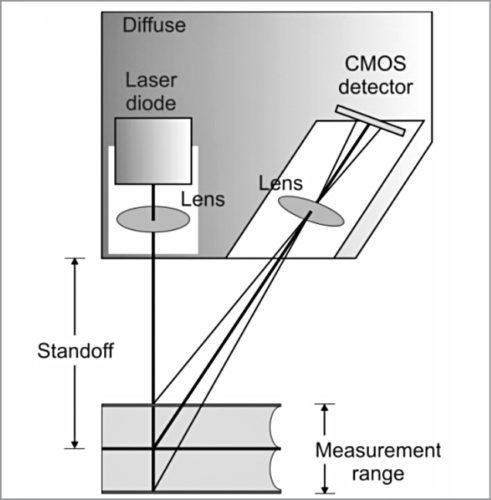
Detector signal is suitably processed to determine relative distance to the target. While CMOS and CCD sensors detect peak distribution of light quantity on a sensor pixel array to identify target position, PSD sensors calculate beam centroid based on the entire reflected spot on an array.
The sensor is interfaced to the PC. Multiple sensors may be used when the objective is to determine displacement produced in a metal surface or a structure under stress due to blast loading or other similar effects. These are connected through an Ethernet interface card. Fig. 10 shows the schematic of a typical multi-sensor instrumentation.
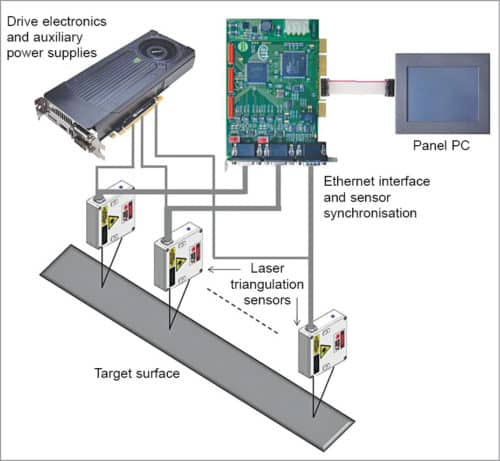
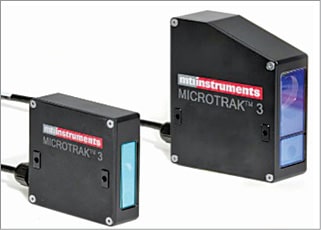
CCD and CMOS systems are typically more accurate over a wider variety of surfaces, because only the highest charged pixels from the reflected beam are used to calculate position. Lower charged pixels are usually energised by unwanted reflections from changing optical properties of the surface being measured and can easily be ignored during signal processing. This allows these to be used in a wider variety of applications.
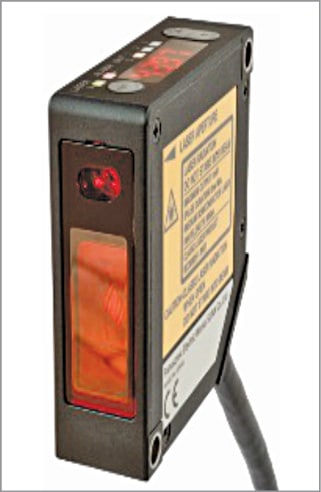
COTS laser triangulation sensors with a wide range of specifications of ranging distance, distance accuracy and range update rate are available from many manufacturers. Some representative modules from major international manufacturers include MICROTRAK-3 from MTI Instruments (Fig. 11), ILD-2300-200 from Micro-Epsilon, HL-G1 from Panasonic (Fig. 12), LDE-HS series from FAE (Fig. 13) and IL-2000 from Keyence.
These laser triangulation sensors represent a wide range of performance specifications in terms of stand-off range, measurement resolution and sampling rate. Triangulation sensors with stand-off range approaching a few metres, resolution approaching 0.01 microns and sampling rate of the order of a few hundred kHz are commercially available for a variety of industrial applications.
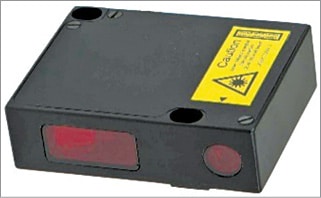
Laser velocity screen
A laser velocity screen is laser instrumentation comprising a two-dimensional array of optronic transmitter and receiver pairs. It is used for the measurement of velocity of projectiles of different calibres and travel velocities.
In addition to measuring projectile velocity, the instrumentation setup also measures aiming accuracy through the measurement of x-y coordinates of the projectile at two different planes that are spatially apart and parallel to each other, and orthogonal to the direction of travel of the projectile.
