Based on ultrasound technology, the robot can lift effectively lift a variety of tiny, delicate objects without damaging them
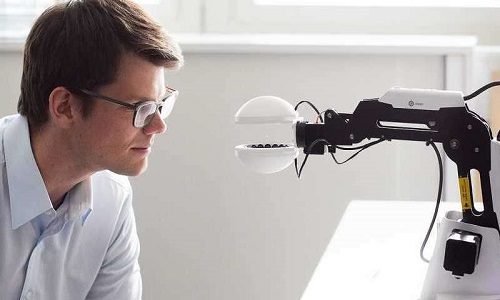
Robotic grippers are required for handling objects and materials that are quite fragile or large in number. However, a risk is present in getting these damaged due to the powerful grip of conventional robotic grippers.
Based on a technology similar to that used by robotic space explorers to operate in zero-gravity, a novel robotic gripper has been developed that can manipulate small and fragile objects without touching them. The technology used is based on acoustic waves.
Magnetic levitation
Comprising of two semi-spheres having the shape of a pair of headphones, the robotic gripper is connected to a circuit board that is embedded with several microchips.
These ultrasound waves are generated by numerous ultrasonic transducers fitted inside the inner body of the robotic gripper. As the waves travel, they superimpose each other, thus creating several acoustic pressure points and causing small objects to get trapped within them. As a result, these small objects are able to float freely in the air.
“This phenomenon is known as acoustic levitation,” states Marcel Schuck, lead researcher and former doctoral student, ETH Zurich.
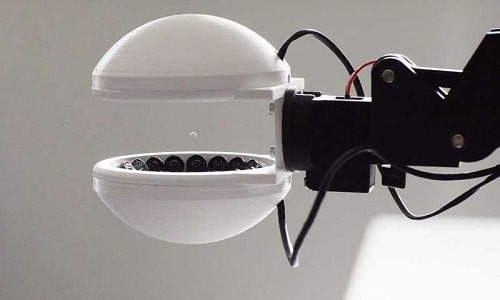
A software controls the movement of the ultrasonic transducers in real-time so that pressure points can be created in different directions. The software also adjusts the gripper according to the shape of the object that has to be lifted.
Delicate enclosure
To enable a precise and careful grasp of fragile objects, a layer of soft rubber has been placed along the inner surface and edge of the robotic gripper.
All this makes it possible to lift and manipulate small objects such as tiny mechanical devices and semiconductor chips without entirely touching them.
Saves money
When working with a conventional robot, different grippers are required for every new shape but the ultrasonic gripper eliminates this as it can effectively hold objects of varying sizes between itself. This helps save money, which otherwise would have been spent in purchasing an extensive set of expensive high-precision grippers.
“The exact positioning is determined by the acoustic waves controlled by the software,” Schuck explains.
Further improvements
Currently, these robotic grippers offer only limited positioning accuracy. The goal is to provide a variety of position movements without the suspended object falling to the ground. For this Marcel Schuck along with fellow researchers, Marc Röthlisberger and Christian Burkard are currently working upon techniques to achieve this.
Schuck intends to introduce the robot gripper along with the control software to the industry, especially watchmaking and chip manufacturing industries. “The main aim is to explore the potential fields of application and open doors within the industry,” Schuck says.
The researcher also plans to establish a start-up based on this technology by 2021, provided that positive feedback is received from the industry.