In July this year, Changying Precision Technology Co., a manufacturer of mobile phone modules, set up the first fully-automated factory at Dongguan, China. Any time during the day or night, you can see 60 robot arms at ten production lines polishing the modules, a job that required 650 workers in the past. According to reports, 90 per cent of the factory’s workforce comprises robots, with just a few human workers to monitor the machinery.
Elsewhere in the world, Ports of Auckland plans to replace 50 jobs with Autostrads, which are 15m-tall automated straddle carriers. These container-stacking robots can stack up to four containers high and are expected to increase the container terminal capacity by 30 per cent.
The job for a robot does not necessarily have to be high-precision, as in the first case, or heavy-load as in the second, it could just be a routine job that needs to be done well. A wet-wipe maker, for example, recently signed up NEXCOM to design an automated system with Delta robots and EtherCAT master stations to coordinate everything from programmable logic controllers (PLCs), conveyors and sensors to gluing and labelling equipment. This move is expected to reduce manpower by around 30 per cent, while increasing productivity up to 1.5 packages per second.
Robots are being increasingly employed to automate innumerable tasks at manufacturing facilities across the world, not to forget their newfound jobs at homes, to make life easier and more comfortable. This article looks at the same trend, from angles that you might not have noticed before.
Coat-wearing robots
Known as laboratory robots, smart and efficient bots lend a helping hand in laboratories, too. These help in jobs like high throughput screening, chemical and biochemical synthesis, so that researchers’ time is freed for more strategic planning.
In a recent Laboratory Equipment story, Sam Michael, director of automation and compound management at National Centre for Advancing Translational Sciences (NCATS), USA, explains how the trend has shifted from large, monolithic robots to little robotic arms that have a special direct drive or magnetic drive.
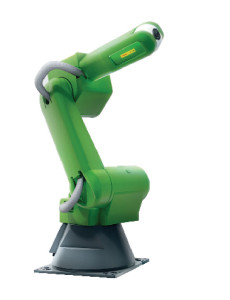
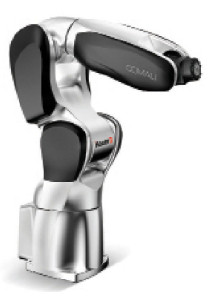
While the size has shrunk, their importance has increased manifold, especially at NCATS, which is a heavily-automated research lab that runs high throughput screening of compounds. It recently hit the news as Yale University researchers used the NCATS facility to discover that a drug, originally meant for cancer, could restore memory and reverse cognitive problems in mice with Alzheimer-type symptoms.
The Machine. An example of a machine that can quickly solve a problem is called, well, The Machine, which was developed by Dr Martin Burke of University of Illinois, Urbana-Champaign. His goal was to automate chemical synthesis, so that several Ph.D-level scientists could be freed from working for days in the lab to develop small molecules. The device developed by him, currently licensed to Revolution Medicines Inc., uses a building-block approach to try and replicate what is found in nature.
The Machine can assemble complex small molecules at the click of a mouse. The idea is to break down complex molecules into smaller, chemical-building blocks, all of which have the same connector piece and can be stitched together with a single reaction. Burke’s team automated this process, making The Machine work much like a 3D printer at the molecular level. They devised a simple catch-and-release method that adds one building block at a time, rinsing the excess away before adding the next one.
The team demonstrated that this device could build 14 different classes of small molecules. Essentially, it transforms small molecule synthesis from a highly individualised, customised process, to a more generalised automated approach, which has the potential to speed up new drug development.
Adam and Eve. One step ahead of being helpers in the lab, robot scientists like Adam and Eve are ready to develop drugs themselves. According to a University of Cambridge press report, robot scientists can, “automatically develop and test hypotheses to explain observations, run experiments using laboratory robotics, interpret the results to amend their hypotheses and then repeat the cycle, automating high-throughput hypothesis-led research.”
Adam, a robot scientist developed in 2009 by researchers at Universities of Aberystwyth and Cambridge, both in the UK, became the first machine to independently discover new scientific knowledge. In its wake comes Eve, a robot recently developed by the same team, based at University of Manchester, UK.
Eve can automate early-stage drug design by systematically testing each member from a large set of compounds in the standard brute-force way of conventional mass screening these compounds against assays (tests) designed to be automatically engineered and using statistics and machine learning to predict new structures that might score better against the assays.
Future versions of the robot might also be able to synthesise these recommended compounds. It is hoped that Eve can help identify new drug candidates for malaria and neglected tropical diseases such as African sleeping sickness and Chagas disease, which are killing millions of people every year.
Prof. Ross King, from Manchester Institute of Biotechnology at University of Manchester, says in a media report, “Every industry now benefits from automation, and science is no exception. Bringing in machine learning to make this process intelligent, rather than just a brute-force approach, could greatly speed up scientific progress and potentially reap huge rewards.”
Real helping hands
Known more scientifically as collaborative robots, these are a rising new clan of robots that can truly work side-by-side with humans. Imagine a robot lending a real helping hand, lifting a heavy object into a truck, the way you manually guide it to, just as two humans would lift it? The current generation of agile and safe industrial robots are really breaking out of caged production lines and working besides humans.
