Connected car is the buzz word today. In reality, the connected car already relies on the Ethernet also known as vehicles Ethernet. From infotainment systems and backup camera connections, the Ethernet’s high capacity and versatility readily penetrates automotive segments.
Ethernet migration in the automotive market in 2016 is a new trend. The advanced driver assistance system featured in many vehicles is expected to expand the use of the Ethernet. Recent technological developments make the Ethernet viable for use in cars. As per estimates by Frost & Sullivan and Strategy Analysis, nearly 400 million vehicles Ethernet ports will be in use by 2020. By then, total number of vehicles Ethernet ports is expected to be higher than the total number of all other Ethernet ports combined.
Gigabit Ethernet is also in the pipeline in 2016. Emergence of 1000BASE-T1 standard in mid-2016 provides a roadmap for the vehicles Ethernet evolution. By 2020, it is estimated that 40 per cent of the cost of a car will be in electronics.
As automotive manufacturers are adding more and more computer based systems, applications and connections, cost of electronics content and the wiring harness to support these in terms of cabling, network interfaces and onboard computing power is growing. Ethernet deployment can, and will, reduce these costs.
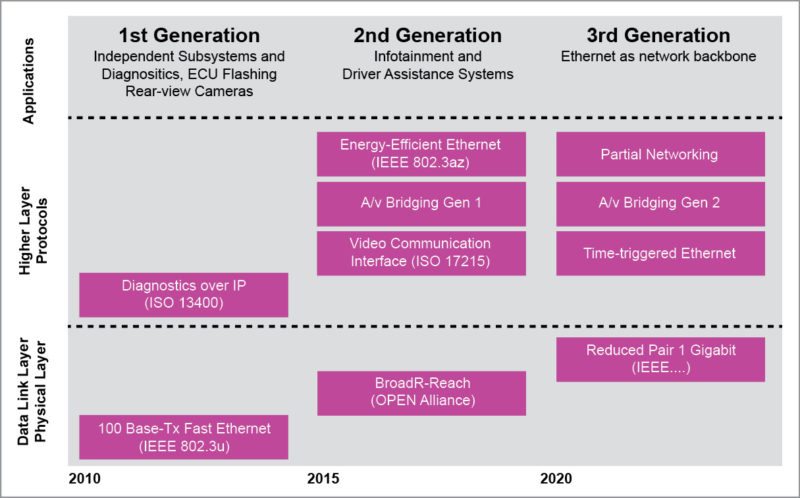
Media-oriented systems transport (MOST) currently dominates as a dedicated high-speed multimedia network technology for auto infotainment systems. MOST bus, based on a ring topology, uses synchronous data communication to transport audio, video and voice signals.
With Gigabit Ethernet, it could support many more streams than MOST at a higher data rate in higher resolution.
A vehicle today consists of an infotainment, advanced driver assistance system (ADAS) and control domains, each using MOST, Flexray, CAN, LIN, LVDS and the Ethernet. Even though the Ethernet has existed for over 20 years, it could not be previously used in automobiles due to the drawbacks like it did not meet OEM EMI/RFI requirements for the automotive market, was susceptible to alien noise from other devices in a car, could not guarantee latency down to the low microsecond range and did not have a way of synchronising time between devices and having multiple devices sample data at the same time.
Automotive Ethernet
Automotive Ethernet is a physical network that is used to connect components within a car using a wired network. It is designed to meet the needs of the automotive market, including meeting electrical requirements such as EMI/RFI emissions and susceptibility, bandwidth requirements, latency requirements, synchronisation and network management requirements. IEEE 802.3 and 802.1 groups where multiple new specifications are listed and revisions to existing specifications are done to meet automotive requirements.
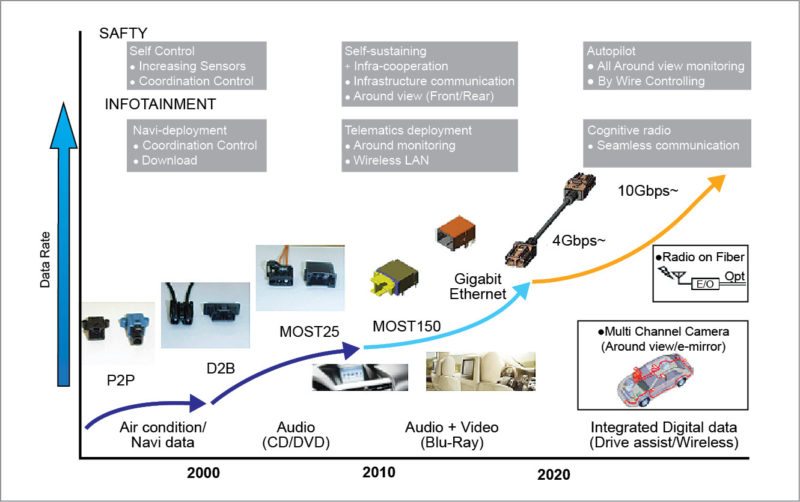
Automotive Ethernet, including 100BASE T-1 and 1000BASE T-1, is not like low-voltage differential signaling (LVDS), which is point-to-point serial connectivity. Automotive Gigabit Ethernet is capable of handling multiple video streams from many cameras. Other obvious places to use 1000BASE-T1 are in connecting multiple cameras and in a variety of infotainment systems. Main driving factors are cost reduction, efficiency and reduced time-to-market.
Technology has paved the way by developing a 100Mbit per second Ethernet physical-layer standard, specifically designed for automotive connectivity applications. It can run high-bandwidth data over a single-pair unshielded twisted-pair copper wire, cutting cable and connector costs, while reducing the weight of the wiring harness inside a car.
The standard’s layered approach enabled the development of new physical layer (PHY) specifications, media access protocols (MACs) and other capabilities, allowing it to keep pace with the demands of modern networks. Extensions to the original IEEE 802.1/802.3 standards now define practical solutions for providing security, deterministic performance, traffic shaping and many other application-specific functions, features and specifications. As a result, Ethernet has many capabilities that it needs to meet the unique demands of in-vehicle Ethernet networking.