A two-dimensional laser screen may be created either by using separate transmitter and receiver pairs as shown in Fig. 14, or by using a laser transceiver unit on one side and a retro-reflector on the other.
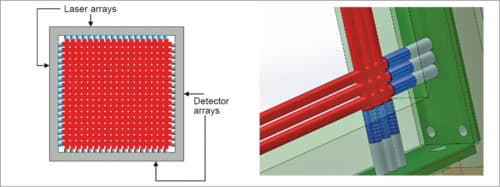
Yet another approach could be to employ a single transmitter, a single receiver and multiple retro-reflectors for each plane, as shown in Fig. 15. With laser screens of this type, one cannot determine coordinates and, hence, aiming accuracy of the projectile. Fig. 16 shows the block schematic arrangement of different sub-systems comprising laser velocity screen instrumentation.
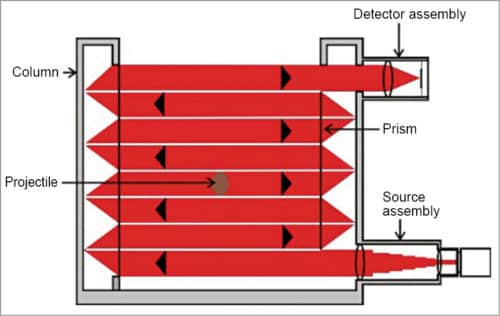
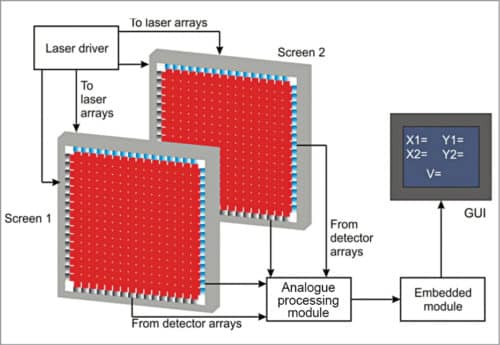
The integrated instrumentation functions as follows. Two screens are mounted parallel to each other, and spaced a known distance apart. In the case of laser screens using separate transmitter-receiver pairs, each of the two screens has two sets of linear semiconductor laser diode arrays located at right angles to each other in the same plane. Each linear array is aligned to a corresponding linear array of silicon PIN photodiodes. Assuming Cartesian coordinate system and that the centre of screen is the origin, we get two sets of collimated laser beams, one parallel to x-axis from linear arrays of laser diodes and photodiodes placed along y-axis, and the other parallel to y-axis obtained from linear arrays of laser diodes and photodiodes placed along x-axis.
The number of laser diode modules in the linear array, which is equal to the number of photodiodes, and the size of collimated laser beam are so chosen that at least one laser beam is interrupted by the smallest calibre projectile passing through it. As the projectile passes through the first laser screen, it cuts across one or more laser beams parallel to x-axis and one or more laser beams parallel to y-axis, giving x and y coordinates of projectile at that point. The resolution with which x and y coordinates of the projectile can be determined depends on the number of elements in the linear array.
Resolution for a given array size can be further improved by using a suitable interpolation algorithm. The second screen, spatially apart from the first screen, can similarly give x-y coordinates of the projectile at that location. Thus, we have x-y coordinates of the travelling projectile at two known positions along the path of the projectile. This information can be processed to determine the direction of movement, aiming accuracy and velocity.
Velocity is computed from time taken by the projectile to travel from one screen to the other. An extension of this concept could be creating a one-dimensional laser screen in the field for the measurement of velocity of fragments produced by a blast. Again, we would require two such screens. Width of screens could be a few tens of metres. Fig. 17 shows a representative set up of laser screens.
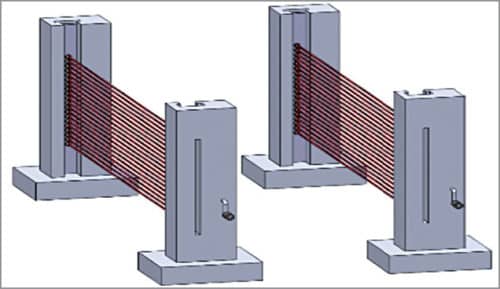
Dr Anil Kumar Maini was formerly outstanding scientist and director at Laser Science and Technology Centre (DRDO)
Nakul Maini is post graduate in optical engineering from University of Bristol (UK), currently working as senior engineer (product development) at Tek Xplore, New Delhi