Experts say that, when man and robot share the same workspace, it creates fruitful synergies and productivity benefits by combining the strengths and benefits of the machine, such as reliability, durability and repetition accuracy, with human strengths such as dexterity and flexibility. However, this class of robots also requires special designs, in terms of greater flexibility, receptiveness to ad-hoc instructions and enhanced safety measures. For example, it must be possible for the robot to assess its co-worker’s position and classify it into safe zones, warning zones and unsafe zones in real-time. The robot should also be able to automatically adjust its own position to always revert to safe zone.
New components such as SafetyEYE, a 3D camera system that helps monitor protected fields and detection zones in several dimensions, aid in implementing human-robot collaboration.
Comau’s Racer3 is a recent example of a robot capable of working besides humans. It is a high-strength aluminium 6-axis articulated robot that can be mounted on benches, walls, ceilings or inclined supports. It has been designed for out-of-the-cage use in industries like food and beverage, electronics, plastics and metalworking. Speed and flexibility are what Racer3 really excels in.
According to the company’s official press release, “Racer3 is a natural contortionist that can bend like a snake until it assumes the shape of a scissor, surpassing the flange at axis 1. Or, it can close like a book, bringing the wrist toward the body to rotate the axis 1 at maximum speed while avoiding collisions with anything in the surrounding space. With a cycle time of less than 0.36 seconds for a 1kg pick-and-place cycle, the rigid construction and stable base ensures high precision and repeatability.”
Fanuc’s CR-35iA stands apart from common collaborative robots in the market, which are usually small payload varieties. This particular helper is capable of handling 35kg payloads, which according to the company is an industry-first. A soft green foam cover helps protect humans working around the robot, which reportedly meets ISO 10218-1:2011 robotic safety requirements and is designed to work alongside humans in operations such as machine tending, handling heavy payloads that require lift-assist devices or custom equipment, higher payload mechanical assembly, palletising or packing, and tote or carton handling.
Another recent example is Fetch Robotics’ team of vision-guided robots, Fetch and Freight. Fetch is an advanced mobile manipulator, while Freight is a mobile base. The duo is designed to work alongside humans in warehouse environments, performing tasks like warehouse delivery and pick-and-pack operations. Interestingly, the robots are built upon the open source robot operating system.
In addition to a range of sensors, grippers and so on, which help them do their job, the two robots are also fitted with components that help them navigate automatically and work safely with humans. In Fetch’s base, there is a charging dock, 25m range laser scanner for navigation and an obstacle-avoidance laser from German company SICK. It also features a 25m range 2D laser scanner used to detect workers and follow them at speeds of up to 2m/s.
Industrial wearables
The media has been abuzz about wearable devices for a long time now; from fitness wearables and health trackers to car-friendly wearables and personal assistants, we have read about these all. Interestingly, wearables are expected to be the next big wave in automation, too.
Healthcare organisations like Dignity Health and Stanford University Medical Center, manufacturers like Boeing, hoteliers like Palladium Hotel Group and Disney Resorts, as well as retailers like Tesco and Woolworths are experimenting with the use of wearable devices like fitness trackers, smart augmented reality (AR) glasses, voice-controlled headsets, wearable cameras and body sensors. These efforts are expected to improve speed, safety and efficiency while lowering costs.
In industrial spaces, wearable technology often takes the form of personal protective equipment (PPE). Protective and sophisticated, these technologies help safeguard users from workplace hazards. Mining firms, for example, are fitting workers with sensors that monitor air quality and alert them of danger zones.
On the other hand, some verticals have started using commercially-available wearable technology to augment technicians’ skills with extra information and guidelines. Architectural firms are using AR glasses, which superimpose valuable details like dimensions and soil quality, which are updated live as the architect moves about the site.
The oil and gas industry, one of the early adopters of wearable technology, uses Google Glasses for on-field maintenance technicians to access real-time information and instructions to fix malfunctioning equipment.
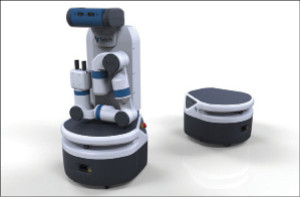
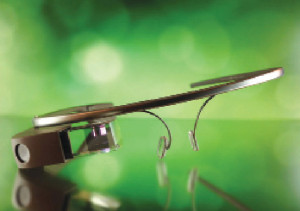
Google Glasses, despite all the speculation about the project’s shutdown and the impending re-emergence of Glass 2, seemed to be the spotlight at events like International Machine Tool Show and PackExpo in 2014. Beckhoff Automation, for instance, showed a proof-of-concept of Google Glass attached to a machine interface application running off its PC based computing platform. Novotek combined the Glass with GE’s Proficy Workflow software for hands-free expert guidance through process steps.
Smartwatches are also proving to be quite useful on the industrial front, thanks to being supported by tools like Schneider Electric’s Wonderware SmartGlance 2014 R2, which helps monitor, visualise and analyse real-time plant and industrial process data using mobile devices. APX Labs, a known name in smartglasses based applications for automotive, aerospace, oil, gas and energy industries, recently launched a smartwatch-friendly version of its popular Skylight software. This would enable factory workers and engineers to access checklists, alerts, information, applications and systems necessary to do their jobs in a more hands-on fashion.
Trend-watchers predict that soon smartrings could also be used to alert field technicians of an urgent requirement or warn workers of a potentially-dangerous condition.
So, it is evident that from brainy (robot scientists) and brawny (collaborative robots) to tiny (wearables), technology is coming to us in many glamorous and useful forms, to automate tasks and improve efficiency at locations ranging from labs and factories to mines. This trend is all set to improve, because the need is real. And of course, profitable, too!